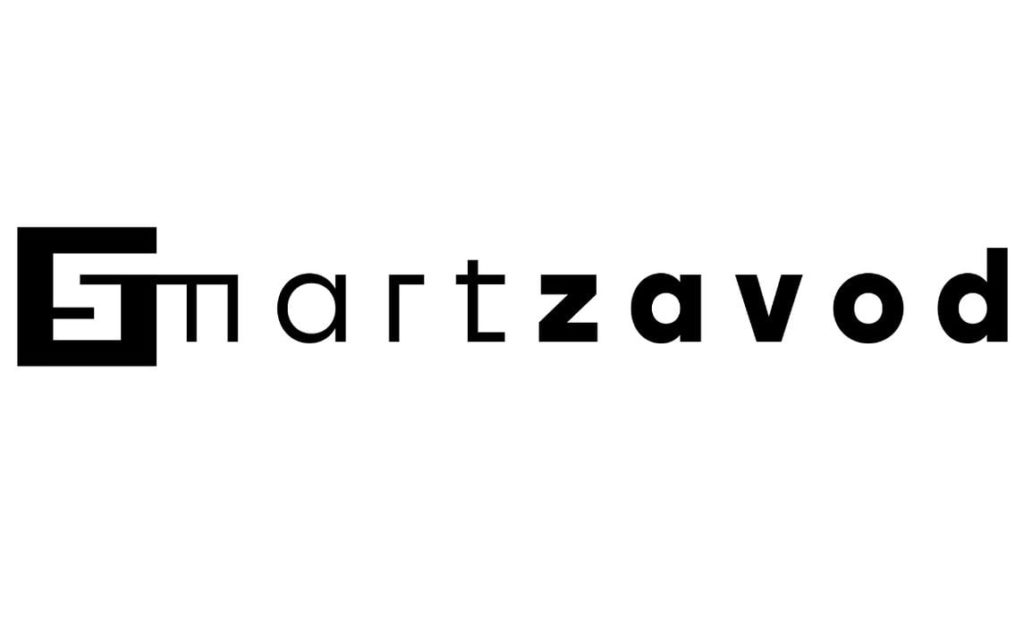
SPONSORED CONTENT
A German-Ukrainian startup has developed a new system for not only 3D printing, but multifunction manufacturing.
The company, named after the Ukrainian words for “Smart Factory”, is the product of Okeksii Solntsev, the company CEO, and Anton Yakhno, currently CTO. The two masters students at the University of Applied Sciences in Hof, Germany, built a prototype of their concept and subsequently formed SmartZavod.
But why build yet another 3D printer? There are literally hundreds of them on the market, many of which offer identical functions. How does SmartZavod differentiate their system from all the others?
The answer relates to a trend that’s been underway in 3D printing for several years now.
As the technology gradually improved and began to provide more high-quality parts, it drew the attention of manufacturers seeking to use 3D printing to produce end-use parts. However, the problem was that production parts require many different materials.
For a long time prior to this period the list of materials available to 3D print was relatively short: PLA, ABS, PETG and a few others. Once the chemical industry came to understand the long-term potential of 3D printing, they began to release more of their materials in forms suitable for 3D printing.
That was good news for manufacturers, but it challenged 3D printer manufacturers, who found their default equipment could handle only certain types of materials. As a result we saw an explosion of specialized extruders, hot ends, build chambers and other hardware components to address these new material needs.
For manufacturers it meant they would often have to swap toolheads on their 3D printer for new print jobs, or even acquire multiple devices and dedicate them to specific materials. That solved the problem, but caused extra cost.
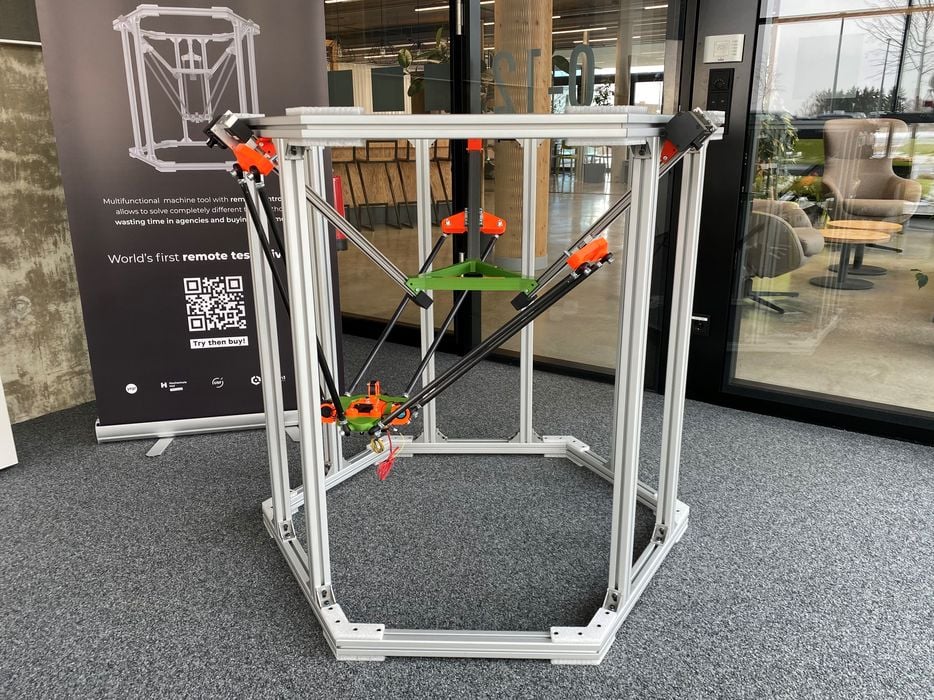
Enter SmartZavod, which has developed a solution to these woes. Their device, the CEH1, is not only multimaterial , but also multifunction.
The CEH1 uses a delta-style motion system that provides a straightforward method of swapping toolheads. It’s so easy that the machine actually automates the process of changing tools at the touch of a button.
This means that the machine could, for example, swap out the active 0.4mm nozzle TPU toolhead in exchange for a high speed 2.0mm ABS toolhead. All this could happen during the print job without the need for human intervention.
Even better, if you can swap out a filament extruder, why not swap in different kinds of tools? By swapping in CNC mills or laser engraving toolheads the function of the machine could become completely different — again all during a single print job. Note that some toolheads could potentially perform post processing actions, while it’s still “in the print job”.
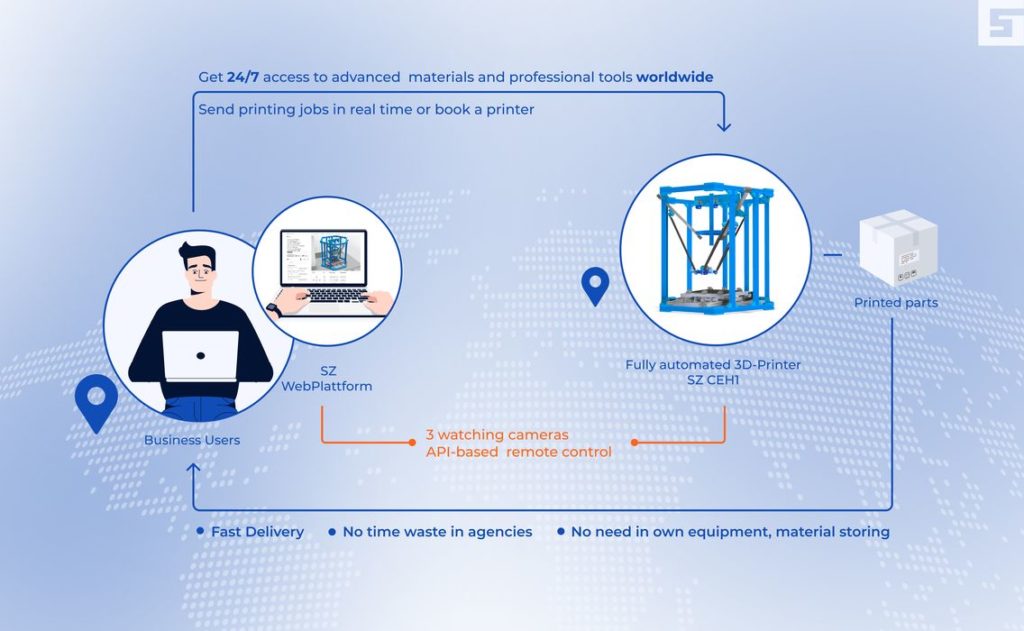
Normally multifunction devices require the operator to physically install the alternate toolheads before the job begins, usually meaning the job is either “all 3D printing”, or “all laser engraving”, and so on. The CEH1 should be able to produce objects made from not only multiple materials, but also using multiple making processes.
The initial version of the CEH1 will include three 3D printing toolheads:
- Standard tool: Dyze design pro 0.4mm + multimaterial upgrade for 6 filaments
- High flow tool: Dyze design Typhoon ~2mm nozzle
- 2nozzle tool for printing with detachable supports
However, in the near future SmartZavod expects to add these toolheads and features:
- Liquid adhesive dispenser tool
- CNC for part finishing
- Different printing heads with different nozzle sizes and nozzle materials
- Possibilities to combine different tool/materials for one printed part
All of this activity takes place in a very generous 400 x 400 x 400 mm build volume, which includes a unique carbon plate build surface that can be heated up to 130C. Future versions of the device might include active chamber heating for high quality part production.
One very interesting feature is a method of continuous 3D printing, where there is an automated bed cleaning system. That will become more important as you read on.
The CEH1 is operated from a cloud system SmartZavod calls “WebPlatform”. This system allows an operator to work on the CEH1 remotely to start and monitor job activity through webcams and sensors. Importantly, because the system is entirely automated, there is little need for the operator to physically attend the machine. Remember, the CEH1 can not only swap materials and tools, it can also remove prints from the build plate. In other words, multiple sequential jobs using different materials could run automatically, all controllable remotely through WebPlatform.
These features make the CEH1 a small production machine that, in theory, could operate on its own until it runs out of material.
The company’s innovation doesn’t stop at the hardware level: they also plan to deploy a “rental” program that would permit companies to easily get started without incurring a large one-time expense. This might be a good way to “try before you buy”.
SmartZavod has developed a fascinating new concept in 3D printing — and manufacturing — with a device that, when equipped with the right toolheads and materials, could make relatively complex multimaterial objects in a completely automated manner.
At this time SmartZavod is building the first few prototype devices, and is seeking participants to test them. If you’re interested, please head to their website and register. SmartZavod is particularly interested in working with those testing the remote operations features.
Via SmartZavod