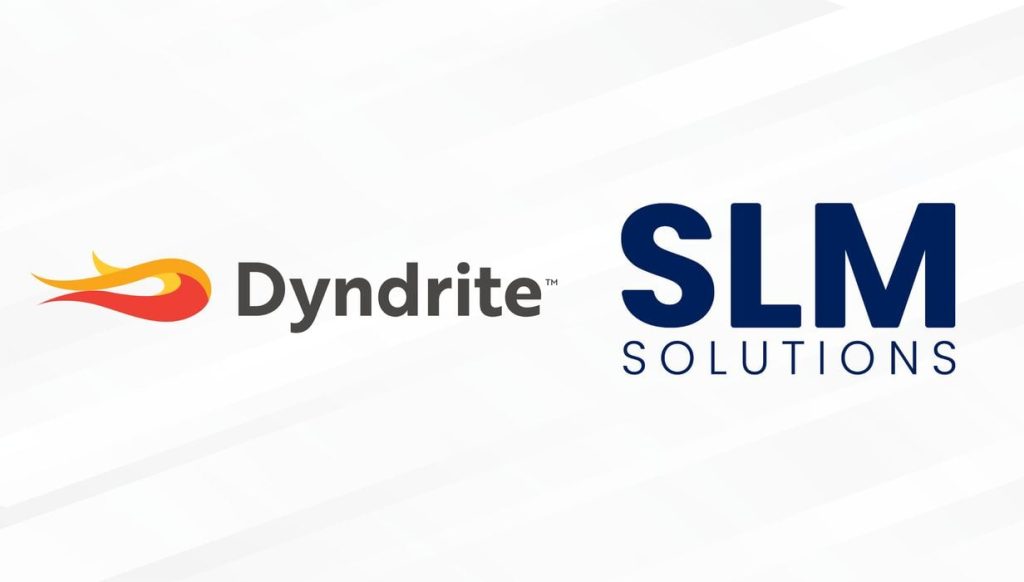
Software has become increasingly important in 3D printing in multiple dimensions.
As someone who’s followed the progress of 3D printing for now over 15 years, I’ve seen quite a progression of the technology. When I began looking at the tech there were a handful of patent-protected large companies and a few rough startups in garages looking for the next big thing.
Since then things have developed in dramatic fashion. We now have literally hundreds of 3D printer manufacturers, many using patent-expired processes, as well as a number of new entrants with revolutionary new tech, including volumetric 3D printing.
But all through that progression there has been a significant emphasis on improving the hardware.
We’ve seen machines have new processes, better quality components, more rigid frames, etc. These were key to today’s world of machines that can, usually, reliably print good quality prints at relatively low cost.
For the machines using the standard 3D print processes, there seems to be a plateauing of the hardware in recent years. The FFF process, for example, now is used by many producers, and it’s beginning to be difficult to distinguish between options. Most of them simply have pretty much the same hardware — and some have literally the same components inside if you care to look.
There are hardware innovations still occurring, of course, but my suspicion is that they will be overcome in the very near future by software improvements.
Consider Klipper, the open source firmware replacement for desktop FFF devices. This software provides advanced methods of leveraging the 3D printer’s motion system to achieve far higher print speeds. However, it can’t really be effective unless the base machine has a minimum quality level of components and motion system.
But what if typical machines end up with that quality level? What then would prevent every machine from using Klipper and gaining faster print speeds?
This is a demonstration of how advanced software can combine with hardware to achieve a far better outcome.
It’s not the only one, either. There are multiple instances of 3D printer manufacturers now leaning on software to make their products better. This happens not only with desktop equipment, but perhaps even more frequently on commercial equipment.
Some examples:
- Linking cloud-based 3D model repositories (e.g. Creality Cloud)
- Integrating with third party job preparation software (e.g. Lychee Slicer)
- AI vision tools to detect print failures (e.g. Quinly Vision)
- Machine learning systems to monitor print quality (several)
- Automated machine calibration systems (many)
- Advanced slicing procedures (e.g. Arachne algorithm)
Another very recent example is SLM Solutions’ arrangement with Dyndrite. Dyndrite produces AGK, the “Dyndrite Accelerated Geometry Kernel” that leverages GPU hardware to rapidly process and handle extremely complex geometries and produce the associated toolpaths. Their arrangement allows the creation of complex toolpaths for SLM Solutions’ equipment using AGK, bypassing slower slicing solutions. The SLM Solutions hardware is the same, but the software provides more capability.
All of these have one thing in common: they make the hardware do a lot more than it could on its own. In particular, the AI-based tools could perform seemingly magical feats that otherwise would require human intervention.
As software advances, and the cost of increasingly powerful controller boards decreases, we’re likely to see the scales tip in favor of software upgrades, rather than hardware upgrades.
That could be a much better world, because hardware upgrades are expensive and infrequently done. On the other hand, software upgrades are far easier to implement.
If I were running a 3D printer manufacturing company, I’d be considering how to beef up the software department, particularly with AI skills.