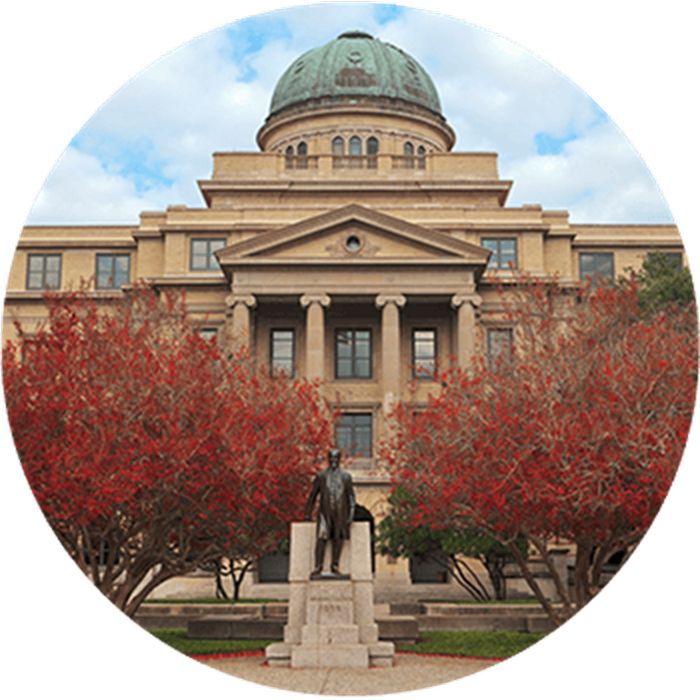
Charles R. Goulding and Preeti Sulibhavi look at the use of 3D printing by Texas A&M students.
Texas A&M University is a statewide network of 11 universities, seven state agencies, two service units, and a comprehensive health science center. Educating more than 152,000 students, the A&M System has a physical presence in 250 of the state’s 254 counties and programmatic presence in every county. Altogether, more than one in five students in a public university in Texas is enrolled in an A&M System institution.
Located in College Station, Texas A&M University is the flagship institution of the Texas A&M University System. It is the sixth-largest university in the country and home to more than 58,000 students. The university was named second in the nation by The Wall Street Journal among all universities, public and private, in a survey of top U.S. corporations, non-profits, and government agencies. The ranking was based on the number of graduates that recruiters preferred to hire.
With more and more businesses flocking to Texas, the university serves as a good resource for technical candidates.
Texas A&M and 3D Printing
The J. Mike Walker ’66 Department of Mechanical Engineering’s Rapid Prototyping Studio operates printers of two methods of additive manufacturing. The department possesses printers of the Fused Filament Fabrication (FFF) type and one of the Stereolithography (SLA) type. FFF printers utilize a “hot glue gun” extrusion style, heating a plastic filament and forcing it through an extruder mounted on a Cartesian robot, which directs where the filament is deposited. Stereolithography (SLA) is an additive manufacturing process that works by selectively exposing an ultraviolet (UV) laser on the surface of a vat of photopolymer resin.
3D printing has been available to students during Covid through Google Forms, to help limit the spread of COVID-19 from face-to-face interactions. Students receive an email when and how to pick their prints up.
In fact, during the coronavirus pandemic, the University’s engineers were creating much needed medical equipment and PPE to keep up with demand. Many lab technicians, engineers, innovators and makers across Texas A&M University were motivated to address the grave shortage of lifesaving medical supplies and devices during the COVID-19 pandemic by devising products to keep health care workers safe from infection.
Often using crowdsourced designs, 3D printers proved to be useful tools in this effort for both student hobbyists and the engineers and technicians who use them in labs across the College Station campus. It was a win-win for 3D printing as well as for the local healthcare community.
One of the PPE 3D printed at the University included clear, plastic face shields for healthcare workers to use in protecting themselves during contact with infected patients.
The Research & Development Tax Credit
The now permanent Research and Development (R&D) Tax Credit is available for companies developing new or improved products, processes and/or software.
3D printing can help boost a company’s R&D Tax Credits. Wages for technical employees creating, testing and revising 3D printed prototypes can be included as a percentage of eligible time spent for the R&D Tax Credit. Similarly, when used as a method of improving a process, time spent integrating 3D printing hardware and software counts as an eligible activity. Lastly, when used for modeling and preproduction, the costs of filaments consumed during the development process may also be recovered.
Whether it is used for creating and testing prototypes or for final production, 3D printing is a great indicator that R&D Credit eligible activities are taking place. Companies implementing this technology at any point should consider taking advantage of R&D Tax Credits.
“Gig ‘em, Aggieland”
There are many reasons why the Lonestar state is attracting big business. One of the best reasons is to recruit top talent at Texas A&M, with remarkable 3D printing expertise.