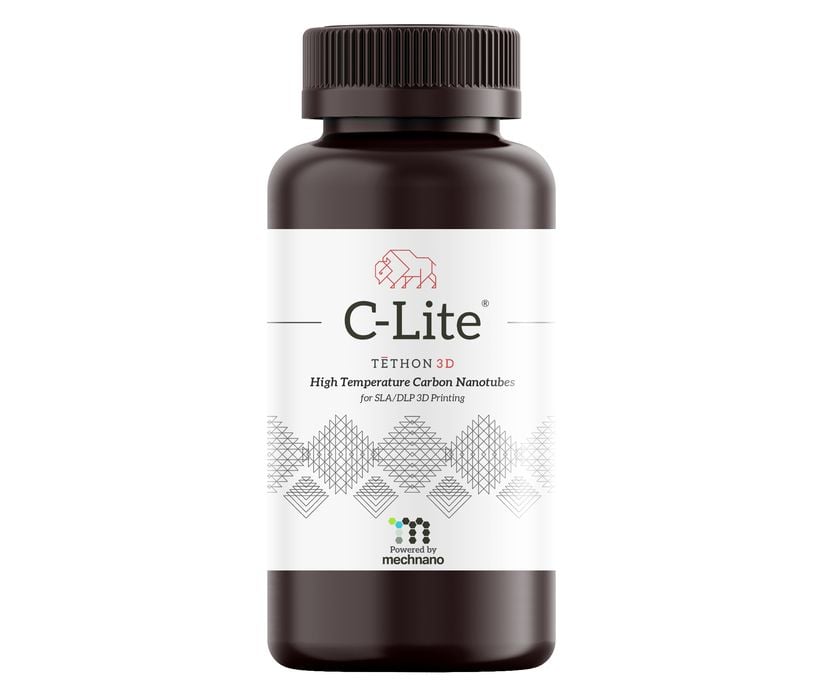
Tethon 3D has been producing unusual 3D printer resins for years, but their latest product, C-Lite is quite amazing.
First known for their ceramic resins, Tethon 3D has been slowly building quite a catalog of resin products, which are used by many in the industry. The company even launched their own desktop resin 3D printer, the Bison 1000 not too long ago.
Once again they push the envelope with C-Lite, their latest resin. This material has some highly unusual properties: it is an ESD (Electro Static Dissipative) material, AND it is a high temperature material, able to withstand heat up to a massive 225C.
The combination of these two properties should light up a number of new 3D print applications where both properties, ESD and high temperature, are required.
Apparently C-Lite took only six weeks to develop, which seems a bit fast given the unusual engineering properties. How did Tethon 3D manage to do this so quickly?
It turns out they partnered with Mechnano, an additive materials company I had not heard of previously.
Arizona-based Mechnano was founded several years ago with the goal of applying carbon nanotube technology to the AM industry.
Carbon nanotubes are microscopic arrangements of carbon atoms in the form of tubes. These tubes are unbelievably strong, because their structure is literally based on the atomic forces binding carbon atoms together.
Carbon nanotubes offer ridiculously powerful engineering properties. According to Mechnano:
- 100× higher tensile strength (no fatigue failures) than steel
- 100× higher thermal conductivity than steel
- 6× lighter than steel
- 5× higher modulus than steel
- 5× electrical conductivity than copper
- 15× thermal conductivity than copper
- 1000× current capacity than copper
That sounds good. Why don’t we just mix some carbon nanotubes into 3D printer materials to make them a lot stronger, much like what has been done with carbon fiber?
It turns out you can’t do this. Microscopically, carbon nanotubes very quickly bunch up into tangled messes, which lose the desired properties. Even if you could untangle them to mix with a binder, they’d re-tangle quickly.
That’s the problem Mechnano set out to solve, and after 100+ patents, they apparently have done so. They are able to mix carbon nanotubes successfully into 3D printing materials to provide additional strength and other properties.
In fact, they were apparently the very first company to develop successful carbon nanotube composite resins for vat polymerization systems.
Back to Tethon 3D.
Tethon 3D is well-known for their ability to produce powerful 3D printing resins, and they currently offer around twenty very unusual resins. One of their products is a kind of “development kit”, where it’s possible to mix in different additives to create new resin types.
This is where they partnered with Mechnano. Mechnano provided Tethon 3D with their E35A masterbatch, a mix-in that is able to provide ESD properties. By combining this with a base high-temperature resin, they were able to create C-Lite, a resin with both properties.
Mechnano CEO Steve Lowder said:
“This is a great example of how our discrete carbon nanotube technology is a game changer for the additive manufacturing industry. E35A Masterbatch provides ESD benefits to existing materials, such as the custom high-temp resin formulated by Tethon 3D.”
There’s some interesting thoughts from this partnership.
First, this shows that very powerful products can be created by combining the knowledge of two companies together. The years of work each company undertook to get to this point was leveraged to achieve something even greater. I wish more 3D print companies would look at partnerships of this type, as that would benefit not only the participating companies, but also the 3D print community as a whole.
Secondly, C-Lite makes Tethon 3D’s resin catalog that much stronger. It’s critically important to have more selection of unusual materials because that’s the only way some applications will come to use 3D printing technology.
I believe Tethon 3D realizes this, as their CEO, Trent Allen, told us:
“We have four core strategies for the long term and the top of the list is developing as many materials as possible.”
Mark one more done.