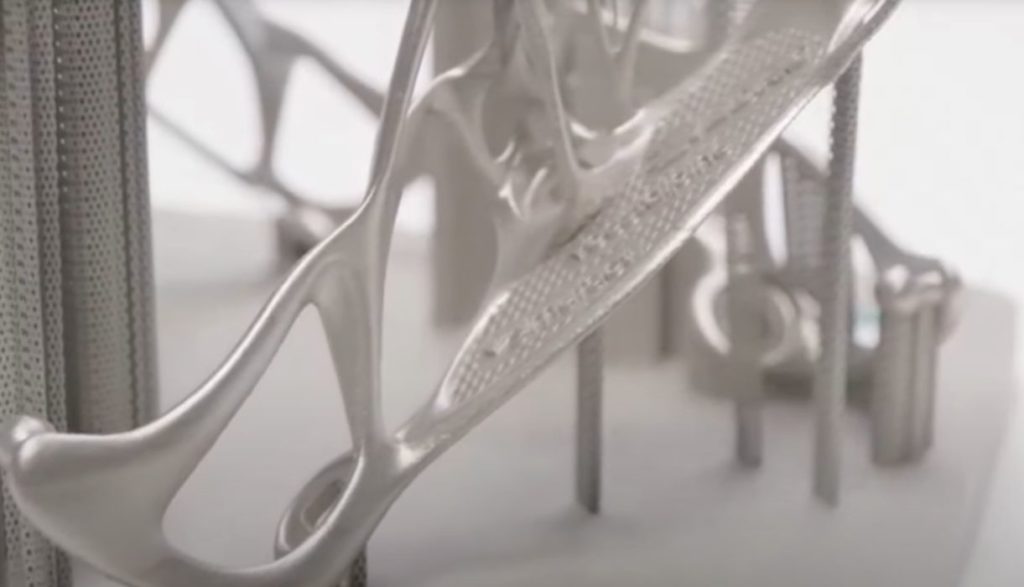
SLM Solutions announced a new technology called “Free Float” that dramatically reduces the need for support material.
Support material is the bane of metal 3D printing using PBF processes. Support structures are required to handle several issues during 3D printing, including fixing the position of “loose” elements and managing the mechanical stresses generated by the tremendous heat gradients during and after printing. In some cases supports are added to help draw heat away from the hot spots for thermal management.
Support Structure Challenges
However, while supports are desirable during the print job, they are not desirable afterwards. That’s because they have to be literally cut off using metalworking tools. While this process can be automated in some cases using advanced (but expensive) CNC equipment, it is often done manually using hand tools.
That post-processing is expensive due to the labor component, but it also introduces delays in finishing the part. As a step in the production process, support removal can become a bottleneck if overloaded with parts. Support structures themselves consume quantities of expensive metal powder, only to be thrown away after post-processing.
The best outcome would be to avoid support structures entirely, but that’s not truly achievable with the LPBF process. However, it is possible to minimize the amount of supports.
SLM Solutions Free Float
That is the plan from SLM Solutions with their new “Free Float” technology. It’s not hardware, as we thought, but instead is a way to run a print job with more highly tuned parameters and some added smarts.
Essentially they are leveraging their existing hardware and computing resources with clever software to decrease the need for support structures as much as possible.
For example, rather than having print parameters for the entire build chamber, the Free Float system can adapt to local conditions in different portions of the build chamber during the print job.
The results are impressive. SLM Solutions says the need for supports drops by a very large percentage. They don’t say exactly how much because this clearly depends on specific situations and geometries, but the point is that there’s far, far less support used.
While they call the system “support-free”, it really isn’t. It’s more like “support-minimum”.
SLM Solutions said Free Float can work for “any material”, but initially they will offer the service for Inconel and Titanium metals.
The best news is that Free Float will be available not only on new SLM Solutions equipment, but also on most of their prior models as well. As software, Free Float is a lot more portable than if it had involved new hardware.
SLM Solutions showed some impressive results. Apparently Free Float is able to 3D print “long range” overhangs up to ten degrees, and short range overhangs up to only five degrees. That demonstrates the enhanced ability by Free Float, and you can imagine how this could affect a given geometry with that in mind.
In general, however, the Free Float concept should allow for production of thinner walls, much sharper edges and increase surface finish quality. It’s also possible it may decrease porosity of printed parts, making them stronger.
The ability to handle more overhangs also results in the a corresponding ability to use different orientations during 3D printing. In general orientation is driven by overhangs rather than strength requirements, but the ability of Free Float to mostly ignore overhangs allows new orientation possibilities.
Free Float is set up as a kind of post-processor for slicing. Files are run through a secondary process to convert them into “Free Float” style, which can then be printed.
SLM Solutions said Free Float can be ordered now for new systems, and will ship some time later this year in Q4.
Via SLM Solutions