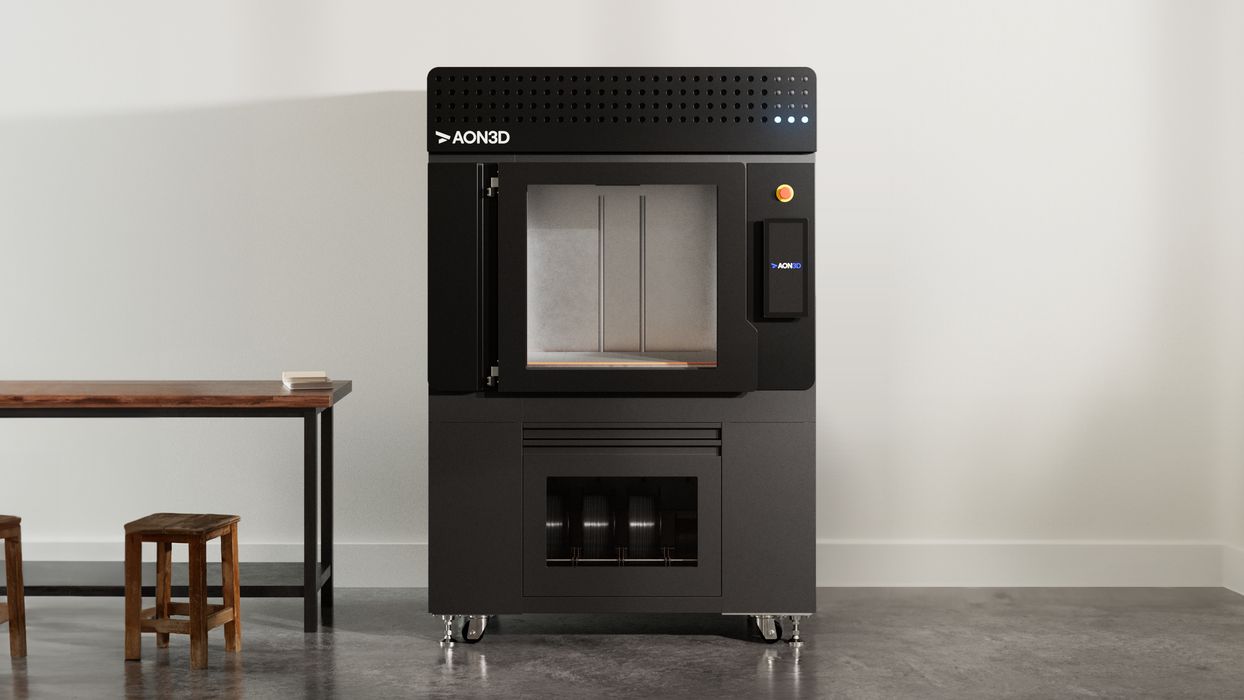
AON3D announced an intriguing new 3D printer that’s driven by a new AI-powered software system.
The Montreal-based company has been specializing in high temperature 3D printers for quite a while, so they’ve learned a considerable amount regarding how to — and how not — to print tricky materials.
That seems to be the focus of the announcements.
There were two items announced: the Hylo, a new industrial 3D printer, and Basis, a software tool to accompany the printer.
First, the Hylo.
It’s a fully enclosed high temperature-capable 3D printer, with a large build volume of 650 x 450 x 450 mm. The build chamber can be heated up to a whopping 250C, enabling printing of high temperature materials.
The Hylo includes a dual independent “IDEX” extrusion system, which can print at speeds up to 500mm/s. With that in mind, one could also say the Hylo is a high speed 3D printer.
However, AON3D is calling the Hylo a “smart” 3D printer instead. That’s because it has an incredible 25 different integrated sensors in the machine, which are together able to provide considerable information about ongoing print jobs.
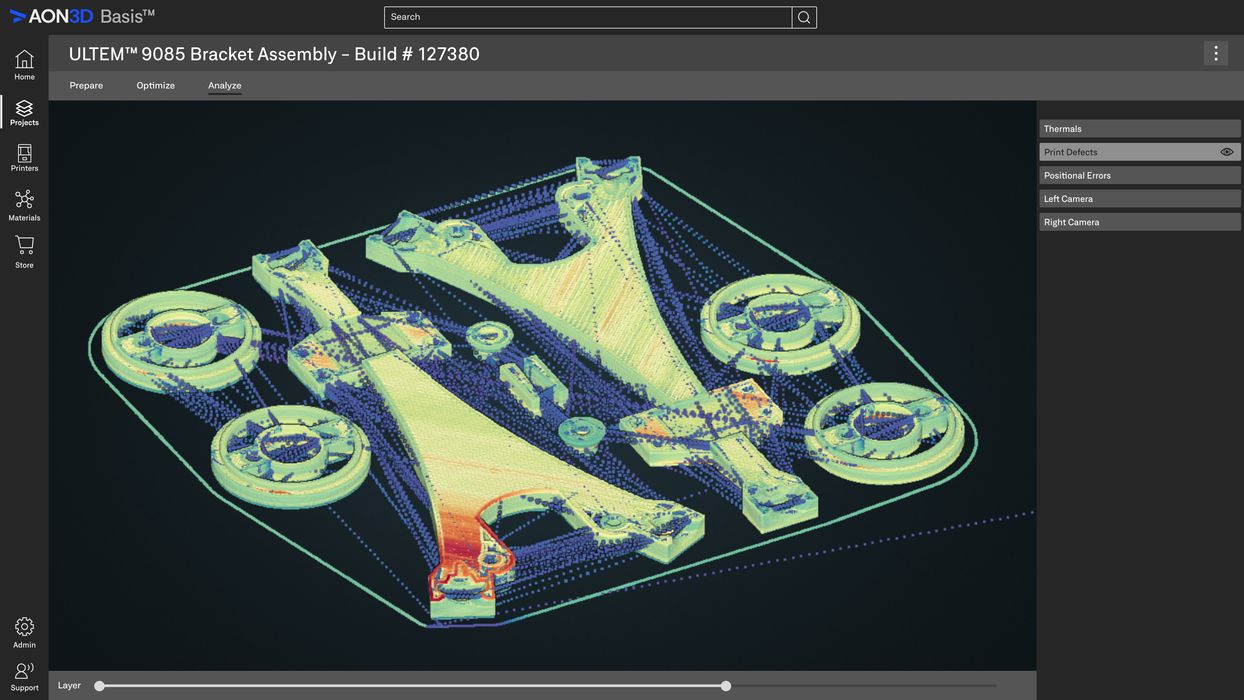
Basis is a smart slicing system that takes advantage of the data collected by the Hylo. Through simulations, it’s apparently able to prepare jobs for the system that ensure quality results.
It’s not quite clear how exactly they do this, but they mention that the real time monitoring and closed loop design of the Hylo are able together with Basis to produce the results.
AON3D is being a bit mysterious about Basis. They explain:
“While complete details are not yet released, AON3D Basis™ adds material-specific thermal awareness to the slicing process, dynamically tuning process parameters to optimize properties such as layer weld strength, dimensional accuracy, surface finish, and more.”
This sounds incredibly interesting, and may be unique among industrial 3D printers.
Why is AON3D doing this? It seems they have been through a great deal on their journey to print engineering materials. They believe (correctly) that printing high performance polymers has been very challenging on current 3D printers because of a lack of information and monitoring.
The print process always has some variability, so the key is to take action at the right moment to provide necessary corrections. That just isn’t done in most of today’s equipment. AON3D explains this very well:
“Current material extrusion printers rely on workaround solutions, like reducing variability by locking down materials and process settings or using “one size fits all” process parameters e.g., print speeds and thermals. When combined with a printed part’s unique features, these limitations lead to visible/hidden defects, print failures, variable part performance, and the perception that high performance polymers are hard to print.”
The are so correct here: “certified materials”, proprietary spools, print profile libraries are all simply approximations to get close to what the machine should really do: adjust itself on the fly to make perfect prints.
That seems to be what Hylo and Basis will do.
Via AON3D