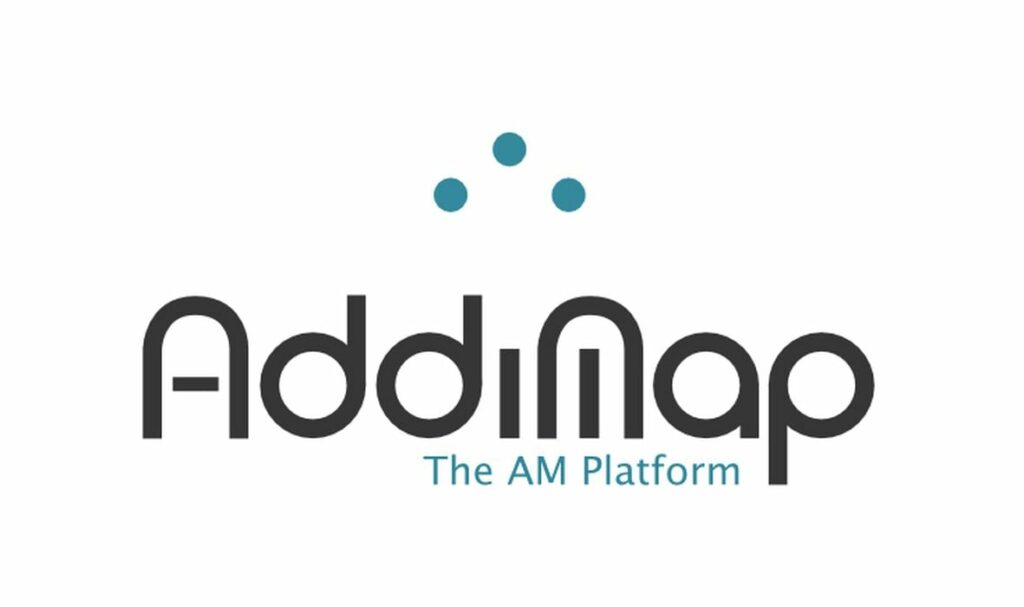
The AddiMap Project could revolutionize production metal 3D printing as we know it.
The project, undertaken by Roswag Engineering and NuCOS, intends on creating an online marketplace for trading LPBF printing parameter sets.
Roswag Engineering is a German end-to-end metal 3D print service, providing functions including engineering, simulation, materials, printing, post processing and analytics. NuCOS is a full stack software development company that is able to create applications that are user-centric for a variety of domains.
In their normal course of business, Roswag Engineering has to deal with plenty of different material and machine combinations. Their clients continually present different application requirements that involve unusual or standard materials, with varying engineering requirements.
Like most metal 3D print shops, Roswag Engineering has to go through the motions when presented with a new material and/or machine to print it on.
The “motions” are repeated iterations of test prints that gradually dial in the material / machine combination to enable production of metal parts that meet the engineering requirements of the applications.
This iteration is done by almost all metal AM shops, and is quite expensive. It’s expensive because pricey engineers must carefully design the parameter experiments, and the print jobs themselves occupy non-paying equipment time and consume amounts of very expensive metal powders that can cost US$100’s per kg.
It can take weeks of experiments to arrive at a suitable parameter set for a given material and machine.
These days it’s pretty much expected that this will occur whenever machines or materials change, and metal additive manufacturing providers no doubt account for this expense in their price quotes to requesters. In other words, it’s necessary work that adds to the final cost of metal parts.
Essentially, the printing engineers start with a nearly-blank slate when faced with this situation. They begin their iterations with stock parameters they get from the manufacturer or from their own experience, but that’s only the first step.
The work these folks do is literally repeated every day, everywhere by AM print shops. Over and over and over.
If only there were a way to short circuit this work because it’s repeated constantly.
Now there might be with The AddiMap Project. Roswag Engineering has created dozens of “correct” print profiles for more than 40 materials used in common LPBF 3D print systems that could potentially be reused by others with the same material / machine combinations. AddiMap explains their goal:
”The aim is to develop a digital B2B platform to provide all materials, parameters, data and services for the accelerated industrialization and democratization of metal 3D-printing.”
But how, exactly would this work? They explain:
“The first service of the AddiMap platform will be a marketplace for trading reliable process parameters and material data to reduce the inefficiencies in LPBF process parameter development projects. Instead of validating the quality and productivity of optimized parameter sets over several weeks with own test series and analyses, the results can be traded on the marketplace to use the full technological potential instantly.”
Using a pre-made profile from AddiMap, an AM workshop could clearly short circuit their tedious setup iterations. While the acquired pre-made profile might not be perfect for the application in question, it could be far closer to the target state than starting from scratch.
AddiMap suggests this approach could increase productivity by 80% for some situations by speeding up the job definition process.
Interestingly, there’s another benefit: research organizations or others that happen to be developing their own profiles for specific material / machine combinations can place their profiles on AddiMap for sale to others in the network. This provides them with another way to gain revenue from their printing experiments.
This is a tremendous development, and I think it’s far more important than you might initially believe.
Let’s take this concept out a bit further.
First, imagine if the AddiMap database of profiles was directly integrated into job preparation software. There are for metal 3D printing, not that many software tools used and it’s quite conceivable that an operator could simply pick a profile from a list while preparing the job directly. That would save quite a bit of time.
Now let’s imagine more. Suppose AddiMap also included polymer print profiles for other equipment and materials? Today we have some 3D printer manufacturers collecting their own print profile databases to make life simpler for their clients, but what if this was a more general solution? What if AddiMap integration was integrated into ALL 3D print slicing tools?
That could really change things in many positive ways.
Via AddiMap