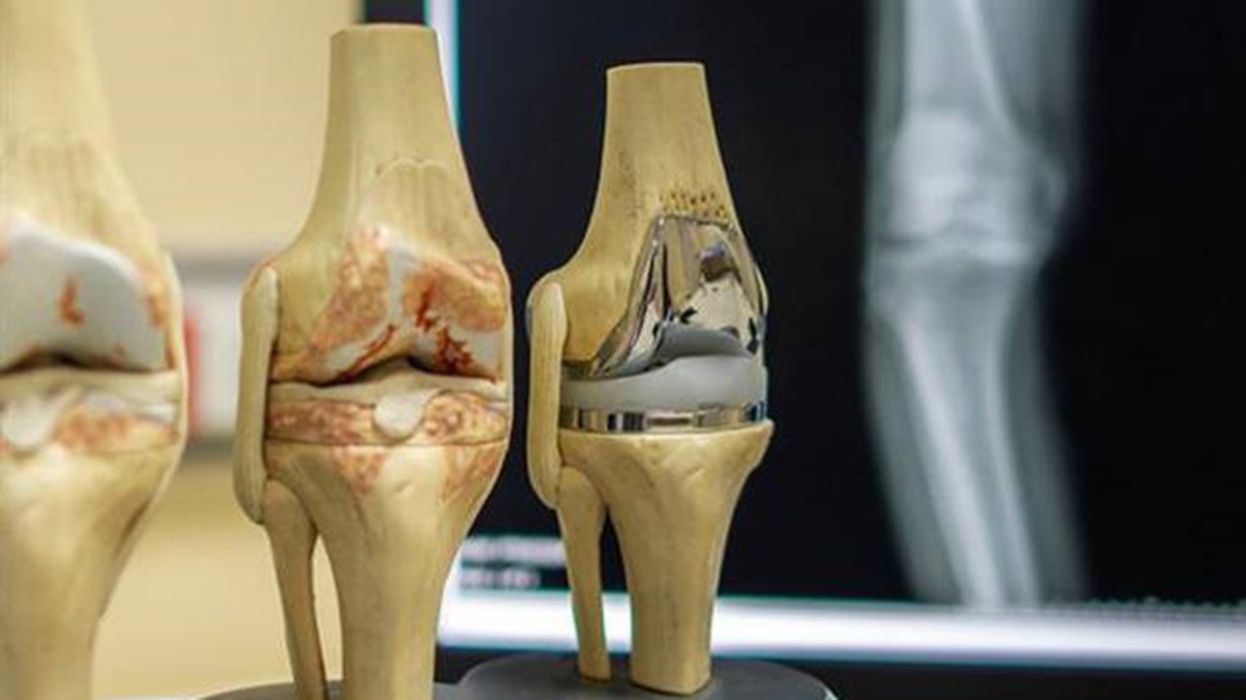
Charles R. Goulding and Preeti Sulibhavi look at opportunities for 3D printing technology in healthcare.
Due to the recent triple threat identified by many state and local governments and recognized by the Centers for Disease Control (CDC) and the Department of Health and Human Services (HHS), that being Covid-19, the flu and respiratory syncytial virus (RSV), elective surgeries are once again being delayed.
Non-essential procedures, such as typical outpatient procedures, including cataract operations, removal of kidney stones, tonsillectomies, and hernia repair, are being pushed back due to both hospital capacity and fear of catching either or all the three viruses mentioned.
The medical community continues to improve the use of 3D printing during the elective surgery moratorium.
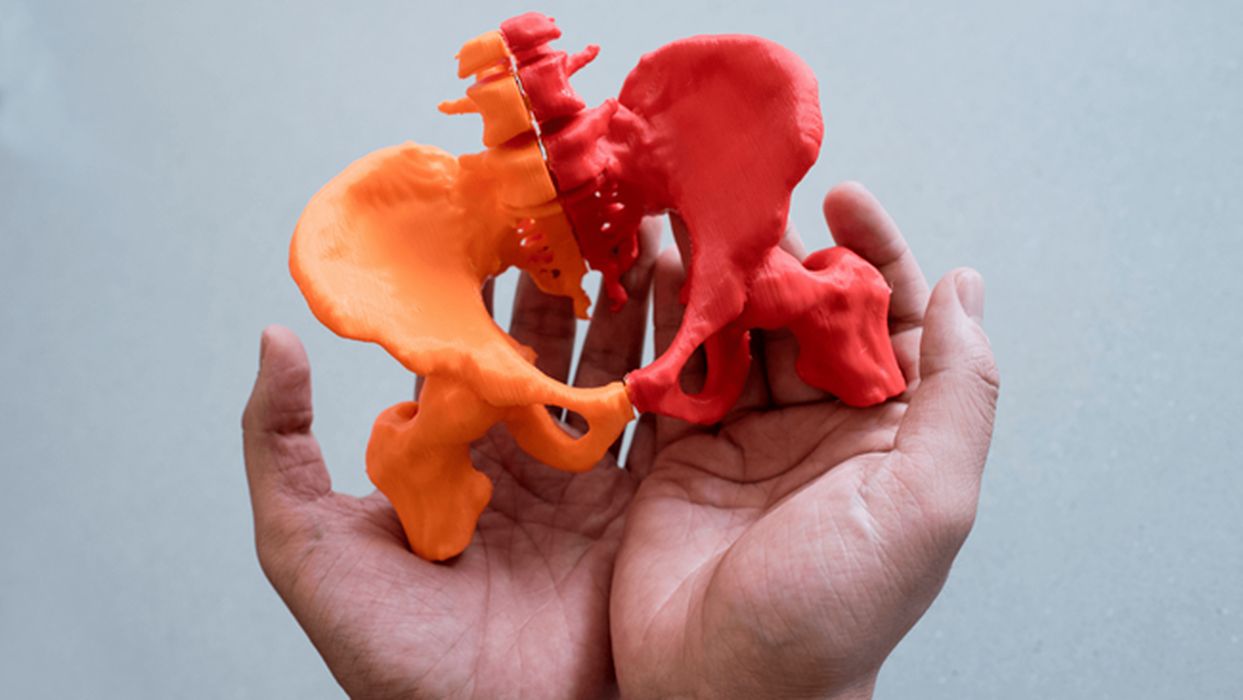
For example, sufferers of osteoarthritis often elect for knee replacement surgery, which is usually a last resort for many patients. There is a personalized early knee osteoarthritis treatment, developed by engineers at the University of Bath’s Center for Therapeutic Innovation (CTI) working with 3D Metal Printing Ltd, which uses state-of-the-art 3D metal printing technology to make personalized medical-grade titanium-alloy plates that perfectly fit every patient.
The TOKA (Tailored Osteotomy for Knee Alignment) treatment improves the operative procedure and fit of high-tibial osteotomy (HTO) plates that are used in realigning a patient’s knee, making them more stable, comfortable and better able to bear weight than existing generic plates. The technique also simplifies HTO surgery, thereby expediting them and making them safer.
Trials for this procedure will begin once clinical centers reopen for elective surgery.
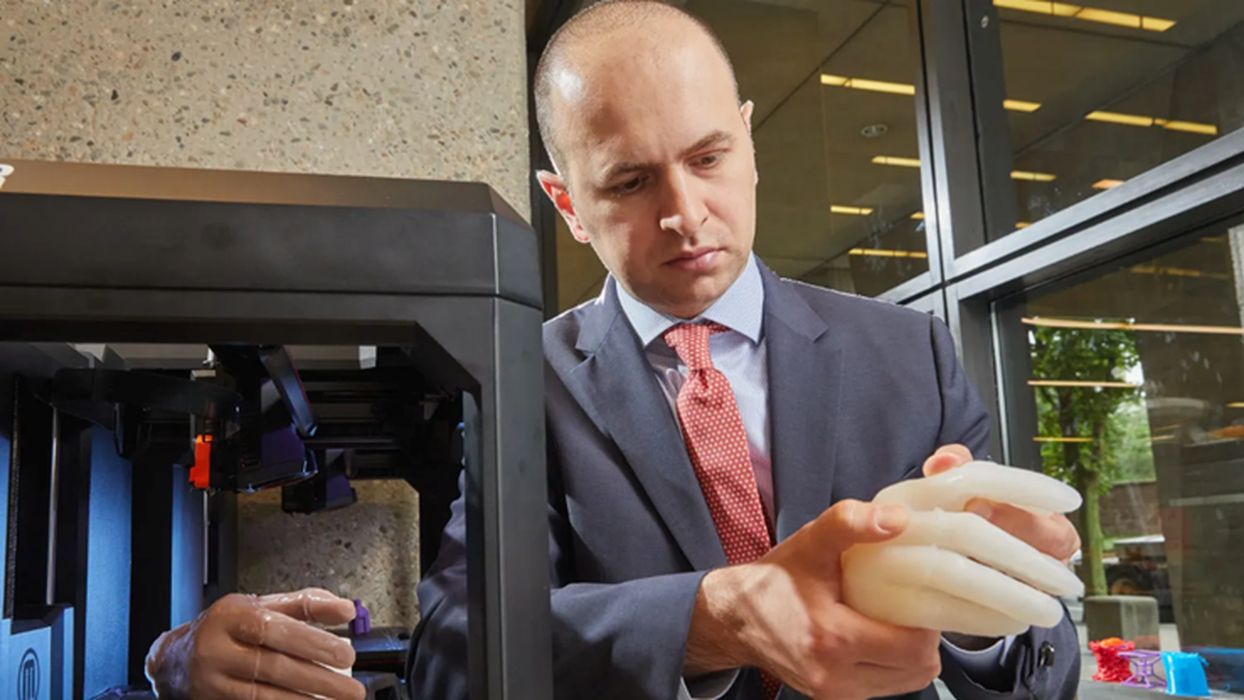
In addition, the University of California at San Francisco (UCSF) is offering an elective for students to the basics of 3D printing and the workflow generating a 3D-printed anatomical model from a CT scan. Derek Harmon, MS, PhD is the course faculty and lead, and Makers Lab staff provides the 3D printing technology and in-class training and support.
The Yale School of Medicine is utilizing 3D printers to create exact replicas of patient limbs and anatomical parts to better plan surgeries as well.
Highly reputable institutions such as Johns Hopkins and Boston Scientific have been utilizing 3D printing technology with some high-quality results. Boston Scientific produces a large range of medical devices used to diagnose and treat patients with issues in the areas of cardiology, urology, endoscopy and many more. Boston Scientific, in collaboration with Stratasys, hosts “Boston Scientific Additive Manufacturing Customer Success Day.” This is a half-day training to identify and build AM tooling, manufacturing aids and production parts to improve efficiency and reduce costs on your manufacturing floor.
The Research & Development Tax Credit
The now permanent Research and Development (R&D) Tax Credit is available for companies developing new or improved products, processes and/or software.
3D printing can help boost a company’s R&D Tax Credits. Wages for technical employees creating, testing and revising 3D printed prototypes can be included as a percentage of eligible time spent for the R&D Tax Credit. Similarly, when used as a method of improving a process, time spent integrating 3D printing hardware and software counts as an eligible activity. Lastly, when used for modeling and preproduction, the costs of filaments consumed during the development process may also be recovered.
Whether it is used for creating and testing prototypes or for final production, 3D printing is a great indicator that R&D Credit eligible activities are taking place. Companies implementing this technology at any point should consider taking advantage of R&D Tax Credits.
Conclusion
The triple threat this winter should not be taken lightly. There are many reasons why patients have been choosing to delay their elective surgeries, however, the medical and 3D printing communities can use this period to improve future patient outcomes.