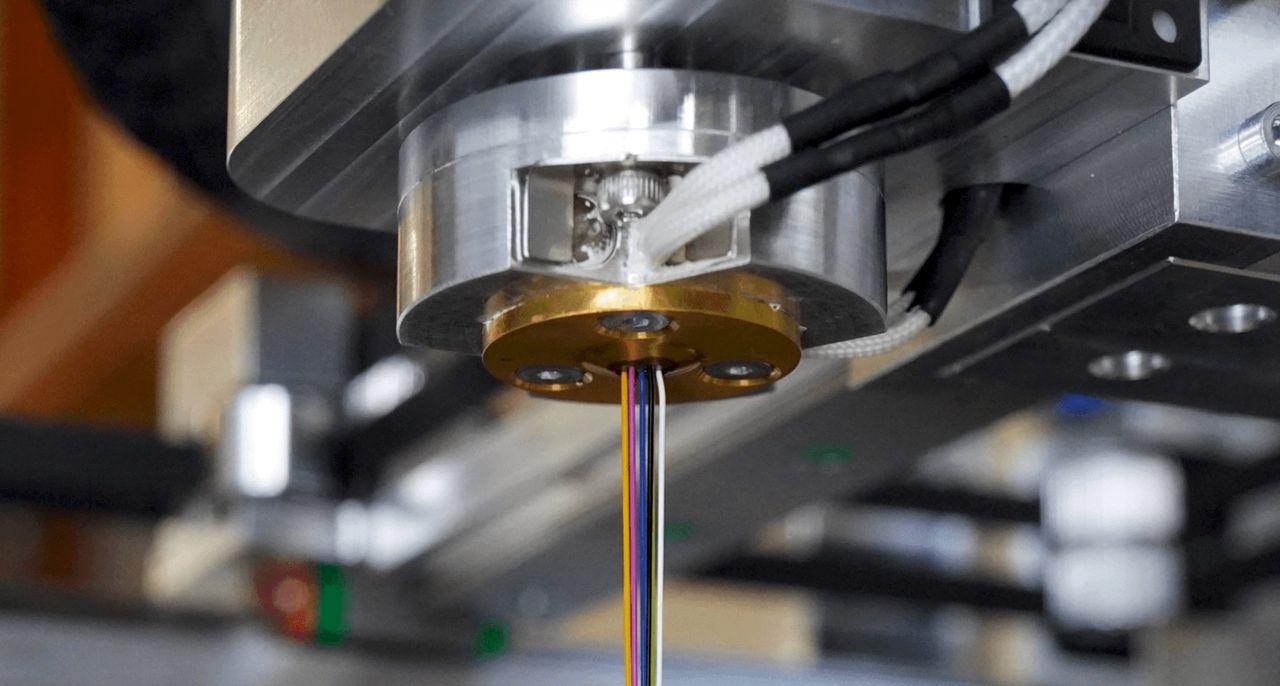
LIQTRA has developed a very unusual 3D printing system that’s up to 4X faster than typical FFF implementations.
Speeding up the FFF 3D printing process is a goal of many companies and developers, simply because it just takes too long to produce large prints. Why wait days when a print should be done in hours or minutes?
The usual approaches for speeding up FFF 3D printing involve one or more of these:
- Moving the print head faster
- Increasing the nozzle diameter to deposit more material per second
- Tweaking the GCODE toolpath to be more efficient
- Adding another toolhead (or more) to print other portions of the object or more objects
All of these offer some benefit, depending on the solution and application.
Now there’s another very different approach to print speedup from LIQTRA: multi-nozzle, which they call “LIQTRATM”.
The idea behind the multi-nozzle system is straightforward: have many nozzles extruding all at once. If you look at the image at top, you will understand what’s happening in the LIQTRA design.
This makes much sense when you consider a typical GCODE tool path: the print head and nozzle move back and forth, largely repeating movement patterns over and over.
What if those motions could be more efficient? What if there could be more material extruded during each sweep of the toolhead?
There’s a bunch of challenges to overcome, however.
One is creating a “super nozzle” that has multiple input filaments and multiple output nozzles. We’ve previously seen multiple input nozzles for multi-material devices, but the LIQTRA approach involves both ends.
The second issue is control of the extrusion. In a normal single extruder setup, the extrusion starts and stops at appropriate locations on each movement of the toolhead. However, if you were to examine these motions you’d find they are slightly different from each other even though they largely follow the same path.
In other words, extrusion line 2 would terminate in a slightly different position than extrusion line 1, as would lines 3, 4, and … n.
This means that LIQTRA would have to find a way to precisely control extrusion start and stop so that the toolhead could continue deposition for some nozzles, but not for others.
Starting and stopping a nozzle is a tricky process. Usually it’s done by stopping the extruder motor, but that introduces problems. The fluid pressure of the softened thermoplastic makes the stoppage “fuzzy”, and there can be drips, which we normally observe as “stringing”.
That method clearly would not work in the multi-nozzle system, so LIQTRA devised a unique valve system to more precisely control the extrusion. In the diagram above you can see a cross-section of one of these nozzles. As pressure is applied from the left, the internal structure of the nozzle clamps down and immediately cuts off the flow. LIQTRA said this happens in less than 20 microseconds, so basically instantly.
Each of the nozzles in the multi-nozzle arrangement have this valve system, making it easy to control the extrusions.
However, there’s another issue: who’s switching the valves open and closed? Typical 3D print slicing software has no concept of valves and especially how to coordinate broad movements with multiple extrusions. That’s why LIQTRA composed their own slicing software to incorporate these functions.
The result is a FFF 3D printer that can produce prints typically with a 75% reduction in duration. That’s very powerful and not only speeds up a single print, but can also be used to dramatically increase part production throughput. Watch this video demonstrating the concept:
LIQTRA seems to be operating as a service, where they retain the technology and simply print parts at high throughput rates. That’s a business model we’ve been increasing encountering, particularly with companies with new and unique technologies such as LIQTRA.
3D printing just got a bit faster.
Via LIQTRA