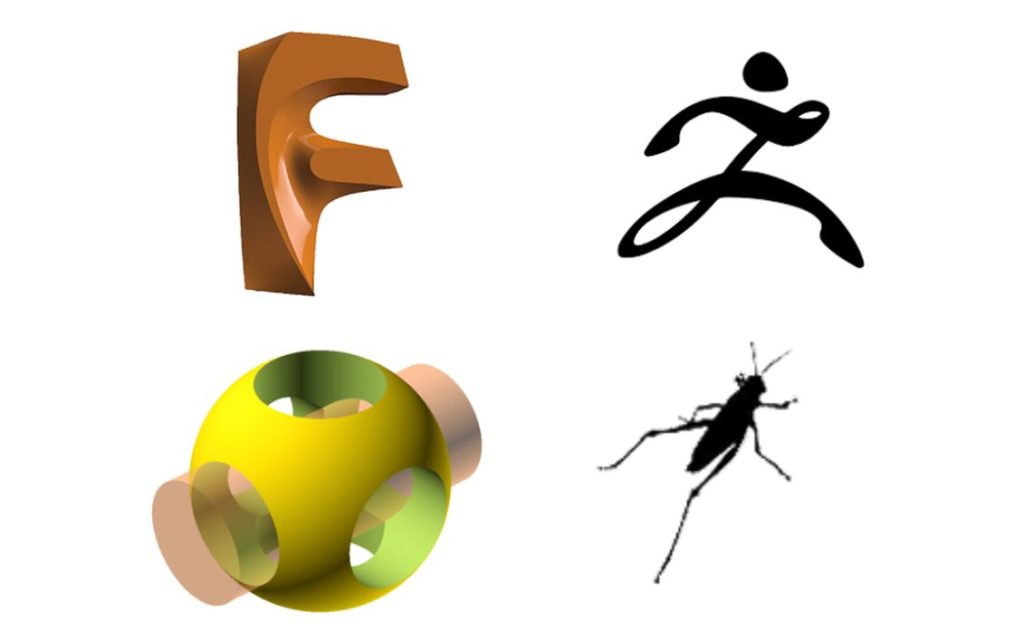
There are dozens of different software tools to produce 3D models for 3D printing, but all fall into four categories.
The goal of all 3D CAD systems is to produce a 3D model that’s used for either visual use or for manufacture. The manufactured 3D models must be watertight and usable by 3D print slicing software to prepare print jobs.
That’s the end point of the CAD workflow, but the method of getting there can be quite different. Because of this there are several different styles of CAD systems that each address different needs for the development of 3D models.
Those unfamiliar with CAD systems might be baffled as to why there are different styles. An analogy that can help understand this is the following: MS Excel can do anything, if you want it to. But should you? Wouldn’t you want to prepare a document in a word processor, even though it could technically be done in Excel?
That’s the situation here: the idea is to pick the right kind of CAD tool for the job, or in this case, the model. Certain kinds of models are best made using certain styles of CAD tools.
I’ve divided the world of CAD tools into four stylistic categories. Let’s take a look at which are best for different types of applications. But keep in mind you could theoretically use any of them to do the job; it must might be more difficult to do so.
Solid
What I’m calling the “solid” style is the most commonly found approach. Here we have tools that can build complex 3D objects by combining basic solid shapes. For example, putting a cone on top of a cylinder could create an arrow 3D model.
More advanced “solid” tools are parametric. This means the basic shapes can have dimensions that are numerically specified. This ensures the 3D model produced is of a predictable size and geometry. Note that some tools include 2D “sketching” tools that can be used to build more complex 3D shapes if required.
Example Tools: SOLIDWORKS, Autodesk Inventor, Autodesk Fusion 360, SolidEdge
Best For: Creation of mechanical parts that require specific dimensions, particularly assemblies of moving parts.
Not For: Artistic shapes, sculptures or modifying complex 3D scan data. Also not optimal for creating very complicated geometries.
Sculpting
“Sculpting” is an alternative interface for developing a 3D model, and it uses a sculpture paradigm. Generally, a base shape is established, which is then modified by manual 3D “touches” to that shape. Shapes are pushed, pulled, grooved, textured, etc. in a gradual manner until the desired shape is achieved.
Example Tool: ZBrush
Best For: Artistic works, particular 3D character development where organic shapes are required. Sometimes it is easier to handle 3D scan data with sculpting tools.
Not For: Creation of mechanical parts or highly complex shapes.
Programmatic
“Programmatic” is a very different approach than the “what you see is what you get” interface on other CAD styles. Here instead the designer provides a series of programming statements that, when executed from start to finish, build the required geometry. You should have some understanding of programming before attempting this CAD style.
Programmatic interfaces are also inherently parametric, as the statements must include numbers to indicate the dimensions of what is being generated.
Example Tool: OPENSCAD
Best For: Simple or complex mechanical parts, depending on the capabilities of the programmer. Can also use dimensions generated by algorithms to create highly complex shapes.
Not For: Organic shapes involving complex and unpredictable curves. Models good for sculpting would not be good for Programmatic tools.
Generative
“Generative” is a new class of tool in which the designer numerically specifies the “goals” of the design. For example, a part might have to withstand a certain amount of downward force at a specific temperature. Once all the conditions of use and goals are set, the system will use advanced computational techniques to “generate” a 3D model that meets those requirements. The results are typically very unusual geometries that would likely never be made by humans, yet they perform the required function, often optimally so. Pioneered by Rhino/Grasshopper, the technology has now been made much more automated by other tools.
Example Tools: Rhino/Grasshopper, nTopology, Live Parts
Best For: Producing highly optimized lightweighted parts for advanced applications. Unusual complex artistic works can also be generated.
Not For: Reproduction of classic shapes or sculptures.
CAD Combinations
Some CAD software producers manage to combine two or more of these modes together into a single tool, where the interface can be swapped as required. Perhaps the best example of this effect is with Autodesk Fusion, which offers Solid, Sculpting and Generative tools all bundled together. Hint: this is why the product is called “FUSION”.
The unfortunate problem here is that each tool tends to take a considerable effort to learn and become competent. Thus we often find designers continuing to use their favorite (or only) tool to design items that might best be done in another mode. If it’s at all possible, try to learn more than one interface.
Like any tool, 3D CAD options should be selected carefully to ensure you have the right tool ready for your creative efforts.