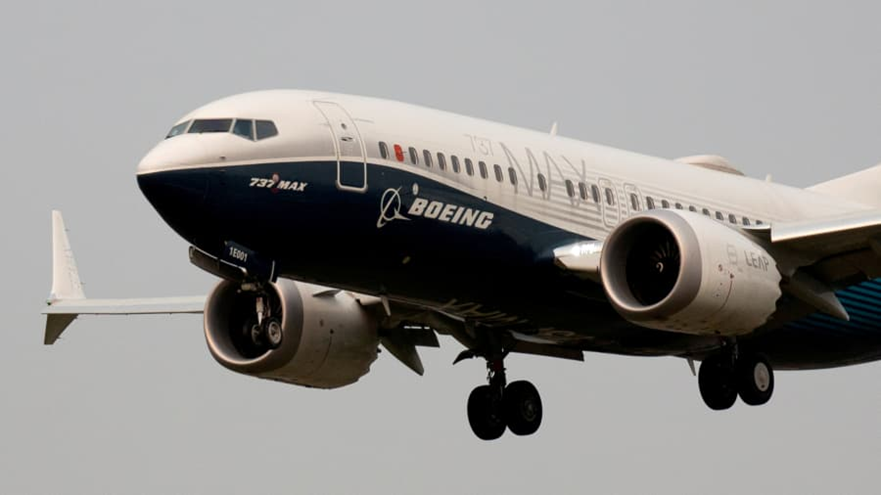
Charles R. Goulding considers potential 3D printing-related implications of a major aerospace competitive truce.
After 17 years of fighting over subsidies for Boeing and Airbus, the EU and the US have called for a five-year truce on retaliatory tariffs. In this writer’s opinion, this is a welcomed development since these kinds of disputes take companies away from what should be their main focus. The main focus should be technology advancement, fuel efficiency, high-quality safe plane production, and attention to consumer needs.
Both companies were severely impacted by COVID-19-related shutdowns impacting both business and consumer travel. The lucrative long flight segment is still in the doldrums. Fully functional used planes at much lower price points are available on the market. Boeing was crippled by the extended pre-pandemic, Boeing 737 product suspension, and COVID-19 remains prevalent in multiple countries in both the Eastern and Western hemispheres.
Both companies are confronting a new business environment as the markets recover. There is widespread supply chain disruption, including metals and semiconductors. Both companies also confront the emergence of a Chinese competitor called Comac, developing the C919, a rival to the Airbus A320 and the Boeing 737.
The New 3D Printing Offering
While the airframe manufacturers have suffered, the 3D printing industry has not stood still. Important innovation in the airframe industry occurs at Tier 1 and below Tier supplier levels, and those suppliers have embraced 3D printing.
Strong Tier supply chains have made the airframe industry the powerhouse that it is today. 3D printing has advanced in all of the major systems in an aircraft, including engines and components, avionics and electronics, and cabin features.
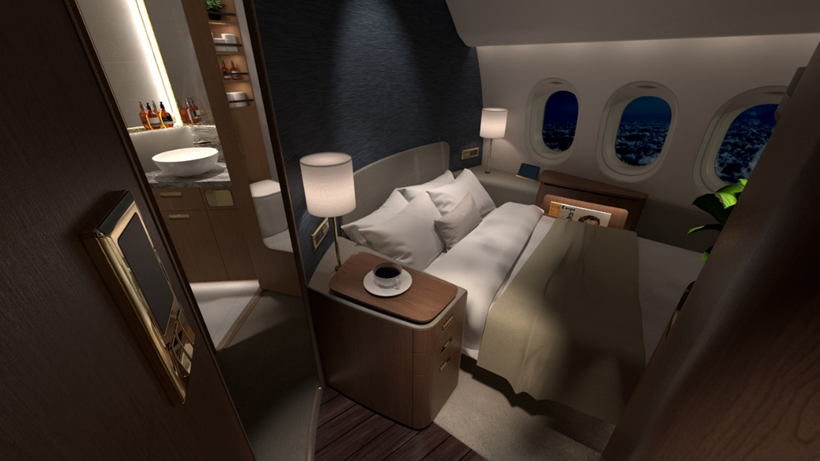
In particular, metal-related and electronics-related 3D printing has greatly improved. The further embracing of 3D printing has the potential to greatly improve the overall airframe product thereby making newly-produced planes the optimal choice, rather than opting for used planes. 3D printing topology results in fewer components, better components, and lighter components. Lighter components improve fuel efficiency and reduce emissions.
The new US-EU agreement calls for some type of R&D cooperation which hopefully involves 3D printing.
The Research & Development Tax Credit
The now permanent Research and Development (R&D) Tax Credit is available for companies developing new or improved products, processes and/or software. Eligible costs include U.S.-based employee wages, cost of supplies consumed in the R&D process, cost of pre-production testing, contract research expenses, and certain costs associated with developing a patent. As of 2016, eligible startup businesses can use the R&D Tax Credit against $250,000 per year in payroll taxes.
3D printing can help boost a company’s R&D Tax Credits. Wages for technical employees creating, testing and revising 3D printed prototypes can be included as a percentage of eligible time spent for the R&D Tax Credit. Similarly, when used as a method of improving a process, time spent integrating 3D printing hardware and software counts as an eligible activity. Lastly, when used for modeling and preproduction, the costs of filaments consumed during the development process may also be recovered.
Whether it is used for creating and testing prototypes or for final production, 3D printing is a great indicator that R&D Credit eligible activities are taking place. Companies implementing this technology at any point should consider taking advantage of R&D Tax Credits.
Conclusion
The five-year truce is a welcome development and hopefully will become permanent. During this period the 3D printing industry needs to make its improved offerings known to the industry and the Tier suppliers need to continually embrace 3D printing technologies.