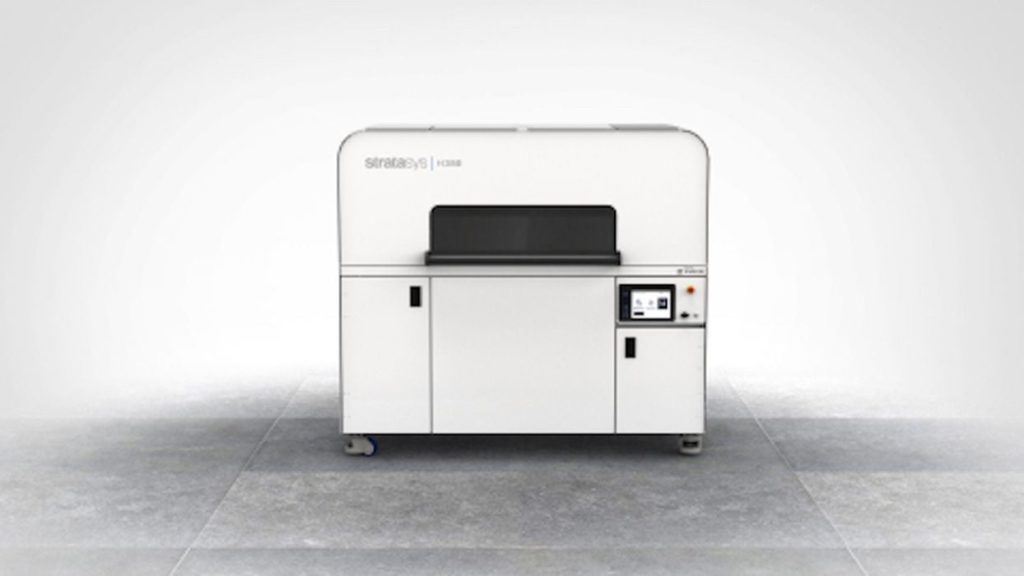
Stratasys announced new software tools to enable more use of their SAF technology in manufacturing.
SAF 3D Printing
SAF stands for “Selective Absorption Fusion”, and it’s a very different 3D printing process. While it uses a flat powder bed as many other 3D printing processes, do, the method of fusing the particles together is quite different.
In SAF a fast-moving arm quickly deposits droplets of “HAF” on the portions of the layer that are to be fused. HAF is a specialized fluid designed to rapidly heat up when exposed to specific light frequencies.
After the fluid deposition, a powerful infrared light sweeps over the layer, causing the wet portions to heat up and fuse. While the other powder is also heated, it’s not sufficient to cause fusion to occur, and these particles remain loose.
The process repeats, layer-by-layer until the object is complete, whereupon it must be dug out of a build chamber filled with loose powder.
SAF has not only the major advantage of powder printing, the lack of requirement for any support structures, but it’s also very fast as each layer can be produced quite quickly with the rapid deposition and heating steps.
Stratasys has implemented SAF in one device thus far, the H350 3D printer.
GrabCAD and SAF
Now Stratasys announced they’ve integrated H350 — and by extension SAF — into GrabCAD, their go-to 3D print management software tool.
Specifically, they have announced “GrabCAD Print” for the H350, and they say it is built on their recently introduced GrabCAD Additive Manufacturing Platform.
If you’re not familiar with GrabCAD Additive Manufacturing, we recently explored this new software. It’s far, far more than just a 3D print slicer, as it includes CAD-agnostic end-to-end DfAM workflows, network printer management, fleet management, job scheduling, Industry 4.0 integration, and much more. Basically it’s an all-in-one tool for managing a design and manufacturing line for AM products.
Now it’s also available for the H350.
Stratasys explains:
“GrabCAD Print for the H350 ensures that the end-to-end workflow from digital design to physical part across the manufacturing enterprise is easy, accessible, affordable and connected. The software has been upgraded to provide advanced print capabilities that give users the ability to stack and nest parts automatically or manually to maximize packing density and print hundreds to thousands of parts in a single build volume. Further, because the application is built on the GrabCAD Additive Manufacturing Platform, Stratasys H350 users have access to additional core applications like GrabCAD Print Mobile, GrabCAD Shop™, reporting and analytics, and machine connectivity which will allow them to easily integrate their H350 with enterprise systems and Software Partner solutions.”
This is a key step for Stratasys as it now positions their H350 — and by implication SAF itself — as a fully capable production option. Manufacturers considering SAF may now be assured they will have the necessary software to operate the device, in addition to the hardware and materials.
There’s another thing: SAF is a very interesting technology that can be scaled up significantly. By increasing the powder bed surface area (and/or depth), the print volume can be dramatically increased. Making bigger deposition arms should not be a technical issue, nor should illuminating a larger area with infrared light.
In other words, if Stratasys wanted to, they could make a much, much larger SAF device. I’ve been thinking all along that the H350 is basically an experimental platform for Stratasys to figure out all the details of using SAF for production purposes, and that seems to be the case with today’s announcement.
Imagine if such a machine existed: a manufacturer could deploy massive 3D print jobs that would be able to produce perhaps thousands of parts in a single job. By stacking parts together vertically in the build chamber, this should be entirely possible. Even better, the manufacturer could specify customizations for each and every part produced, providing huge flexibility. In a sense, this could be a kind of “universal manufacturing machine”.
That could be where Stratasys is headed, and the new GrabCAD could certainly be a big step along that trajectory.
Via Stratasys