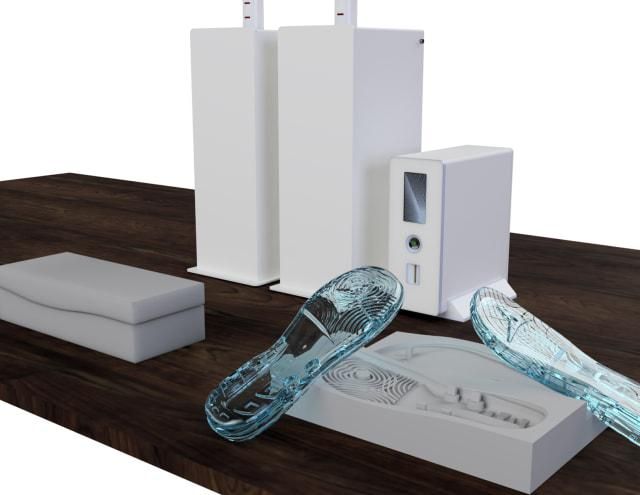
3D printing company introduces the Inj3ctor to allow everyone access to injection molding of rubber parts.
If you ever wanted a factory in your home, you are in luck. Structur3d has unveiled the Inj3ctor platform, a low-cost desktop injection molding tool that uses 3D-printed molds. Andrew Finkle, co-founder and CTO of Structur3d, discussed the Inj3ctor’s launch with engineering.com.
Founded in 2013 in Kitchener, Ontario, Structur3d began with the Discov3ry Paste Extruder, which was funded through Kickstarter in 2015. It featured an add-on for desktop fused deposition modeling (FDM) printers that allowed much greater flexibility in the choice of materials, aside from just plastics.
“The Discov3ry is compatible with most open additive manufacturing platforms,” Finkle said. “It gave 3D hobbyists the option of using thousands more materials with their plastic 3D printer thanks to this upgrade. We currently have thousands of hackers, scientists, engineers and educators using the Discov3ry technology in their workflow.”
Through customer feedback and collaboration with Ultimaker, the company expanded its offerings to include pre-integrated printer systems, the Discov3ry Complete and Discov3ry 2-Part Complete.
The Canada-based organization now aims to overcome challenges preventing 3D-printed rubber parts from meeting necessary manufacturing standards, by bringing 3D printing and desktop injection techniques together with factory-grade materials.
Existing Technologies and Materials
Most 3D-printing applications call for rigid materials. Typically hard and brittle thermoplastic materials, such as polylactic acid (PLA) and acrylonitrile butadiene styrene (ABS), offer very limited applications. Sometimes, more flexibility and strength are required.
Elastomers, which are rubber-like materials, try to fulfill that requirement. However, the flexibility comes with drawbacks. FDM 3D printers, the most popular type, extrude heated filament so that it can melt and be brought into the requisite shape. This does not work with elastomers, as the print head would be blocked. Additionally, elastomers cannot be used in functional parts due to their fragile nature.
Other leading rubber parts production processes are casting and traditional injection molding. Casting involves premixing precursor materials and pouring or dipping into the desired shape. Though it is a reliable process, it results in a lot of wastage of time and materials.
As for traditional injection molding, the mold has to be tailored to one specific part, making it very expensive. This makes it feasible for the production of thousands of units but not suited for rapid prototyping of that same part during pre-production design.
While the original Discov3ry extruder was able to address some of these issues, there remained a larger problem. The structural integrity of extruded parts along the Z-axis (i.e., the height) was weaker than that along the X- and Y-axes.
“Due to viscosity and the slower ‘hardening’ times compared to plastic, silicone parts are limited in the surface quality that can be achieved through direct writing of the material, even seeing some slumping,” Finkle explained. “Direct writing of silicone can lead to slow print times—about five times slower than plastic—and reduced surface finish quality.”
Therefore, the demand for rapid prototyping of manufacturing factory-grade rubber products remained unfulfilled. Structur3d stepped in to fill that gap.
Read more at ENGINEERING.com