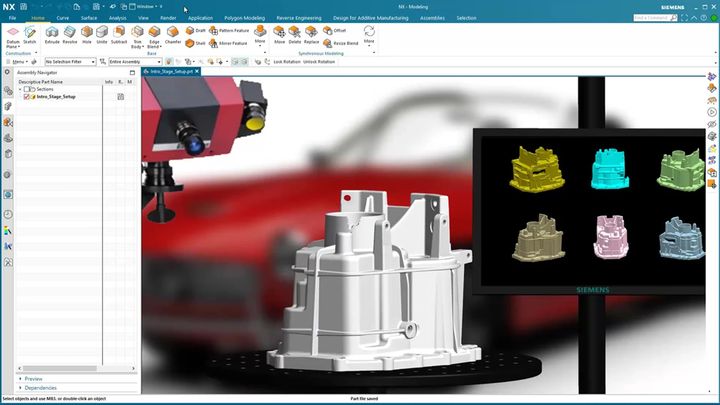
When Siemens implemented its continuous release plan almost two years ago, it promised enhancements to NX every six months.
This month, the company released the newest update of its NX software with enhancements to model-based definition, Synchronous Technology and an improved extensive CAM enterprise.
The desktop CAD and CAE software now has more simulation functionality and an automated multi-physics platform. The company has also added new features, including algorithmic modeling, additive manufacturing design and convergent modeling upgrades.
Sketch
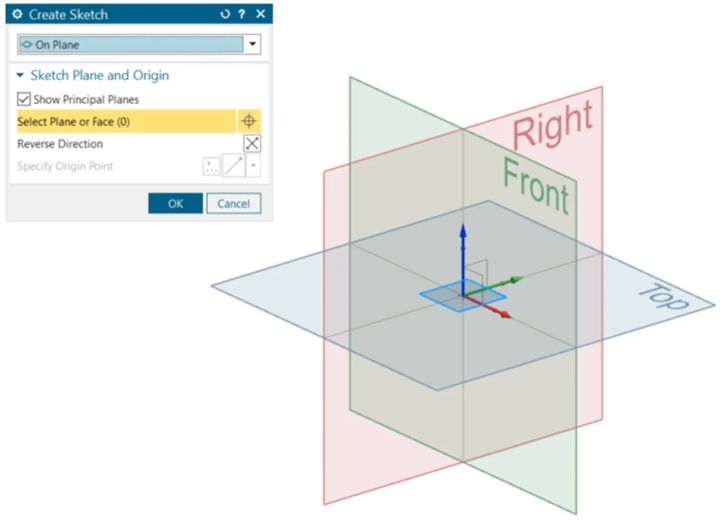
Changes start where the design process begins: the sketcher. Enhanced visual feedback uses artificial intelligence (AI) to perform geometric constraint solving and guess which shapes the user needs based on the rest of the design. Instead of using CAD after the initial sketch, the software now allows users to employ CAD during the sketch phase. The company has also reduced the required click count and labeled the principal planes on which to sketch.
Algorithmic Modeling
Through NX software, users can now create a customizable design without the need for manual modeling and complex programming. With algorithmic modeling, users can simply describe the design using rules to define the structure, such as the number of floors in a building or the slant of an object, and let the program build the structure for them. Users can experiment with algorithmic modeling until they are happy with the results. The feature also allows users to save time by producing product forms and saving them as templates for use in other workflows. The feature also helps users create algorithms using a logic editor. The engineer can then save these algorithms as a template for their designs.
Convergent Modeling
Siemens has added the ability to create convergent bodies with mixed geometry that combines scan data and precise and continuous CAD geometry, which is helpful in reverse engineering. Siemens has also added a Replace Face of Mesh command and made available an optional Implicit Modeling module that allows users to create equation-driven structures and complex designs.
Additive Manufacturing Design
Additive manufacturing design requires fewer resources than CAD but offers greater flexibility and speed in designing structures. It allows users to create different parts and then combine them into a single lattice structure while improving quality and speed. This simplifies assembly because there are fewer pieces.
The wrap mesh command helps users make STL/mesh models for 3D printing and wrap a volume to make a watertight mesh body. The software now has improved multi-axis and planar printing through new support profiles, coating capabilities, and CLI slicing.
Read more at ENGINEERING.com