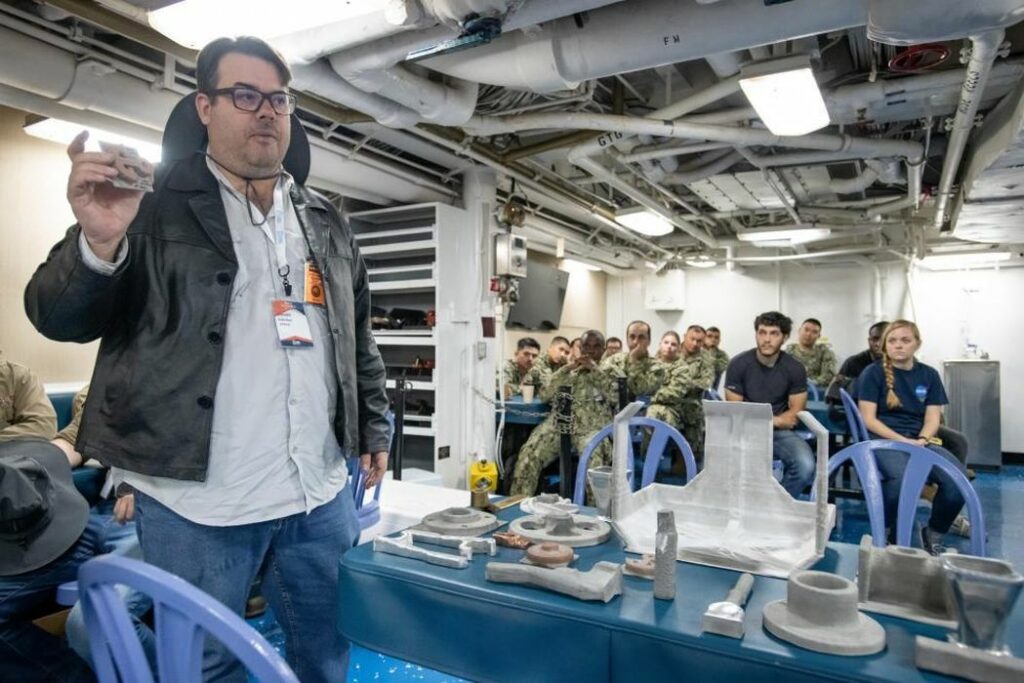
SPEE3D did something very interesting: they 3D printed a metal part on a navy ship.
Australia-based SPEE3D uses a unique 3D printing process that is literally supersonic. Their idea is to blast fine metal powder through a robotically-controlled toolhead at supersonic speeds. When a particle strikes a metal surface, the kinetic energy causes instantaneous molecular bonding — all without the need for heat.
This “cold spray” approach allows the building of 3D objects by simply moving the printhead around in 3D space to build up the object.
The process is extraordinarily fast. Here you can see an 8.5kg copper flywheel printed in only 60 minutes. Not only is the supersonic process fast, it can also handle metals that are difficult to 3D print using LPBF methods, like copper.
One limitation to the SPEE3D process is that it doesn’t have nearly the resolution of LPBF print processes. However, there are plenty of parts that don’t require such resolution. In fact, there are likely many more “coarse” metal parts required.
For several years SPEE3D has been working with various militaries to see how well their system could work in those environments. The most recent test took place with the US Navy in California, where a SPEE3D system was installed on a US Navy ship.
This work was done as part of the US Navy’s Repair Technology Exercise (REPTX) at Naval Surface Warfare Center, Port Hueneme Division. Parts printed included a wrench, pulley, door handle, pump flange, valve handle, impeller, and more.
You’ll note that all of those example prints sound like spare parts that one might require on a ship.
That’s the goal of this exercise: to prove that it is possible to 3D print spare metal parts shipboard, and thus avoid the need to stock heavy and expensive spares — or worse, transport them to the needy ship. Making spare parts on demand would be an incredibly powerful way to increase ship reliability and reduce dependency on central services.
The interest in this concept has been high, and navies around the world have been looking at ways to implement a solution. Several have even attempted to use LPBF solutions, but apparently have been unsuccessful.
This is understandable, because LPBF equipment requires a stable platform because loose powder is deployed on each layer of the print. Should the machine be shaken or tilted, it’s not clear how the print quality could be affected, or even if the prints would complete at all. LPBF depends on gravity and stability.
That’s not a problem when you put LPBF equipment in a factory to make medical implants or aerospace parts, but it is when you put the machine on a navy ship that is tossing about in the sea.
That is where SPEE3D comes in: their cold spray process is mostly immune to shakes and rattles, and should be able to print competent parts in less than stable conditions. That could be ideal for naval spare parts.
Evidently the project was able to successfully produce a number of spare parts using this equipment, proving the concept.
For SPEE3D, this is incredibly good news. It means that they could leverage this development into actual deployments of their equipment on navy ships. Those ships are not necessarily just with the US Navy as well: if proven on one ship, it should work on others in other navies as well.
The technology will also work for commercial shipping, too, and that is a vastly larger market.
I believe SPEE3D just opened a big door for forward movement.
Via SPEE3D