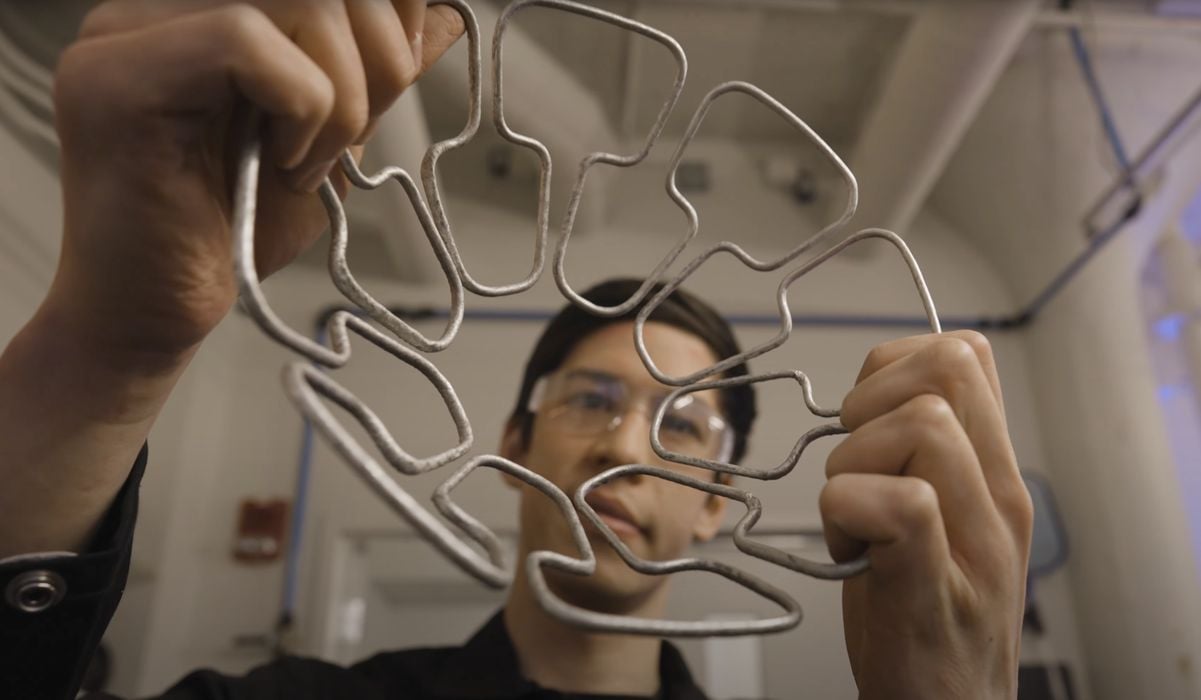
Researchers have developed a practical method for 3D printing liquid metal.
By “liquid metal”, I don’t mean a metal that is in a fluid state at room temperatures; instead I mean a metal, such as aluminum, that’s been heated sufficiently to become completely molten.
Their process, LMP (Liquid Metal Printing), would at first seem similar to WAAM (Wire Arc Additive Manufacturing). WAAM involves feeding a solid welding wire to the toolhead on a robotic arm. There, a powerful electrical arc instantly melts the tip of the wire, which is then deposited on the print.
In LMP the deposition is similar, but the material handling is very different. In fact, the metal is pre-melted and stored in liquid form in a hot reservoir. The printing process involves pumping this fluid to the toolhead for deposition.
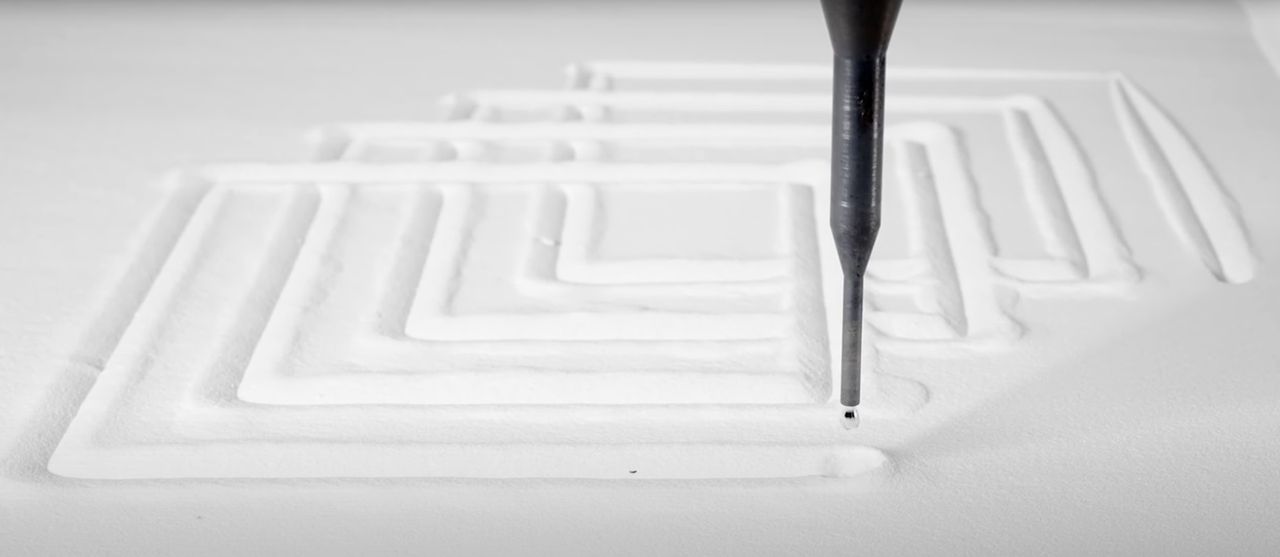
You might ask why the liquid droplets don’t simply fall to the ground when released, and there’s a reason they don’t: the build chamber for LMP is filled with tiny glass beads. The toolhead is inserted into the beads to the correct 3D position, where deposition occurs. The beads prevent the liquid material from flowing further.
The beads keep the material at or near molten temperatures during the print, and this reduces warping and distortion from thermal effects that are often seen in other metal 3D printing processes. Cooling occurs in a more uniform manner, reducing the possibility of cracks.

For their prototype, the researchers chose to use aluminum metal due to its popularity and low melting temperature. It would seem possible to use other materials, but the temperatures would be different.
While LMP seems a bit more complex than other metal 3D printing processes, there are two very significant benefits.
The first is speed. The LMP process is much like “opening a faucet” to allow the material to flow very quickly. This means large metal prints can be produced at speeds up to 10X that of other fast metal processes.
Of course, this is at the cost of resolution. You can see in the images that the surface quality is not great. However, for many applications that’s perfectly fine as function may beat appearance.
It’s also possible to mill the surfaces after printing to obtain perfectly smooth areas or sharp edges.

The second benefit is a bit more subtle. Recall that LMP works with a reservoir of molten aluminum, which is pumped through the toolhead.
It would be entirely possible to design a LMP system that accepts scrap aluminum metal input. One can imagine a hopper where aluminum chunks are tossed in for immediate melting and printing.
This could very rapidly enable a much more direct recycling process for aluminum. Imagine a recycling depot where aluminum is shunted into the LMP system directly, where it is then printed into new parts.
I expect we’ll be hearing a lot more about LMP in the future. For now it’s a research project, but those can be commercialized.
Via MIT and [Research Paper PDF]