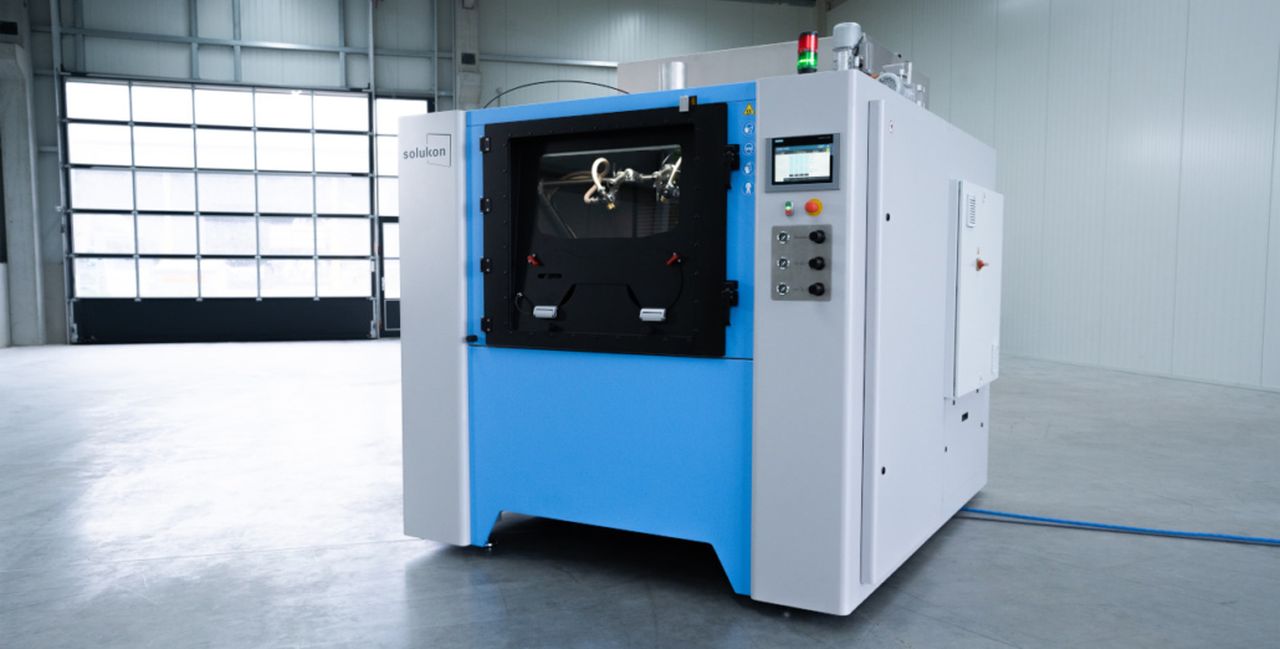
Solukon announced a new series of adapters that should greatly expand the use of the sophisticated post processing system.
Solukon is a German company that specializes in post processing equipment, a growing market in the additive manufacturing space. As more companies adopt the technology, they also discover the troubles of post processing and seek automated solutions. Powder and support structures must be removed, surfaces smoothed, and much more.
That’s where Solukon comes in. They have what is called “Smart Powder Recuperation” (SPR). This is what you might view as a form of intelligent depowdering.
Typical solutions involve vacuums and vibration action, but they are nowhere near as sophisticated as Solukon’s solution.
Here’s how it works: they analyze the CAD model of the prints from the current job, and then using fancy software devise an optimized and unique pattern of rotation and vibration to get all stray particles off the prints.
In fact, the system prevents operators from any exposure to tiny plastic particles used in the 3D printer. This provides a far safer environment than many I’ve seen in the past.
The process is so effective that it doesn’t even require human inspection: it’s been called “witness free” depowdering.
To operate, the Solukon SFP770 device must accommodate the build box from a PBF 3D printer, which is then put through the motions to remove the remaining powder.
Solukon explains the steps involved in their de-powdering solution:
Loading: The build box is placed in the system by a lift truck.
Unpacking: A vibrating sieve cover is placed over the inserted build box, which then rotates gently overhead following an optional programmable process, gradually separating the components from the powder. The loose powder is extracted from the sieve cover directly and without contamination and conveyed to a recycling unit or storage silo.
Transferring: Once the unpacking process is complete, the build box rotates towards the basket and opens the sieve cover. The sieve cover now functions as a slide and the parts are slipped carefully into the basket. If necessary, the automatic transfer process can be paused to manually remove certain components that should not be cleaned automatically. After transfer, the system can immediately be loaded with a new build box, while the components from the first batch are cleaned in the second half of the system, the basket.
Cleaning: The basket rotates in the direction of the blasting unit and begins turning. The glass bead blast and ionized air cleaning process is fully automated and removes residual powder. Process parameters, such as rotation angle, blast intensity, distance or basket rotation, can be easily programmed online by the user.
However, for some unexplainable reason the various manufacturers of PBF 3D printers don’t have the same dimensions and specifications for their build boxes. This means that Solukon must provide adapters for specific machines in order for them to use SPR.
The news is that Solukon announced adapters for the EOS P1 and P5 series of SLS 3D printers. These devices are extremely popular and are used in production scenarios worldwide.
But for each installed P1 and P5 unit, there is a corresponding amount of tedious post processing activity taking place. Now all of these operations have the option of eliminating manual labor for at least the de-powdering step.
Depending on the scenario, this could be very financially advantageous for the operator. Production 3D printers make money when they are operating constantly, and that means a continuous flow of completed prints that require de-powdering. This option could allow a production facility to either reduce staff or re-use the staff for other work.
EOS 3D printer operators should be quite interested in this solution.
Via Solukon