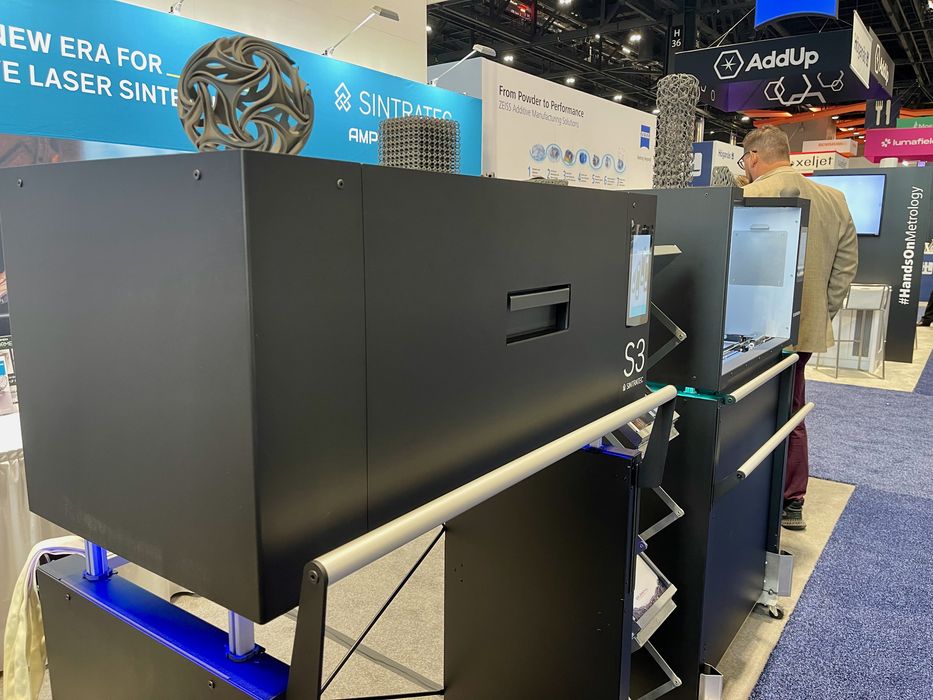
Sintratec has two interesting news items: a modular production system and an ability to print metal 3D objects using SLS 3D printing.
Swiss-based Sintratec is well-known for their low-cost SLS 3D printing systems that broke pricing barriers some years ago. Since the introduction of their first budget-friendly device, the company has continued to innovate and provide new and more sophisticated SLS systems. They currently offer the S2 and S3 systems, which only differ in their power levels. The S3 can print more rapidly than the S2 due to the increased energy available.
Our recent chat with company representatives revealed two innovations we hadn’t seen before.
A Modular Approach for SLS Print Box
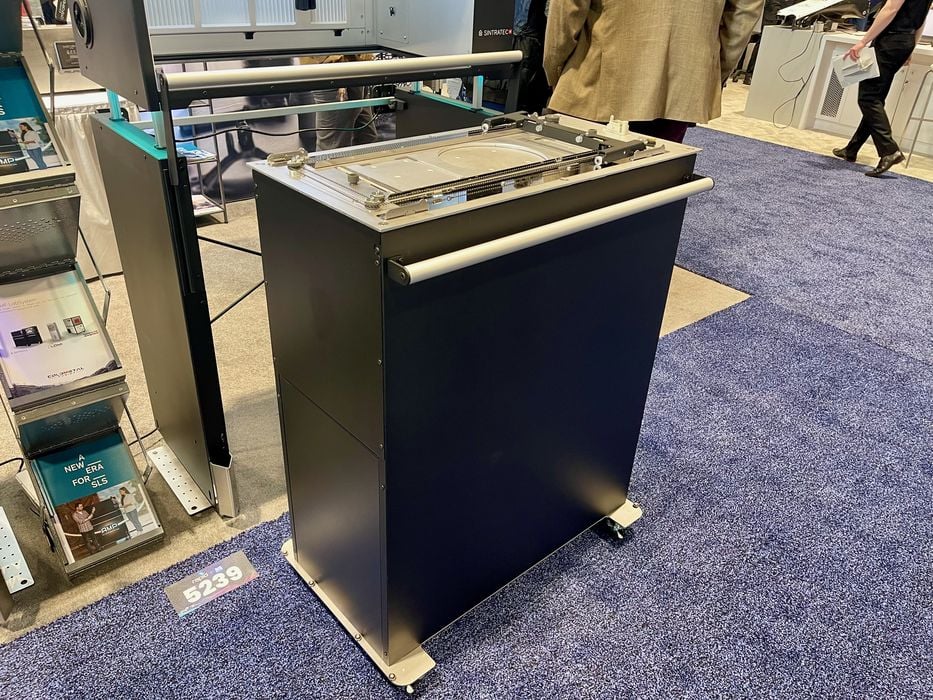
One is a modular-style approach for their SLS print box. SLS 3D printing is a powerful technology, but one challenge is that it takes considerable time to clean out the print box to remove the completed prints.
Sintractec overcomes this limitation with a new modular approach, leveraging a swappable build module. Here’s how it works:
- A fresh build module is rolled under the S2 (or S3) 3D printer
- A latching mechanism connects the two securely
- The print job proceeds
- After printing, the build module is unlatched and moved aside
- A second fresh build module is rolled under the printer and latched in for a second print job
- The first print module is cleaned out while the second job continues
This process allows for parallel operation and achieves maximum throughput for the 3D printer.
From our visual inspection, it seemed quite straightforward to move the build modules and operate the latching mechanism.
There’s another very interesting advantage of this modular approach: it is trivial to change materials, as all powder remains in the build module. The printer itself is never contaminated with a different material and requires cleaning.
Metal 3D Printing with SLS Technology
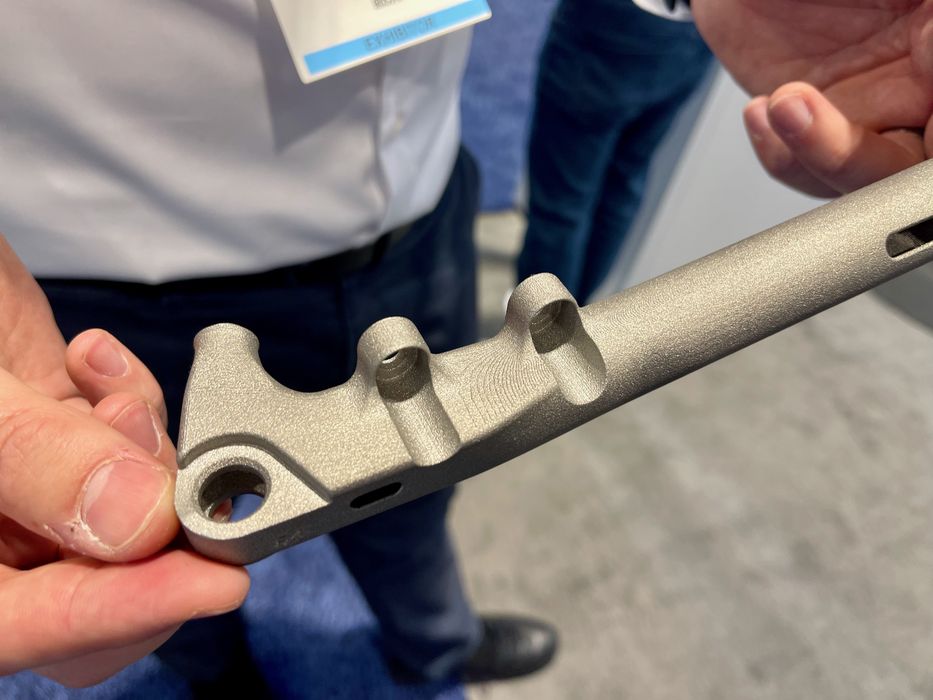
The second innovation we discussed with Sintratec was about metal 3D printing. While metal 3D printing is a well-established technology, Sintratec is using the SLS process to make metal objects, which is traditionally a polymer technology.
The process involves a new material that combines metal powder and a polymer. A part is 3D printed in the material in mostly the usual manner, resulting in a “green” part that is both metal and polymer. A post-processing step removes the polymer and sinters the metal particles together, producing a smaller but complete metal part.
Sintratec said there is one key advantage to this: the green parts are quite robust, unlike the typical highly-fragile green parts produced in binder jet systems. They are so strong they can be power washed without incident. Currently, the metal process is being beta tested, but it’s likely Sintratec will release this new metal capability later this year, perhaps by Q4.
Via Sintratec
Sintratrec’s approach to produce metal parts appears very similar to what DTM developed and commercialized in the late 90s with the RapidTool process.
Due to high levels of shrinkage during the debinding and sintering stages, the accuracy of the process restricted the range of applications for these parts. Also, as the parts had a high level of porosity, an extra infiltration step was required to reach full density.
3D Systems (which had by then acquired DTM) stopped providing materials for the process in the early 00s.