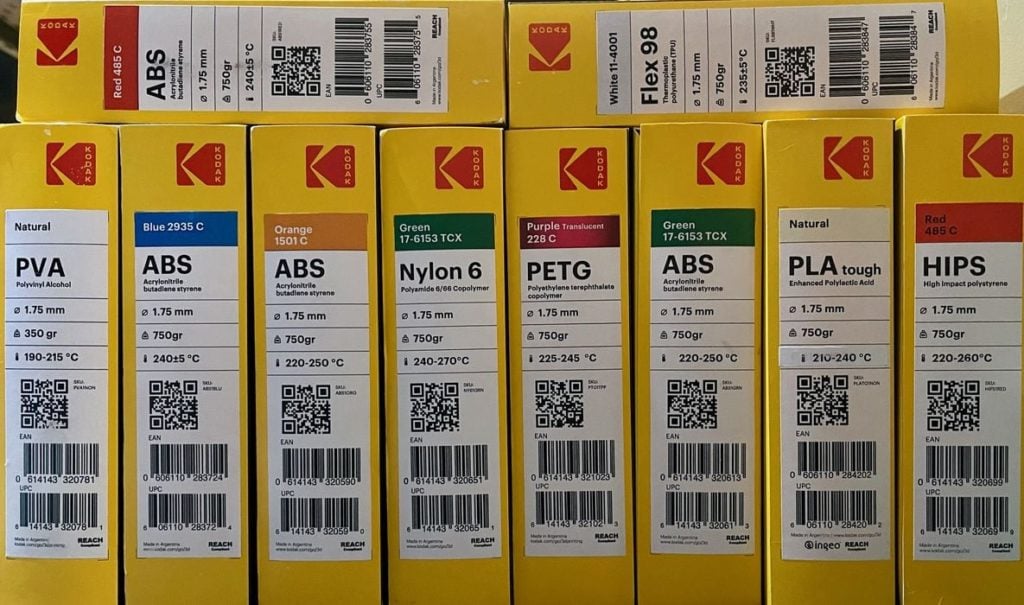
You just cracked open your new desktop FFF 3D printer. What filaments should you use?
Default Materials
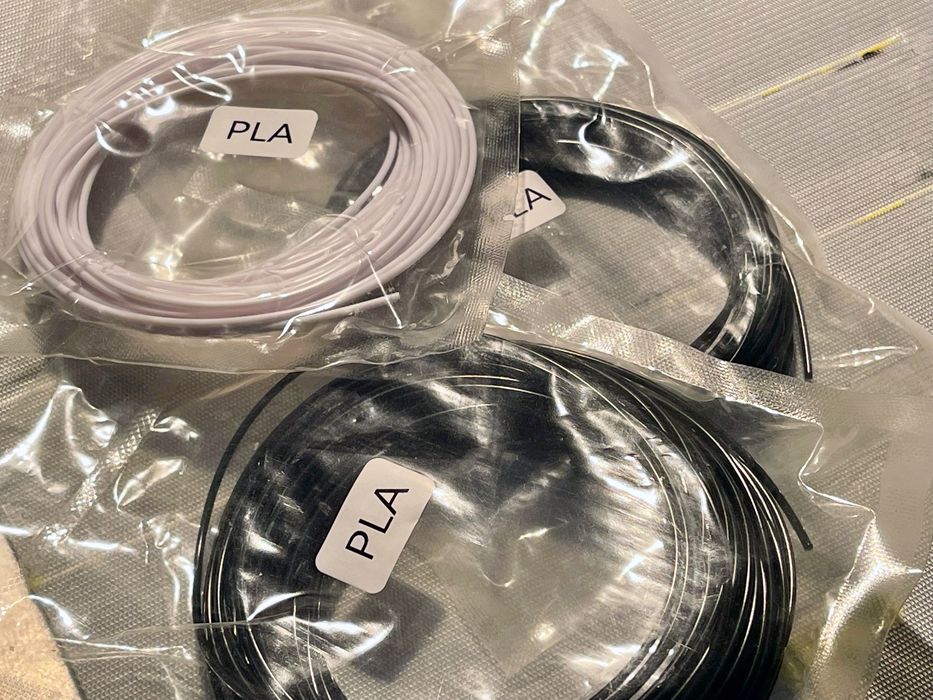
Virtually all desktop FFF 3D printers are accompanied by a spool or coil of filament. Inevitably it will be PLA because it’s a material that’s relatively easy to 3D print, and is not too expensive.
In fact, many machines will be designed to 3D print only PLA filament. One easy way to tell is whether the print surface is heated. If not, then it is typically practical to print PLA only, as other materials won’t stick properly. That’s ok for many 3D printer operators, who stick to PLA for every print.
Problems With PLA
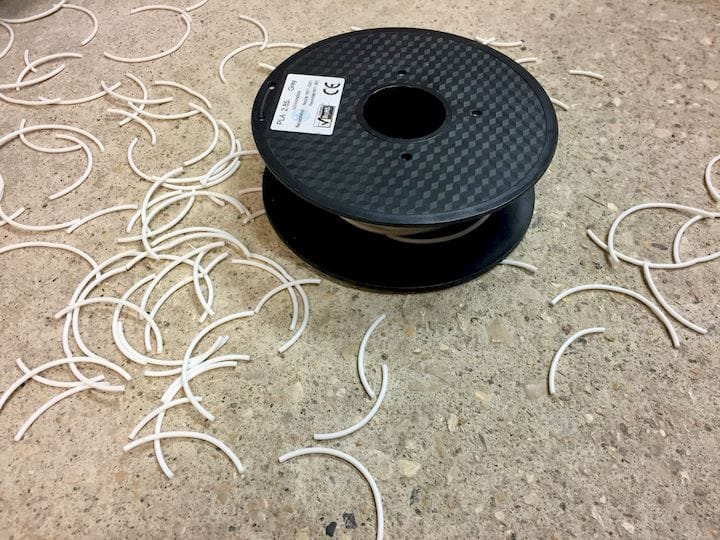
Alas, PLA is not the greatest material for some 3D printed applications. While PLA adheres well during printing and doesn’t warp very much, it has one fatal flaw: it has a relatively low glass transition temperature. This is the temperature where the material softens, and thus printed objects can lose structural integrity.
The classic case is a 3D printed phone holder placed inside a hot car on a summer day. The car interior can easily reach 60C, and that’s enough to slump the phone holder significantly. If your prints are going to be exposed to any temperature greater than 50C, you should consider alternative materials.
Print Profiles
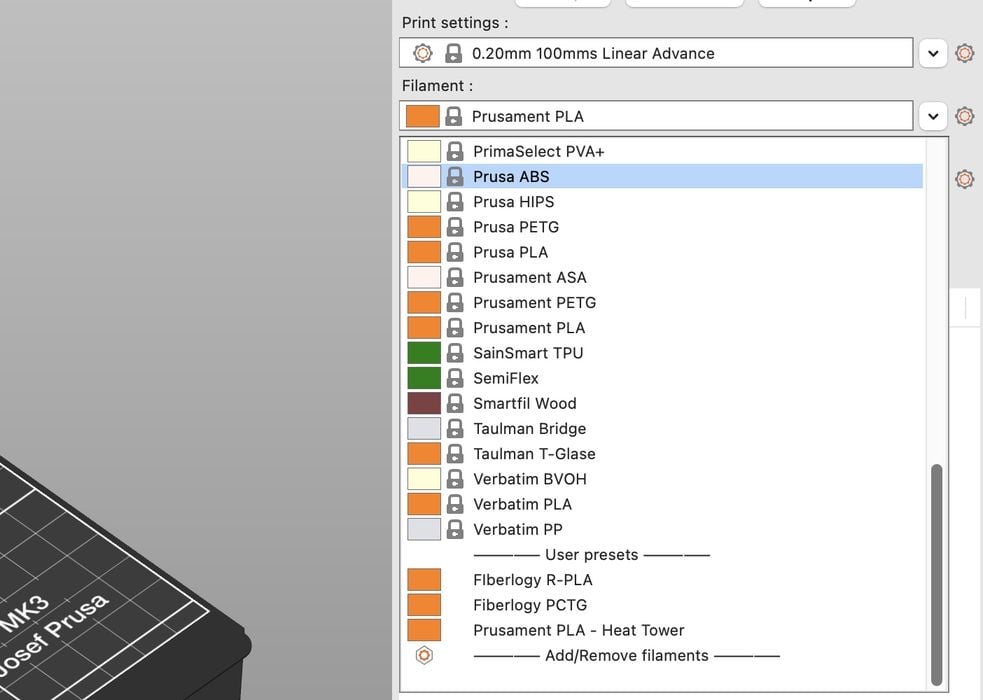
Switching to an alternative material can be easy or difficult. One way to make it easy is to use a pre-made print profile for the material in your favorite slicing program. Very often slicers come with profiles for a variety of commonly available brand name materials, so it’s easy to select one and go ahead.
However, be aware that not all materials are identical. While the label might say “PETG”, it could be have a slightly different chemistry than another brand’s PETG. Matching branded filament to a branded profile is the best course of action, but sometimes that’s not possible. If so, pick a “generic” profile or similar profile and be prepared to do some tweaking of the settings to get it to print optimally.
ABS or ASA?

The most often used alternative material is ABS, the same material used in LEGO blocks. It’s commonly available and is low cost. However, it’s normally challenging to 3D print. It requires a heated print surface to at least 100C, and an enclosure can greatly help defeat ABS’s pathological tendency to warp when printing.
The benefits of ABS are that it offers a higher thermal resistance, well past typical car temperatures, and also has a bit of give when under stress. It is far less brittle than PLA.
This makes it difficult to 3D print ABS on an open-gantry style device. However, some slicers allow the printing of a throwaway “shield” around the object to simulate an enclosure. Nevertheless, ABS is a bear to 3D print.
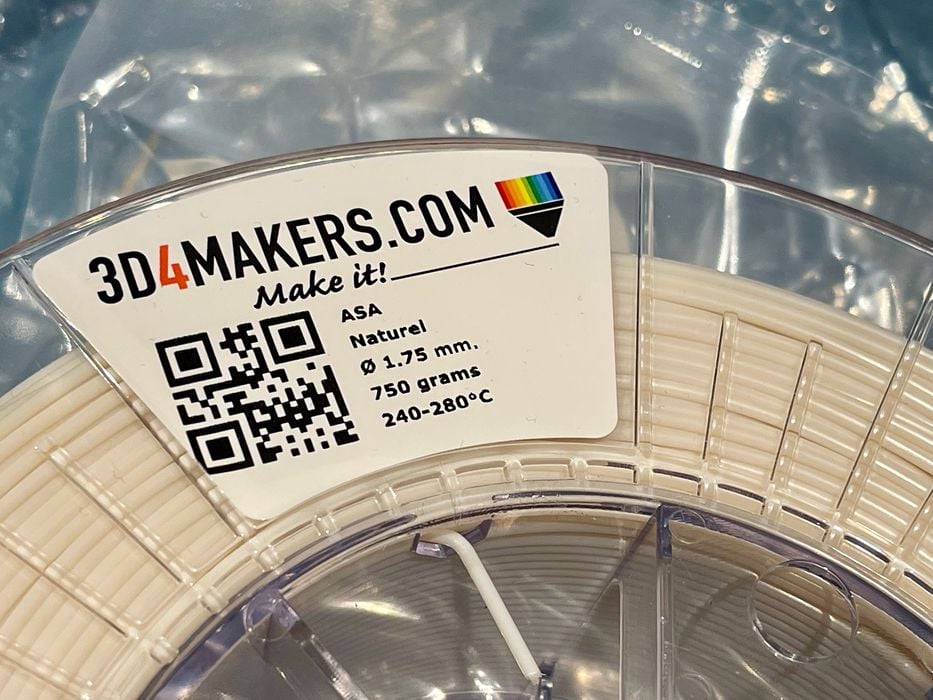
ASA is also often used, and it has properties near identical to ABS, except that it offers resistance to UV light. In other words, an ABS part will degrade if left outdoors, while an ASA part would not.
Easy Alternatives: PETG and PCTG
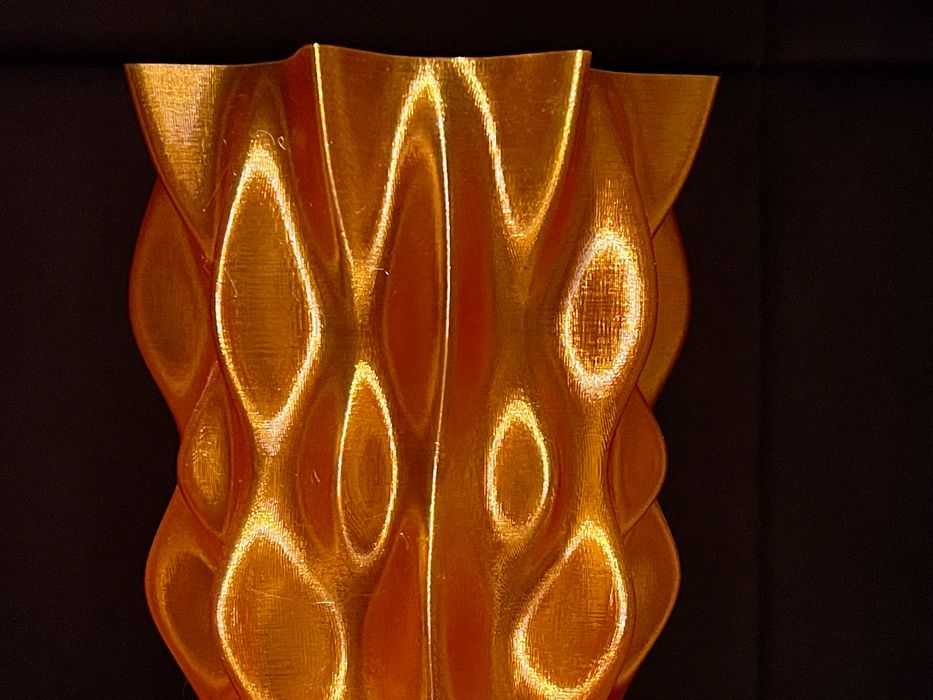
Two materials I’ve found to be quite useful as ABS alternatives are PETG and PCTG. PETG is more commonly available, and is as easy to 3D print as PLA, and perhaps even more. It typically has a shine on the surface that you don’t see with other materials.
PCTG is a more rare material, but is also very easy to 3D print. It provides strength and thermal resistance, but requires a hot print surface similar to ABS levels.
Nylons
Nylons, sometimes found as PA6, PA11 or PA12, are somewhat easy to 3D print and can be printed on most devices. They offer strong, end-use part level strength and considerable bending capability. They are terrific for printing parts with hinges or snaps.
But there are challenges. Nylons tend to warp a great deal and usually require extra attention to avoid print catastrophes.
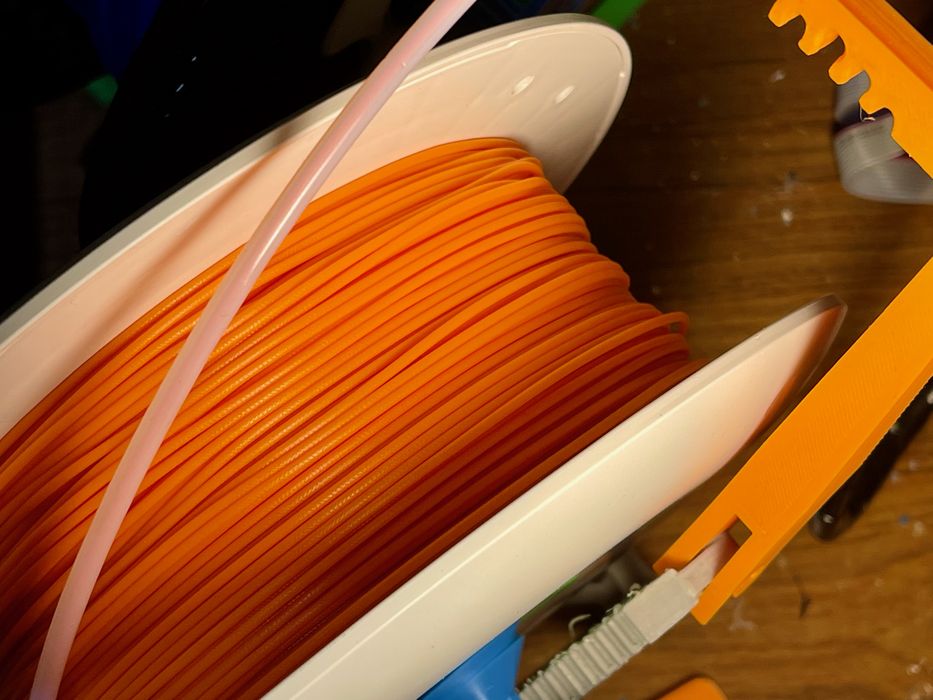
But the biggest problem with nylons is that they are extremely hygroscopic. In other words, if exposed to ambient air, they will slurp up moisture like a sponge. The moisture remains in the filament until it is printed, whereupon the H2O will boil and form bubbles in the print. This ruins part strength and visual appearance.
The only way around this is to use a filament dryer, preferably running while the print proceeds. This is an extra cost for a separate accessory, but is absolutely required.
Flexibles
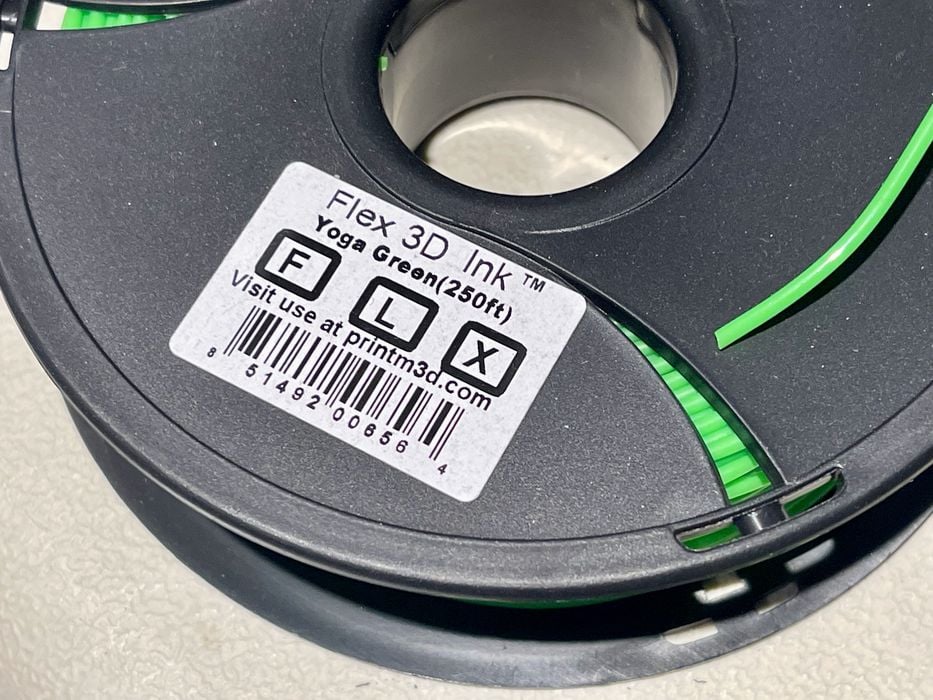
Flexible materials are fun to print as they can be used to make unusual parts, like gaskets, hinges, tires, etc. However, there is one important thing to know about flexibles: they are all very different.
There are different levels of hardness, sometimes denoted by the shore measurement scale (e.g. “40D” or similar). If you understand these measurements, then you can make an intelligent choice about a flexible filament purchase. However, some flexible filaments don’t even bother specifying their hardness so you have no idea what you are buying.
There are two terms used for denoting flexible filaments: TPE and TPU. TPU is actually a subset of the TPE category, and offers slight firmer materials. Regardless, you should choose based on the desired hardness.
One more thing: flexibles are usually very difficult to 3D print. They almost always cannot be used with a 3D printer equipped with a Bowden extruder, as the mechanism cannot push “wet spaghetti” through the filament tube.
Another issue with flexibles is that they stick too well to print surfaces. The frequently found twist-off magnetically attached print plate doesn’t work very well because the flexible print bends as you twist! It’s often best to put painter’s tape on the print bed before printing flexibles to avoid disaster.
Carbon Fiber and Composite Materials
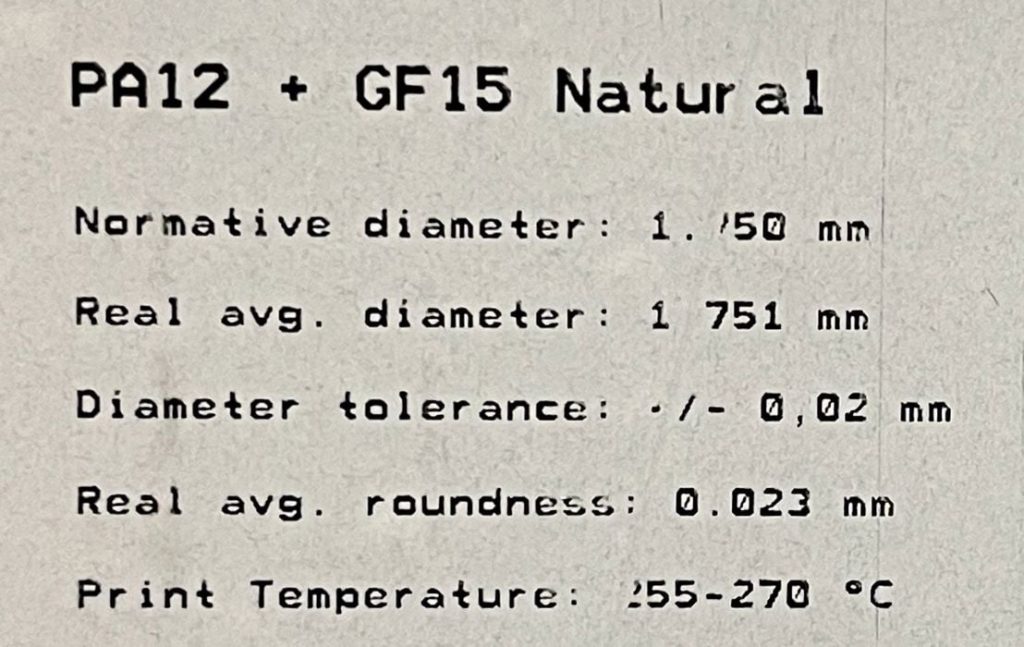
There are plenty of “carbon fiber” filaments on the market now, but do know that they are not literally carbon fiber. They are a polymer (PLA, PETG or similar) that is mixed with finely chopped carbon fiber. These materials can make your print quite a bit stronger than with just a polymer, but no where near as strong as when embedding continuous carbon fibers.
There are similar approaches for glass fibers and other composite materials. All tend to make the material stronger or adopt different properties.
A word of warning: some composites, particularly carbon fiber, will very quickly wear down your stock brass nozzle. The carbon fibers are actually harder than the metal so they grind off bits as extrusion occurs. Soon you’ll have a nozzle that is no longer 0.4mm in diameter, and require replacement. The solution is to swap out your brass nozzle for a hardened steel, titanium or ruby nozzle.
Higher Temperature Materials
There are higher temperature materials such as PEEK, PEKK, ULTEM, etc., but these are almost never 3D printed on desktop equipment. The reason is that they require extremely high chamber temperatures to avoid warping, sometimes in the 200C range, as well as a hot end that can hit 400C. This requires a specialized 3D printer designed for high temperature operation.
Note that most desktop 3D printers use a short tube of PFTE material leading into the hot end. This allows the filament to slide more easily. However, at temperatures exceeding 260C PTFE can begin to vaporize and produce noxious fumes that can harm birds and humans.
Material Changes
Finally, one more thing to know when using alternative materials: be conscious of the different temperatures used by the materials. A typical problem occurs when swapping from a higher temperature material to a lower temperature material. For example, switching from PETG (240C) to PLA (210C) is a 30 degree difference in temperature. The leftover PETG in the hot end might not properly soften at PLA temperatures, meaning it can glob up, jam, or otherwise pollute the next PLA print job because it will not properly be cleaned out. Always warm up the extruder to the temperature of the previous material to make sure it can be cleaned up in the initial fresh extrusions.