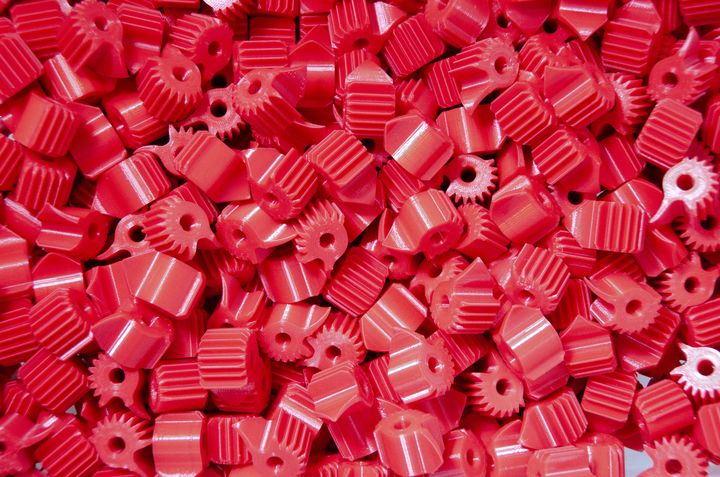
I’ve been doing some thinking about automation lately and realized there are several things that should be covered by 3D print automation solutions.
With the sudden rise of belt 3D printing and other automation solutions, there are implications when producing larger quantities of items. This is not a concern of “normal” 3D printer operators because in most cases, one job equals one output. You know how to unload and post-process the print, and what it is for.
Those are not happening on a 3D print automation system. The purpose of automation systems is to enable the continuous and mostly-unattended production of a series of objects. These objects might be identical, but they could also be unique, or a mix of both.
And they should be handled with the absolute minimum of human intervention. After all, that’s what automation is all about.
Far too often I see automated 3D printers that merely consider the problem of removing the object from the print surface. While that’s obviously necessary, it is only one of the human labor steps that are required to produce objects. A true automation system would account for all — or the majority of — human labor required to fully complete the object.
Let’s take a look at a few that come to mind.
Automated Post-Processing
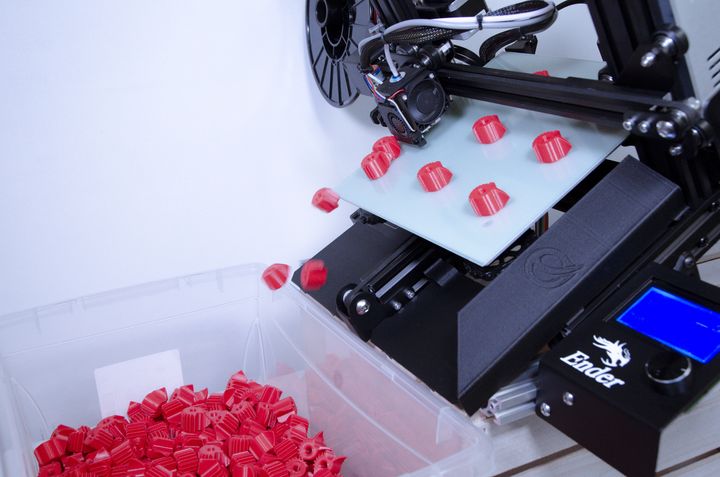
Almost all 3D prints require some level of post-processing, with perhaps the least of which being to remove a skirt from the print. However, some require far more, and usually this involves removing support material.
Support removal can be incredibly tedious and quite manual. While some vendors like Rize have made the manual process efficient, it’s still manual. The best approach here would be to use soluble support, and have the completed prints move into a solution automatically dissolve the supports. That may require additional hardware to hold and circulate the solution.
Increased Material Loading
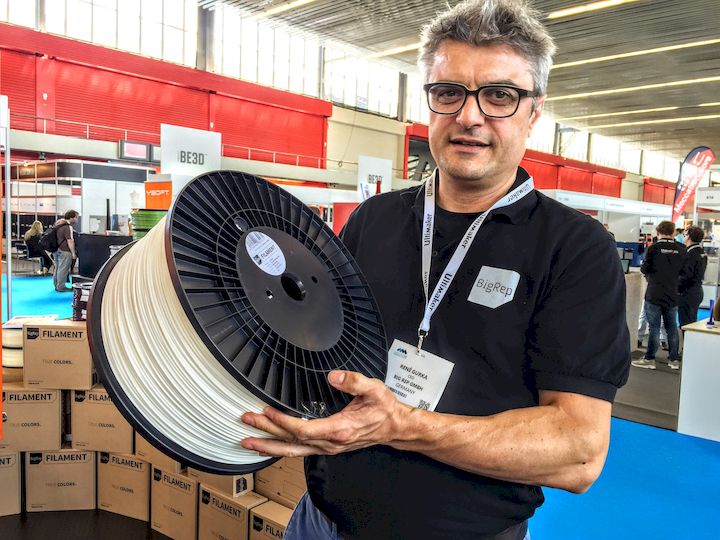
Continuous 3D printing can consume a lot of material, far more than a single 3D print job. Thus it is important for automated 3D printer designers to consider how to supply the maximum amount of material to the device.
This could include using extra-large spools. I’ve seen up to 8kg on a spool myself, but 2kg spools are now relatively common. These should be accommodated in some way to allow for longer continuous operation.
Automated Object Identification
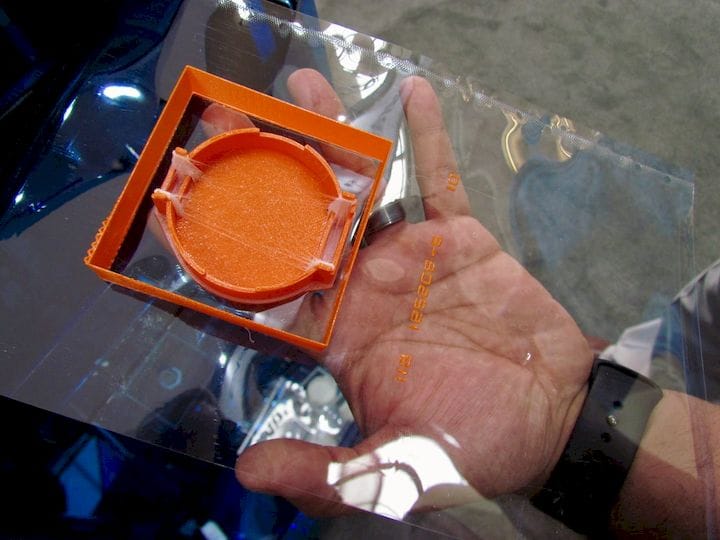
This one is almost never seen in automation solutions, but will become immediately important when more than one client’s objects are produced. The problem is this: if a bucket is collecting objects, how do you know which one is which? How can you quickly find Client X’s objects in the massive pile? This is even worse if you have a stream of customized objects that appear identical.
A solution could be to add some kind of automated tag to each 3D print that would allow for easier physical sorting after the fact. I imagine a small tab at the base of the object could be embossed with some identifying information.
Software to generate GCODE for the machine should have a feature to allow tagging of some kind. For example, serial numbers might be automatically generated and then embossed.
3D Print Stream Operations
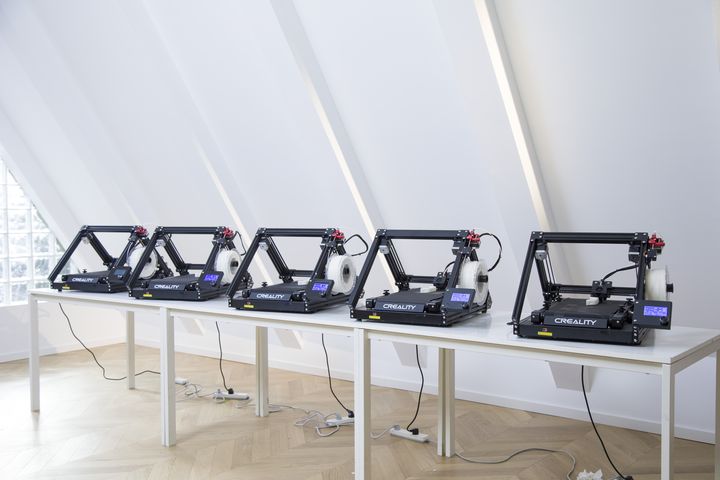
When I first used a belt 3D printer there was a problem: the slicing software generated only one print at a time. In order to achieve “streams” of prints, I had to manually paste GCODE sections together, separated by “eject” commands. This worked, but should be done automatically by the control software.
Alternatively, an automated 3D printer might have a dispatch system that waits for printers to become available, and then send a new job to them. This approach has been done on several array 3D printing solutions.
Automated Quality Control
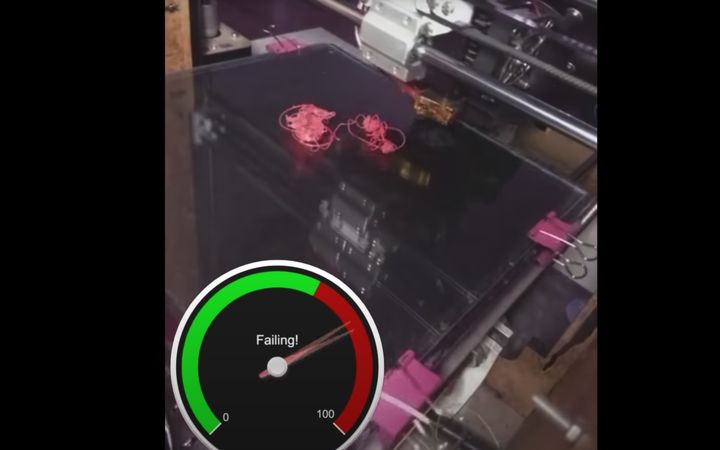
When a 3D printer is doing only a single job, it’s easy to know if the job succeeded: you look at the result. You may find it’s a good print, a messed up print, or a total spaghetti-like failure.
But in an automated system this would have to be determined automatically. This may require a more advanced solution, such as the AI-powered Spaghetti Detective or similar system.
Further, upon detection of a print failure, the system should re-print the object, or at least attempt to do so X times before giving up. I’m not sure I’ve seen this feature in any system to date.
Automatic Bed Placement Variance
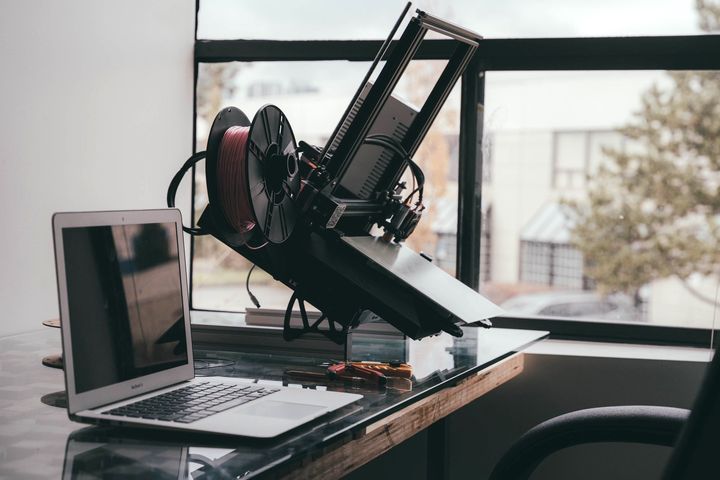
With any continuous 3D printing system I’ve seen there is a looming issue: constant use of one part of the build surface. For example, if you want 459 widgets, you would find that part of the build surface used 459 times, and the rest of the build surface used zero times. That clearly will stress that portion of the print surface, causing it to wear out far more quickly.
The right answer here is to use the slicing and dispatch systems to slightly vary the print location on the print surface for each iteration. In this way the print surface would last far longer.
Intelligent 3D Printer Notifications
Some smart 3D printers have the ability to notify you, perhaps by email, when the print job completes. That’s a great feature, but what if you are 3D printing 10,000 small widgets? Do you want 10,000 notifications? Or zero notifications?
I think there is room for some kind of intelligent notifications for automated 3D printers in which streams, rather than individual object jobs, are the focus. In the above example, the notification could be: “Your 10,000 items have been printed, with 6 failures.” A more sophisticated approach could be to provide in-progress notifications, like this: “2,000 of your 10,000 requested objects have now been 3D printed. Zero failures detected so far.”
3D printer automation is now becoming a thing, but it isn’t complete until all aspects have been covered. Here we find many features that could be added, but I believe there are more yet to come.