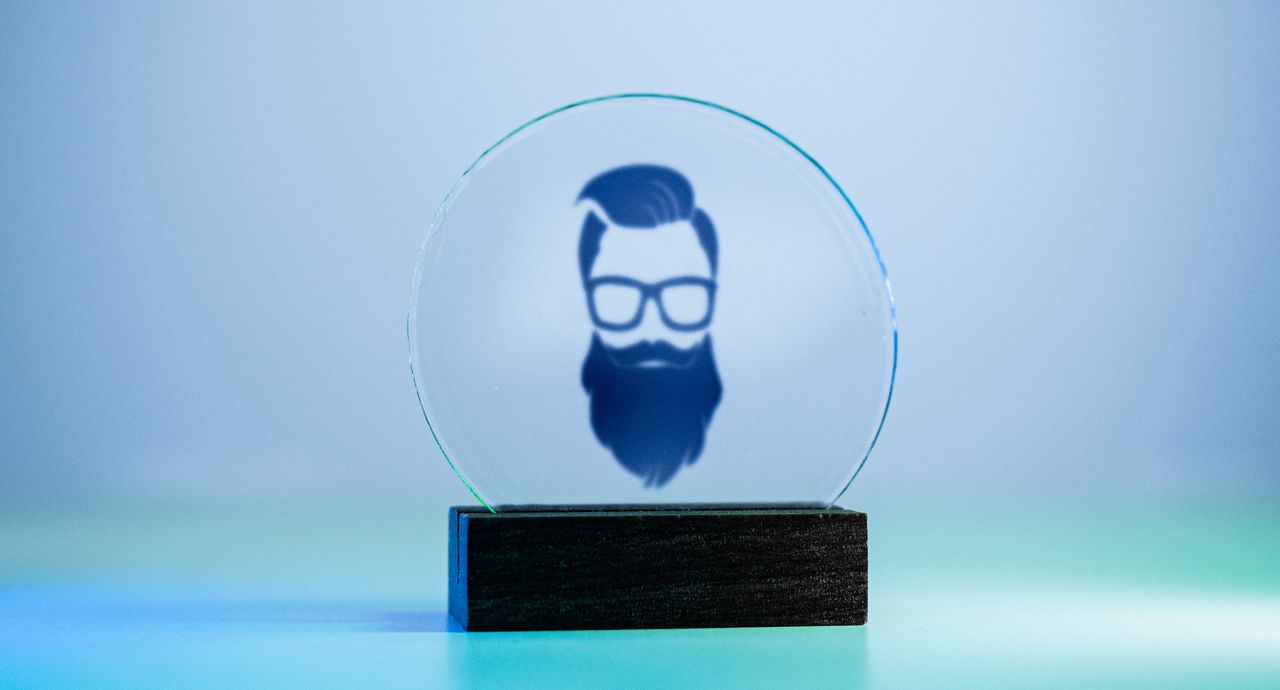
We spoke with Jonathan Jaglom about his new venture, flō, which is using advanced 3D printing to produce advanced lens coatings.
Fabbaloo: How did flō come to be? What was the inspiration behind the launch of the company, and who was involved?
Jaglom: flō was inspired with a vision to disrupt the ophthalmic industry through innovation using Additive Manufacturing (AM). We are using digital printing technology to address the problems existing today in how lenses are being coated.
How this came about is a lot about being at the right time, at the right place, and with the right mindset. I am convinced that only through the trained eye of ‘thinking additive’ could we have come about to think of flō. I think all the AM readers out there have this layer-based, layer-material mindset. I’ve lived it for close to 20 years. We ‘see’ things differently. And so, when the founders understood how coatings in the ophthalmic industry were being handled they were like “wait a minute…na…really? But why…? and if…” and there you had it. The first seeds of thought that later became the flō we know today.
I came across flō when there were just two staff members present. But when Dr. Claudio Rottman (CTO & co-Founder) presented me with the idea I was like… “wait a minute…na…really?!” Two AM minds collided, in some scrappy coffee place in the south of Israel. BOOOOOM. And off we went and some 3 years later…we have achieved quite a bit already in fulfilling the vision we started off with. The vision of disrupting the ophthalmic industry through digital printing.
Fabbaloo: flō is developing a method to 3D print lens coatings, but many people don’t understand the complexities of coatings. Can you explain how coatings have been made in the past?
Jaglom: Coatings on lenses today are mainly being handled in what we call a wet process. Lens are placed in vats filled with certain solutions, a layer of coating is subsequently placed, and the lenses are then taken out and cooled. There are other processes that exist other than the wet one described above but we can focus on this one as an example.
Consequently, the process is somewhat costly, time consuming and labor intensive. There are issues of repeatability as well; leaving the lens in the vat over/under the required time set can result in an undesirable outcome of coating placed. Many problems can arise in the current method mainly because the process is analog and the level of control is at the lens level (meaning, you can’t control anything beyond the lens as the entire lens is dipped into the vat).
Enter flō and digitization. With flō, using digital coating allows you to control the material placed down to the level of the pixel, opening an entirely new world of possibilities. We will discuss this later.
Fabbaloo: Optical coatings might seem to some to be a niche product. Is that the case, or not? Exactly how big is this market?
Jaglom: Coatings in the ophthalmic industry are a significant part of the overall market in terms of size (revenue). Put it this way, there isn’t a lens out there in the market that doesn’t have at least one type of coating on it. Whether it’s a protective coating to shield the lens itself, or anti-reflective coatings, or tinting, photochromic, blue light coating and more. All these coatings add up, and the market of ophthalmic coatings is by no means niche.
Fabbaloo: How does flō print coatings? What is the nature of the new process and chemistry involved, without revealing any trade secrets?
Jaglom: flō uses digital printing technology to position materials where desired on the lenses, subsequently coating them. The challenge becomes in developing materials that have both optical clarity (people need to be able to see through their eyewear…) and also functional properties (all these coatings carry functional purposes – blue light for computer screens, hard coat to project the lens, etc.). Our Materials team is working hard to develop these materials and we are partnering with leading players in the industry to ensure a strong product-market fit.
Now enter the engineering challenge. Lenses are non-flat (spheric) by definition and so printing on curved surfaces is all the more complicated. We need to find ways to address the various indexes (power) of the lens and print on them. This is a real complex challenge.
Our technology is no walk in the park. We have a strong and talented team to help ensure we overcome all of the technological challenges we face.
Fabbaloo: What are the advantages of the new process? Is it more efficient? Less expensive?
Jaglom: This is the key question. “People don’t want to buy a quarter-inch drill. They want a quarter-inch hole!” – Theodore Levitt. The technology is brilliant, exciting, avant-garde…but it is basically insignificant if it doesn’t solve a problem. “Sell the hole, not the drill.”
At flō, the value proposition is very clear and convincing. By using digital printing, we can place the dyes of our various coatings exactly where desired. By doing so, we improve functionality of coating (optimal positioning of dyes), as well as reduce costs (less material consumption needed). Because the process is digital, it is also much more repeatable – another advantage. Sustainability plays a huge part as well; our cartridges are sealed and can be used multiple times, so it is much more environmentally friendly. These are all very convincing arguments to our target audience – Ophthalmic laboratories – on why to transition to digital.
Fabbaloo: Can coatings be functionally different than traditional coatings using the flō approach? What new optical features could be envisioned?
Jaglom: Definitely. By applying digital coating technology, functionality can change. Think of tinted coated lenses. These are coatings that have color that serve both as a fashion and blocking of light, allowing a more pleasant experience for the customer. Today the process of coatings of tint lenses is done by dipping the lenses into a vat with a solution in it. The color of the solution corresponds to that of the desired coating. So, the labs are limited to certain colors – each identified by a designated vat.
Matters get more complicated when factoring in seasonality. In hot summers and humid environments results could be different from those in the winter. Skillsets are also very particular in terms of labor; some staff are designed to more complex tinting coating outcomes than others.
Enter digital printing.
Of course, in digital printing, we have none of the above issues. Look at the printing world around you. The same can be done here, giving a lot more possibilities to the customer. The printing process itself is digital, so it is consistent and repeatable, regardless of weather, operator of system and/or other.
It’s a huge advantage and this is just one coating example. There are many more.
Fabbaloo: How will you deploy the technology? Will you sell machines? Offer services? Who would be the target customers?
Jaglom: The model is very much like the model I know from my past at Stratasys. Being one of the first ones to establish the Go-to-Market strategy at Stratasys, I have gained tremendous know-how on how to run consumable-driven-business models. flō will operate in very similar ways. We will sell systems and the consumables that come then after.
Fabbaloo: Has flō received sufficient funding to proceed with its business plan? Are you seeking new investors?
Jaglom: The investors behind flō are the same as those of Stratasys when it started its journey. We are committed to the long term and highly focused in ensuring flō’s success. Our goal is to bring impactful, disruptive technology via digital printing in the ophthalmic industry.
Via flō