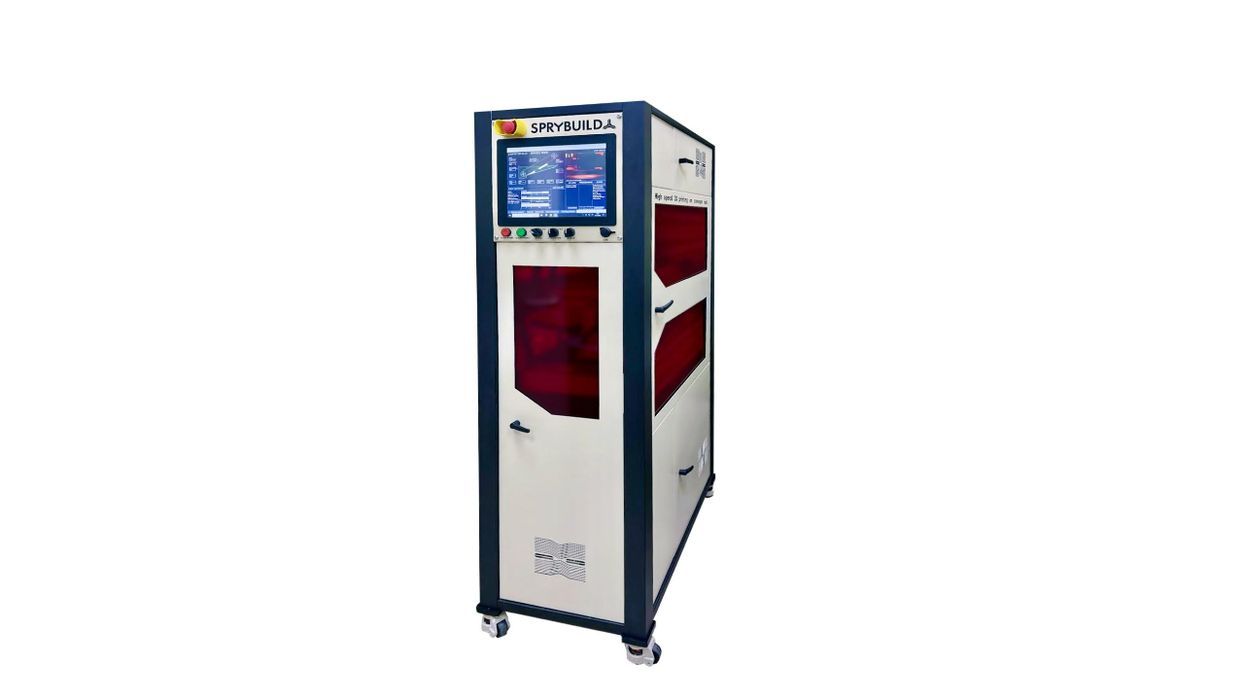
A new player has entered the resin 3D print space: Sprybuild.
The Israeli company has evidently been designing their new system in stealth mode, but this week they revealed their unusual technology.
There are many questions, but we do know the basics of their unusual 3D printing process. It seems the machine designers sought to develop a continuously-operating resin 3D printer, something that really hasn’t been done by anyone else.
They have apparently succeeded.
How could this work? The machine design includes a sophisticated conveyor belt system instead of the standard static build plate. Once the print is complete, the conveyor moves the printed area up out of the resin vat. It then turns a sharp corner, which peels the prints off the belt. Completed items drop into a bin for later pickup and processing.
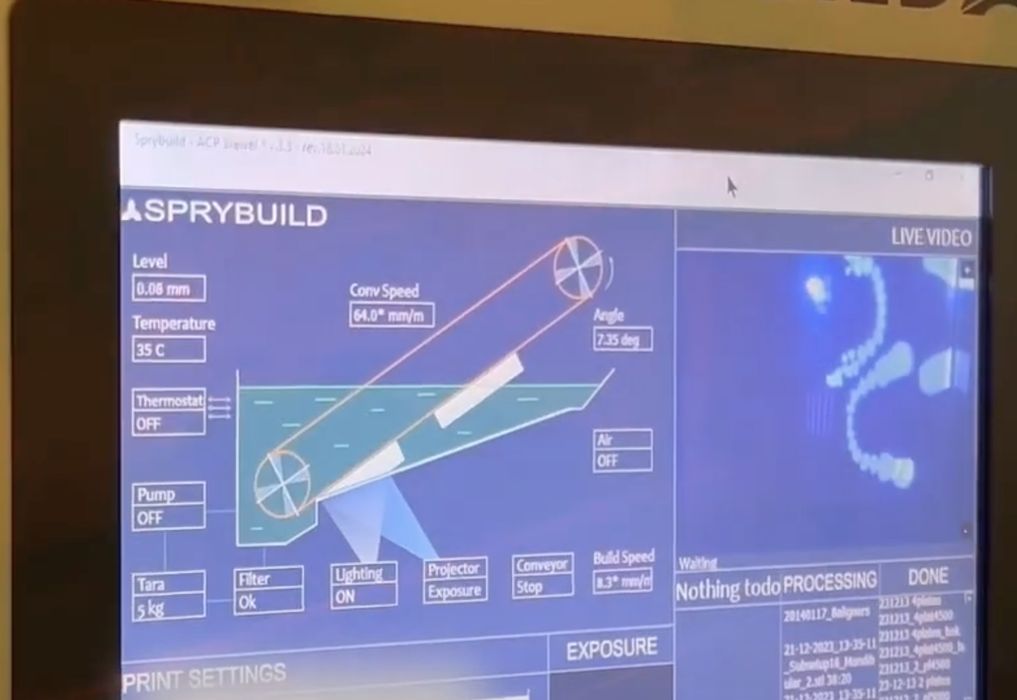
This image shows the concept, where the printing happens under the surface of the resin. Note that the printing takes place at a slight angle from the build surface, unlike most resin 3D printers.
The belt is made of strong, but flexible metal and has a magnetic system to hold it flat. This is always my first question about belt systems: when used over and over, belts tend to bubble and warp, causing quality issues. Sprybuild seems to have found a way around that issue, and they’ve patented it.
That’s not the only interesting feature. The system also uses a form of polymerization suppression. This is done at the tank / resin interface, where in typical resin 3D printers new layers stick hard to the tank. That requires lengthy peeling processes to release the print. However, because of the suppression system on the Sprybuild, no peeling is required and prints can keep going at maximum speed.

Sprybuild said the printer can theoretically print up to 150mm of height per minute on certain materials. This is said to be 20X the speed of the average resin 3D printer.
This appears to be quite similar to Carbon’s CLIP process, but Sprybuild said this:
“Sprybuild’s technology implements a solid optical interface, enabling a continuous build process similar to, yet distinct from, the CLIP technology developed by Carbon3D. The challenge here was twofold: to eliminate the need for inhibiting resin near the interface and, at the same time, to create “dead zones” where the resin could remain liquid. These zones are crucial for ensuring a steady flow of resin into the printing area, a key factor in achieving high-speed printing. Sprybuild’s ingenuity led to the development of an interface that meets these requirements, ensuring sufficient resin flow and curing only where necessary.”
Note that there are multiple processes now on the market that can achieve speeds similar to Carbon’s, and Sprybuild is another one to add to the list.
These features combine to form a very powerful option for resin print manufacturing. A printer that can produce objects quickly — and without requiring much operator labor — is highly desirable.
They don’t say but presumably the system accommodates a large quantity of resin to allow for lengthy unattended operations.

The conveyor process seems quite functional, but it’s likely that certain complex geometries might not survive the detaching step. I can imagine difficulties with spindly models with lots of protrusions. These could break or get tanglled up when detaching. However, there are plenty of 3D models that would work just fine on this setup.
Sprybuild seems to be focusing on the dental market, which is both large and profitable. One can easily foresee squads of these machines being used as a production factory in a dental lab.
There’s no word on full specifications, material compatibility, machine release dates or system cost. I’m sure that’s all coming, and I’ll be watching carefully to see where they position this system.
Via Sprybuild