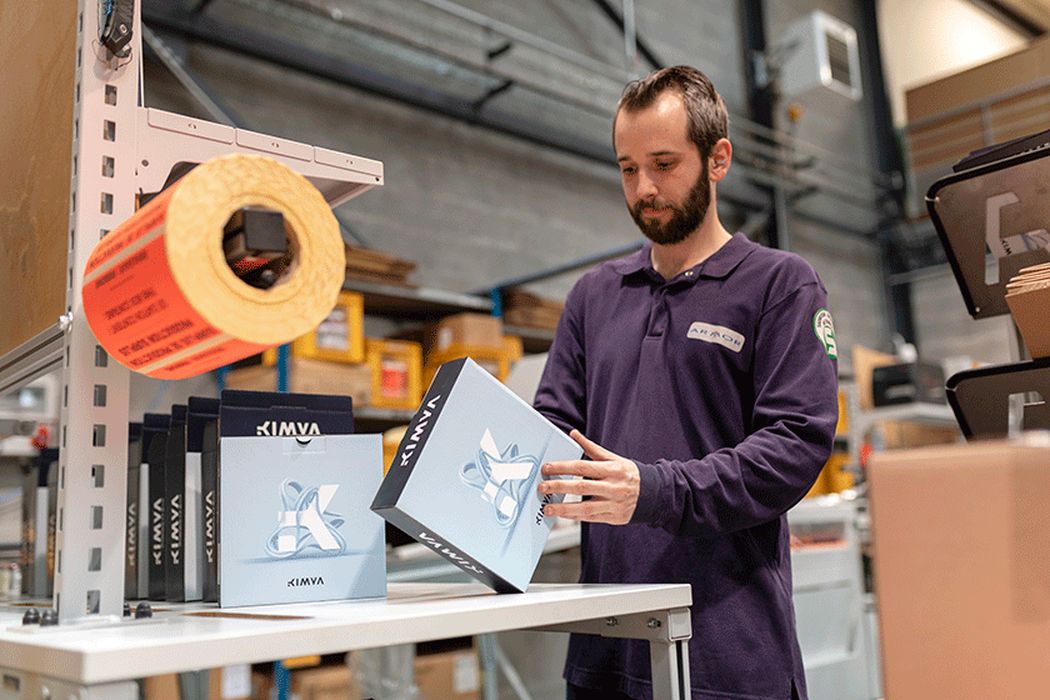
Two reports on sustainability were issued this week by additive manufacturing organizations.
The first report was from the Dansk AM Hub, an organization dedicated to promoting the use of additive manufacturing in Denmark. The provide a “hub” where interested parties can exchange information and learn more about the technology.
Denmark is well-known for their advanced efforts to reduce CO2 emissions and generally increase sustainability. They propose that in order to meet the emissions targets, a reduction must take place in key sources of emissions related to the production and use of aluminum, cement, steel and plastic.
They propose four key steps, which indeed should be considered by anyone in the AM space regardless of location.
The first step is “Digitization”, or as we like to call it, “Digital Inventory”. This is the concept that instead of blindly making billions of parts in hopes they will be sold and used as spares in the distant future, print on demand. Move the “inventory” to a digital format where a 3D printer could produce them as required.
“Mind the Materials” is the second recommendation. Here they suggest to prioritize the use of recyclable and recycled materials. In general, recycled materials generate far less CO2 than the production of raw, first-use materials. This is a trend I’ve seen increasing in recent years.
“Rethink Design” suggests adapting designs so that systems can be repaired or maintained for longer lifecycles. The idea is to reduce the need for the production of new parts and systems by making them last longer. This could be considered the opposite of the “use and dispose” culture we’ve all been subject to for many years.
Finally, they offer “Own your own value chain”. This proposes that companies producing systems document, monitor and improve their entire production lifecycle. For example, it’s not sufficient to just say that recycled materials were used, when the parts and materials were shipped across the ocean four times in CO2-emitting ships. The entire chain of events and activities from raw material to manufacturing to sales to usage to disposal must be considered.
I’ve seen evidence that some of these concepts are starting to be used in some 3D print companies, both suppliers and operators. However, there are many more participants required to make a significant difference.
Kimya Report
The second sustainability report was from Kimya, a well-known producer of 3D print materials.
The company published the results from a lifecycle analysis for their 3D printer filament production process. This is precisely what Dansk AM Hub has recommended above.
Kimya’s analysis shows use of their recycled PETG material provides 35% less emissions as compared to their functionally equivalent non-recycled PETG materials.
Kimya explains:
“Life Cycle Analysis (LCA) is a multi-stage, multi-criteria analysis that measures the environmental impacts generated by a product or service throughout its life cycle: from the extraction of raw materials to the end of life, including manufacturing and use. Conducted in collaboration with Greenly and based on ADEME guidelines, the LCA of Kimya’s recycled PETG 3D filament shows an emission of 4.08 kgCO2 versus 6.27 kgCO2 for Kimya standard PETG filament. Using recycled filament helps to reduce emissions by 35% when compared with the standard version.”
3D printer operators then face a choice: use recycled or fresh PETG?
Shouldn’t the choice be obvious?
Via Dansk AM Hub and Kimya