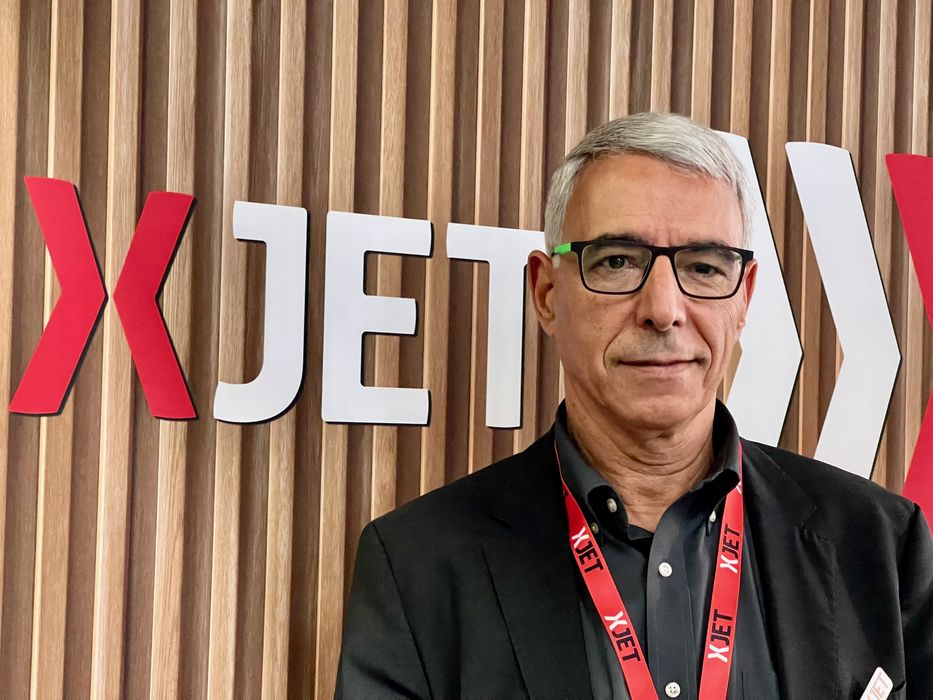
Today we talk a lot about 3D printing or additive manufacturing, but perhaps that will eventually fade away.
Now, let’s be clear, I’m not saying the technology itself will fade away. Instead I believe we’ll think about it differently.
This came up in a lengthy discussion with XJET’s Executive Chair, Avi Cohen, where we talked about the future of the technology.
Cohen believes things will eventually change. He said:
“General Motors doesn’t care how parts are made; they just have to meet the qualifications.”
This is a similar concept to what we were told by GKN Additive’s John Dulchinos: companies want finished parts, not printed parts.
In other words, it doesn’t matter how the parts are made. Companies are focused on building their products and to do so they require parts that meet the engineering requirements only.
Think about it: a robot or human assembling a product has no idea where a part came from, nor would they care. If it works, it’s good.
Sitting with Cohen discussing this topic in the midst of a major 3D print show with exhibitors touting their 3D printing technologies was a stark place for Cohen to say:
“Our industry is overly focused on technology.”
But he’s quite correct: the customers buying additive manufacturing gear are primarily interested in making their manufacturing efforts easier and more profitable. If that can be done with 3D print technology, so be it. But if another tech came along that was better, they’d quickly move on. The tech doesn’t matter; the resulting parts do matter.
Cohen continued:
“Eventually 3D printing must be fully automated, just as CNC shops are today. We need technology that leads toward full automation. There are just too many steps when using 3D printing today.”
Today’s most advanced factories more closely resemble a single large machine, rather than a collection of separate devices. The latter is how most 3D printers are built today, although there have been some efforts to work towards Industry 4.0.
Sliding a typical 3D printer into a smoothly running integrated factory environment is a bit problematic. Processes must be adapted to accommodate the less automated 3D printer, and that’s generally not good. Most
Why is this the case? Why would 3D printers be built in this way when manufacturers expect something different? Cohen has the answer:
“Most 3D print company founders didn’t come from manufacturing.”
This is also true. In all the 3D printing companies I’ve encountered, which must number in the hundreds at this point, I’ve rarely if ever met a founder that was from manufacturing.
The most typical story is someone attempting to invent a product using a 3D printer, and finding it to be inadequate. To resolve the issue, they end up building their own superior 3D printer and market it as a standalone device. Almost all of today’s 3D printers have this as their backstory.
This is likely a temporary situation, however, as 3D printer manufacturers gradually grow closer to manufacturers. The equipment that will be developed as a result of those closer relationships will eventually blend into the stream of manufacturing equipment used, and the fact that it might be a 3D printer will be incidental.
In a way, 3D printing could “disappear”, in the same way other manufacturing equipment has.
Via XJET