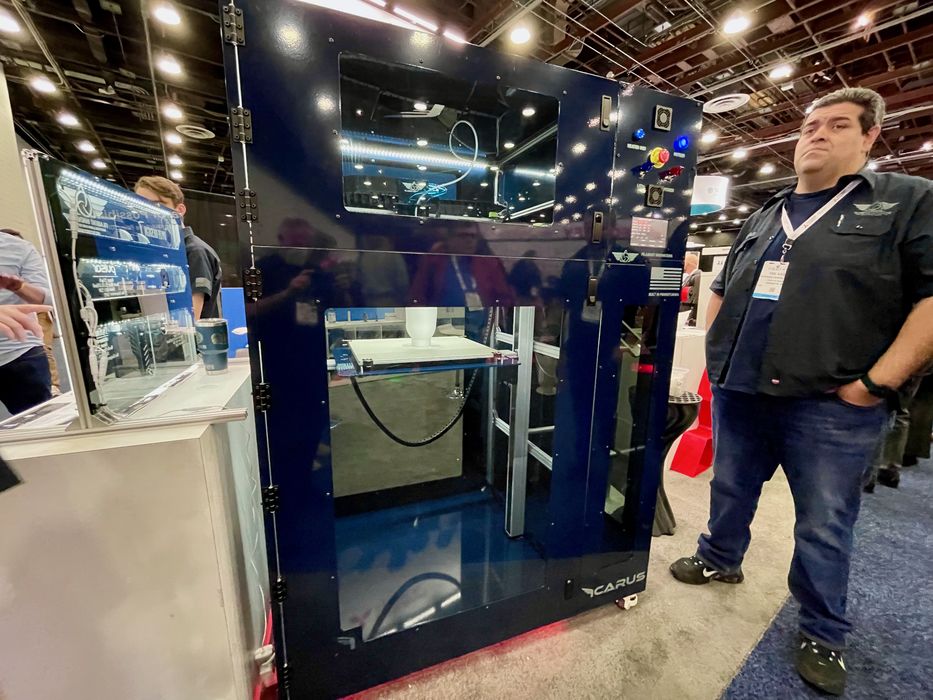
Filament Innovations’ flagship 3D printer is the huge ICARUS generation 5 device.
Filament Innovations is a Pennsylvania-based company that’s been around since it was launched in 2015 by founder Mike Gorski building 3D printer kits in his bedroom. Now the company is much larger and operates a 5500sf factory, producing serious 3D printing gear including the ICARUS.
The ICARUS is an imposing device, as you can see from our image at top. The floor-standing device has a truly massive build volume of 460 x 380 x 950, placing it in the same category as other large-format 3D printers such as those made by 3D Platform or BigRep.
One of the most common issues found with large format 3D printers is the speed of printing. If using typical components used for smaller devices, the print duration can be exceptionally lengthy when printing huge objects. By “lengthy”, I’m talking days or even weeks.
That doesn’t seem to be an issue with the ICARUS, however, as they’ve engineered the device to output up to 2lbs (900g, or almost an entire 1kg spool of filament) in a single hour. Another measure is that this is about 200 cubic mm per second. To put that in perspective, consider how long a typical desktop FFF device might take to run through an entire spool; the ICARUS can do the same in little over an hour.
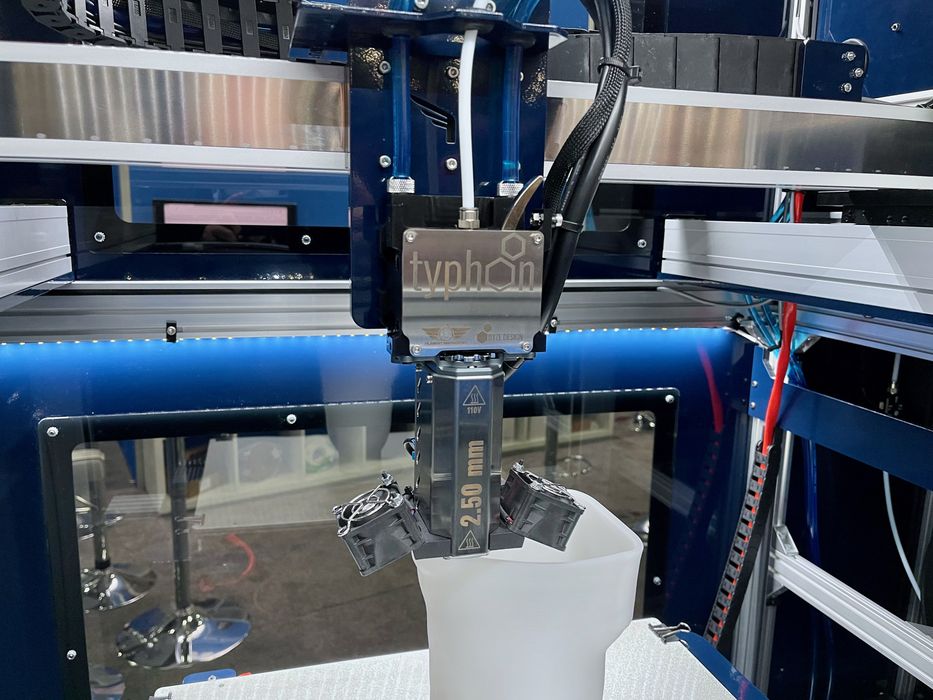
How does it achieve this incredible print speed?
It’s a combination of factors, including a well-designed frame and motion system. But the key seems to be the use of a Daze Design High Flow Typhoon extrusion system.
The Typhoon is an incredible system, involving a “quad pinch” gear system to grip filament like nothing else, dual heating zones to ensure softening of the thermoplastic regardless of how fast it passes by, and precision temperature sensors.
The Typhoon also requires 2.85mm filament, which is becoming a rarity in the world of 3D printing these days. However, for high speed systems it does make sense because the goal is to push as much material through the system as possible. 2.85mm filament offers 2.65x as much cross-sectional area as 1.75mm filament.
The entire build chamber is enclosed, and the print surface can be heated up to 110C, enabling the use of many advanced engineering materials through the 450C hot end. Filament Innovations said the ICARUS can 3D print in PLA, PETG, ABS, Nylon, TPU, TPC, ASA, PVA, HIPS, BVOH, PC, PET, Carbon Fiber Reinforced, Fiber Reinforced, Wood Reinforced and many more material types.
Filament Innovations has included a number of closed loop circuits in the ICARUS to ensure print quality and reliability.
To be clear, this is a large device, weighing in at over 200kg, so it’s definitely not a desktop device and is intended for workshop or factory use.
The ICARUS is built to order, requiring about a month to put together a machine. List price for the ICARUS is US$31,000.