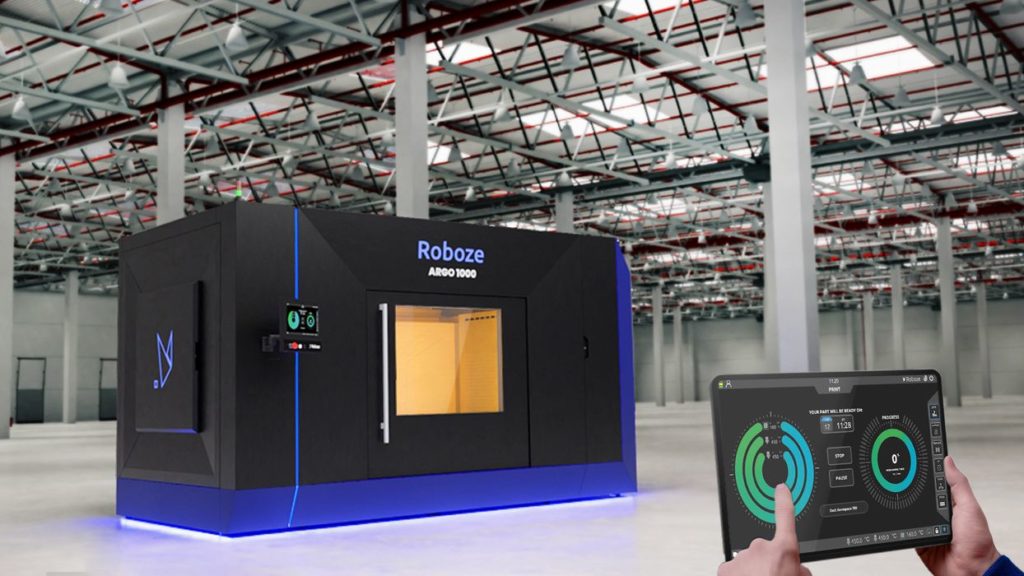
Roboze announced a new 3D printer, the massive ARGO 1000.
There’s a clue in the product’s name, “1000”. This indicates the size of the huge machine’s build chamber, which is, of course, 1000 x 1000 x 1000 mm: a full cubic meter. That is a massive build volume by any standard, but the difference here is that it’s designed to handle high-temperature materials.
Roboze has long focused on high-temperature engineering materials in their equipment. This involves far more than simply heating up the nozzle to higher levels. It also means the machine’s internal components must be designed to withstand high temperatures and function reliably, the build plate must provide appropriate adhesion at high temperatures, and so on.
For example, these 3D printers use gears instead of belts for their motion system, as belts could deteriorate if continually exposed to extraordinarily high temperature.
Roboze solved those issues long ago with their earlier models, culminating in the huge ARGO 500 device shown in 2017. Since then the company introduced a smaller version, the ARGO 350, in 2019.
Now they’ve enlarged the system into the ARGO 1000.
The ARGO 1000 inherits all the capabilities of the prior machines, including the ability to reliably 3D print high-temperature materials. These include PEEK, CF-PEEK, ULTEM 9085, and more.
These materials are entirely suitable for end-use production parts, which is what many ARGO users produce with the equipment.
Why is this important? It’s because these advanced materials are quite strong, yet lightweight and thermally resistant at the same time. That’s a combination normally seen only in metal materials, but they are usually quite heavy.
In other words, it’s possible to substitute advanced high-temperature polymer parts for metal parts in some applications. As long as the operating temperatures don’t exceed the glass transition state of the polymer, you could have a more lightweight part.
That opens the possibility for complex 3D printed parts in many applications where temperatures are higher than ambient, but not exceedingly high. For companies seeking a competitive advantage, this could be one way of achieving that goal: design advanced 3D printed parts that are more lightweight.
This seems to be the case for Roboze clients, who are in the aerospace, energy, automotive and healthcare industries. Each of those markets is quite competitive and increasingly depending on advanced part designs.
The ARGO 1000’s huge build volume will allow two possibilities.
First, larger parts can be produced. With a build volume of a cubic meter, it’s hard to see a bigger build volume requirement except for the most unusual applications.
Second, the larger build volume can be used to produce more smaller parts in a single build. This could increase production throughput and increase efficiency.
Roboze said the ARGO 1000 will be available in 2022, and there is no word on pricing yet.
Via Roboze