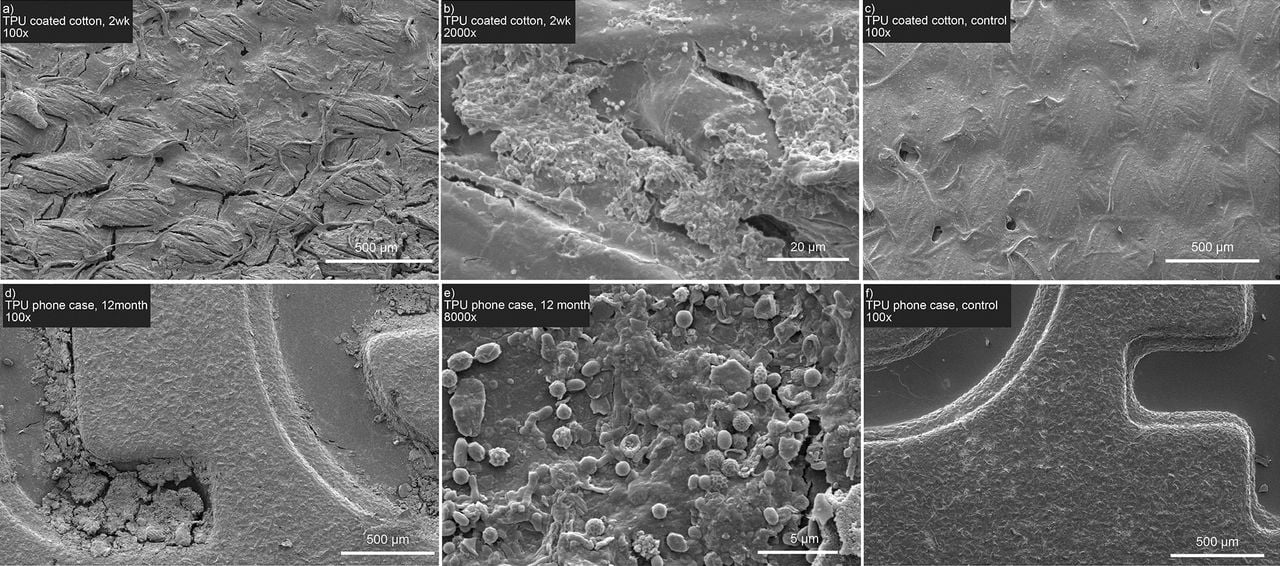
A study proves certain bio-based polymers can complete degrade in the natural environment.
Natural degradation of polymers is not common, as most polymers are derived from petroleum, which doesn’t integrate with the natural surface environment of the planet. In other words, items made from most plastics persist when discarded.
That persistence is at a microscopic level, however, as discarded plastic parts can mechanically break down into ever-smaller particles. They ultimately end up as microplastics, which are extremely tiny particles of — intact — polymers. These are so tiny they can (and are) blown by the wind and moved by the sea to infest basically every environment on the Earth. That’s not good, as we don’t yet know what the long term chemical implications of this will be.
Because of all this researchers have been working diligently to develop new, fully degradable materials for industry.
Most current plastics are not biodegradable. PLA, the most common 3D printing material, is made from organic sources and is fully recyclable. But it is most definitely not naturally biodegradable. If you were to bury a PLA part, it’s going to stay there unchanged for many years.
PLA can be broken down chemically, but only with an application of high heat and pressure. This doesn’t happen in today’s landfills, so discarded PLA 3D prints will inevitably become microplastics.
One theory is that materials derived from bio sources could be made to be fully biodegradable. That is, the part could be completely broken down chemically without the requirement for any special action. Leave it outside, and it disappears.
How does this biodegrading process work? The researchers explain:
”Biodegradation is the process by which microbes break down polymers into simpler molecules that can be used as a source of carbon to produce biomass. This requires that the polymer contains chemical bonds, most notably in the polymer’s primary backbone structure, that are physically accessible to enzymes that naturally recognize these bonds as substrates, and that the underlying monomer molecules that are released through this enzymatic cleavage can be consumed by microorganisms. In natural environments, this process is typically performed by consortia of microbes, including bacteria and fungi, secreting hydrolytic enzymes, which sever the polymer to release a variety of monomers and oligomers that can then be utilized as a carbon nutrient source by the microbes.”
Their research investigated TPU-FC1, a bio-based polyurethane material. They sought to determine the precise method of degradation, and used a variety of investigative tools to do so.
They produced samples of parts using this material, including an injection molded part and a cloth, and used them for the study. They didn’t 3D print a part for testing, but one can envision the injection molded part test as a substitute.
Their experiment was to shred the TPU-FC1 samples into tiny particles to simulate microplastics using a stock benchtop sander — with 80 grit sandpaper.
These particles were then exposed to highly controlled environmental scenarios, including a 45C composting situation.
They found that after 200 days the TPU-FC1 particles had been completed degraded and no material remained.
Their approach was highly detailed and carefully executed, clearly showing that the biodegrading process was indeed real and measurable. This proof provides a foundation for the use of true biodegradable plastics.
Research of this type will hopefully lead towards a 3D print world where biodegradable materials are used much more frequently. Today almost all common 3D print materials are not biodegradable.
A practice that I’m hoping will emerge would be the use of biodegradable materials for 3D printing prototypes. As iterations proceed, the discarded prototypes would be biodegradable. But when the final design is reached, then the material could be switched out for the production material. That approach might save a considerable amount of microplastic sources from the typical 3D printing workflow.
Via Nature