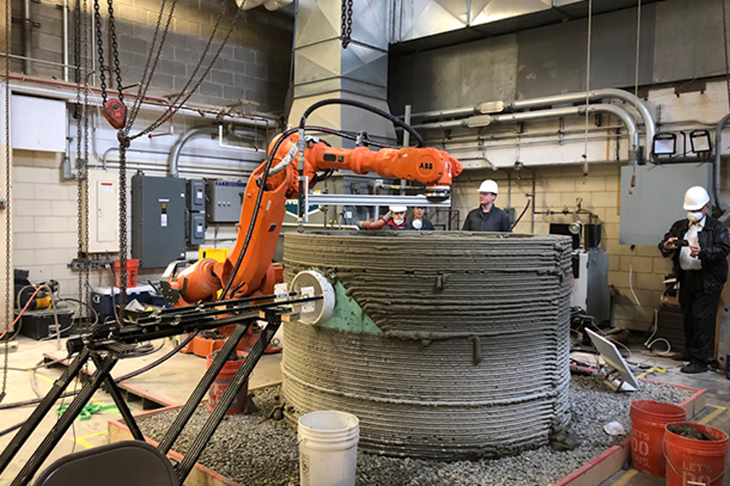
Charles R. Goulding and Joseph Castine build on foundations of advanced concrete 3D printing with a look at SIKA’s involvement.
SIKA AG is a Swiss multinational specialty chemicals company supplying the building sector and motor vehicle industry. Founded in 1910 with the invention of Sika-1 — a quick setting waterproofing admixture for mortar, which was used to waterproof the Gotthard Tunnel — SIKA has continued to break the mold of the traditional company throughout its rich history.
SIKA continues to push the boundaries of what’s possible with 3D printing technologies. Currently, the company stands as one of the leaders in concrete 3D printing techniques. These techniques offer unique applications which can result in the production of concrete shapes that were not previously possible with traditionally framed concrete.
This 3D printing concrete process is able to be integrated with CAD software and can be automated using SIKA’s own MiniShot system. The print head of these 3D concrete printers is perfectly precise and it can be used for many applications including the formulation of 3D mortars. Since the traditional method for construction uses concrete placing, the team at SIKA sought to develop an efficient and precise concrete 3D printing solution. These concrete 3D printing machines use a mix that is similar to that of traditional concrete methods, with altered ratios to allow for smooth flow which can prevent nozzle backpressure and rupture.
Other developments in the concrete additive manufacturing space include efforts made by ICON with their ICON Vulcan and Vulcan II which have allowed for the creation of 3D printed communities in Tabasco, Mexico. These Vulcan 3D printers use proprietary concrete mixtures called Lavacrete which can be sourced from local materials with zero waste. Using these 3D printing techniques new wall systems which are higher in quality can be made with lower costs.
This new construction method via concrete printing eliminates the need for traditional concrete molds and thus can increase the cost efficiency of concrete building. Currently the production of conventional concrete requires between 1700 and 1800 megajoules of energy, which represents the energy equivalent to powering 500 100-watt lightbulbs for 10 hours.
A research team at Penn State has designed a 3D concrete printing system to compete in a NASA challenge. The principal investigator on the team Ali Memari, the Bernard and Henrietta Hankin Chair of Residential Construction and professor of architectural engineering and civil engineering, has said, “once 3D printed example buildings are created using this system, the construction industry will realize the benefits.” Among these benefits, Memari mentioned “minimized construction waste, faster construction, less labor, and more economical construction in areas with limited-resources or hazardous areas.”
President Biden has recently released details of his Build Back Better plan which will result in $3 trillion invested into new infrastructure and refurbishment of existing infrastructure. President Biden has also reaffirmed the United States’ commitment to the Paris Climate Accords. With these stakes in building up infrastructure and commitment to climate change, this new concrete additive technology may prove useful.
Companies engaging in 3D printing advancements or experimentation with 3D printing technology may be eligible for the R&D Tax Credit.
The Research & Development Tax Credit
The now permanent Research and Development (R&D) Tax Credit is available for companies developing new or improved products, processes and/or software. Eligible costs include U.S.-based employee wages, cost of supplies consumed in the R&D process, cost of pre-production testing, contract research expenses, and certain costs associated with developing a patent. As of 2016, eligible startup businesses can use the R&D Tax Credit against $250,000 per year in payroll taxes.
3D printing can help boost a company’s R&D Tax Credits. Wages for technical employees creating, testing and revising 3D printed prototypes can be included as a percentage of eligible time spent for the R&D Tax Credit. Similarly, when used as a method of improving a process, time spent integrating 3D printing hardware and software counts as an eligible activity. Lastly, when used for modeling and preproduction, the costs of filaments consumed during the development process may also be recovered.
Whether it is used for creating and testing prototypes or for final production, 3D printing is a great indicator that R&D Credit eligible activities are taking place. Companies implementing this technology at any point should consider taking advantage of R&D Tax Credits.
Conclusion
As the 3D printing revolution continues, forays into other industries prove fruitful for advancements within those industries. As far as the 3D printing of concrete goes, advancements in this technology can help to reduce waste and carbon emissions, while enabling construction in otherwise hazardous and uninhabitable locations. With entities such as NASA incentivizing this technology, and the US reaffirming beliefs in climate change while building up the country’s infrastructure the future of 3D concrete printing looks extremely bright.