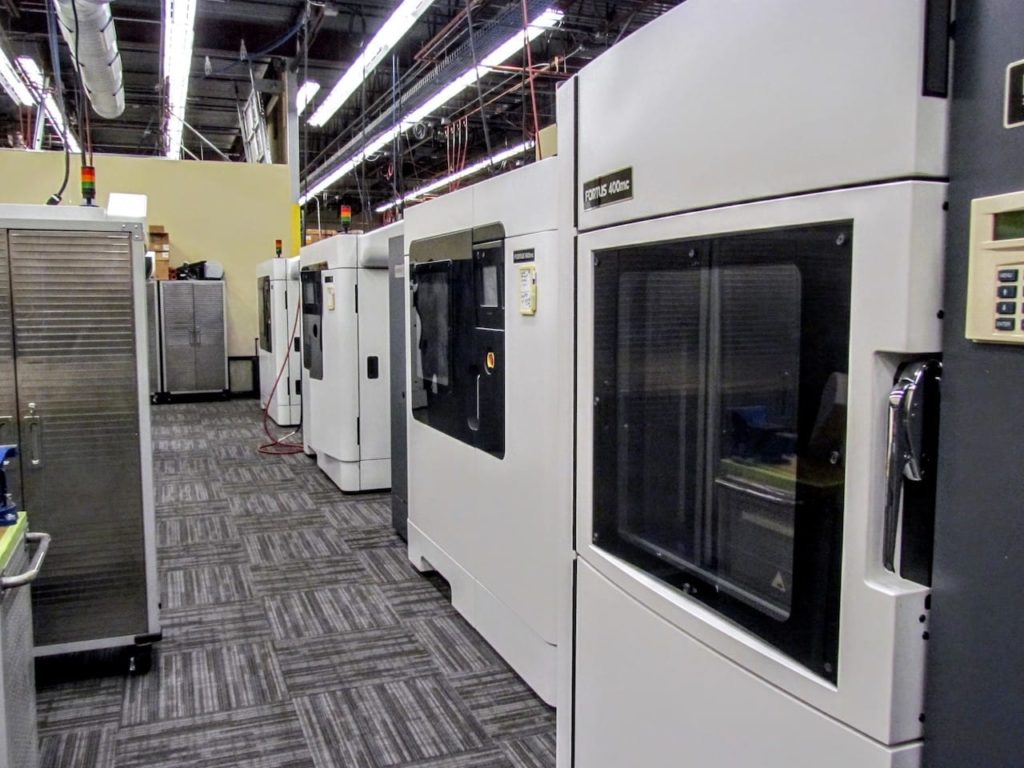
What are the remaining barriers to mass use of additive manufacturing?
Sure, this year will be the biggest ever in terms of use of additive manufacturing technology, but in spite of that there is a very long way to go. Traditional mass manufacturing approaches dominate and may do so for a long time yet.
It might seem far-fetched now, but what if we imagined a future where factories were far more generalized, leveraging the ability of 3D print technology to literally make something different during each production run? These “anything factories” would produce items in any volume required, and dominate the world of manufacturing.
Hold on a moment, that’s not really possible.
Or is it? It seems to me that if the following five barriers were overcome, we could see a world like that described above slowly come into view. Let’s look at the biggest barriers to widespread additive manufacturing.
Materials
How many possible materials are there? I’m not exactly certain, but it’s a lot. Much more than a lot. Materials are highly numerous, and new additions occur every day. They are used everywhere in all manner of applications. The breadth of material usage is vastly larger than the most common materials you could name.
However, the current state of additive manufacturing offers an incredibly constrained list of possible materials. There are still a great many applications that simply cannot be done using additive processes because the materials are not currently available.
Sometimes it’s only a matter of certification, but at other times the material itself is incompatible with known 3D printing processes for one reason or another.
The solution is two-fold: first, many, many more materials need to be qualified for use in additive systems. Secondly, new 3D printing processes must be developed to handle other more challenging materials.
That may sound like a big ask, but researchers are at this very moment developing multiple new processes that could potentially close the materials gap.
Speed
An injection molding system can knock out thousands of parts per day, vastly more than could be attempted by even the fastest 3D printer. That speed advantage current poses one of the toughest barriers to breach.
It’s because of money. Each part produced by a machine defrays a little bit of the cost of the machine acquisition and operation. The more parts produced, the lower the cost burden each part must take on. Therefore, a faster printer would produce more parts in a given time, lowering the effective cost of the parts.
Throughput might be thought of as a solution, but not really: while you’re producing more parts per time period, you’re paying for more 3D printers, too. Thus the cost of the parts doesn’t drop as much as it should.
One answer that might be on the horizon here is Volumetric 3D Printing, in which objects are “materialized” in a vat of photopolymer in only seconds or minutes. This process could end up being as much as 100X as fast as existing additive processes, and shows it could be possible to leap the speed barrier.
Cost
Speed is directly related to the cost of a 3D printed part as above, but there’s more to the story.
The cost of a 3D printer can be vastly more than the cost of an “equivalent” conventional manufacturing machine. Even worse, the cost of 3D print materials is still far too high. Filament in particular is problematic because its physical form requires an extra processing step between raw pellets and the 3D printer. There is a cost for that step, and it’s reflected in the cost of the filament.
Powders are also notably expensive, as many LPBF processes require specific quality levels to be met for proper printing.
The costs of materials and machines must be lowered, and my suspicion is that this will be addressed through more advanced, lower cost machines that use more commonly available materials.
Design
While the technology exists or may come in the future, there is another barrier to mass adoption: design.
The best applications of additive manufacturing occur when the technology is fully leveraged by unique designs. We often forget that almost all current part designs are unconsciously influenced by the requirements of traditional making processes.
Once designers lose those habits we may see an explosion of radical and powerful part designs that can only be produced on 3D printers.
Demand
Why 3D print advanced parts when no one wants them? If everyone wants the same style of shoe as a million other people, then why 3D print the shoe when you can make them with traditional mass manufacturing processes?
But what if people expected parts and products to exactly meet their own requirements? What if clothing, furniture, anything you touch was expected to be made to fit you? Would a mass manufactured standard part fit into that world? Sure, there are standard parts required for some applications, but there is plenty of room for personalized parts that would best be produced with 3D printers.
When the majority of consumers begins to expect customized products, then we will see a shift towards additive processes.
The Future
As of today these five are still the biggest barriers to AM adoption. But while they may be high, there are many people working to bring them down.
Eventually, they will.