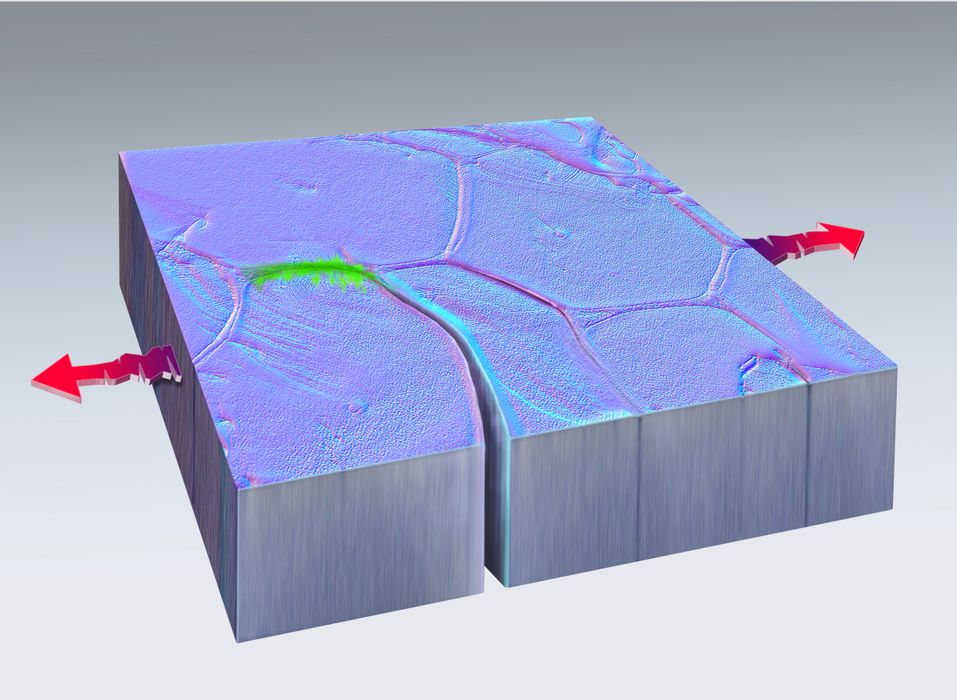
Researchers have discovered a way to provoke metals to automatically heal cracks.
Cracks are the bane of metal part usage. Typically repeated stress will eventually cause metal fatigue and ultimately manifest in cracks. These cracks tend to grow, and can possible become sufficiently large to cause the part to fail.
Cracks occur in almost any metal part, including those produced with 3D print technologies. Considerable effort is taken to prevent cracks from developing during LPBF metal 3D print jobs, and sometimes those efforts succeed. Sometimes they do not.
Even without cracks produced during printing, 3D printed metal parts can similarly fail when used. They can experience metal fatigue just like any other metal parts.
To minimize this effect, metal 3D print jobs usually have carefully tuned print parameters to ensure the microscopic crystalline structure of the metal part is appropriate to provide the necessary strength. If it does not, then expect cracks.
The new discovery is extremely interesting.
The researchers intended on testing a metal part for metal fatigue and crack growth, and their approach for simulating the repeated stress was to use a specialized electron microscope to pull on the ends of a sample at the rate of 200 times per second. If that isn’t repeated stress, I don’t know what is.
To their tremendous surprise, they observed a crack seal itself back up during the process. Apparently the sealed crack “left no trace” of its former existence.
Could this strange effect be somehow leveraged in 3D printing? Sandia materials scientist Brad Boyce explained:
“The extent to which these findings are generalizable will likely become a subject of extensive research. We show this happening in nanocrystalline metals in vacuum. But we don’t know if this can also be induced in conventional metals in air.”
Suppose it can be induced for metals in normal conditions. What might be the implications for 3D printing? I believe there could be several.
One approach would be to develop a post-processing treatment that would generate these high frequency repeated micro-stress conditions to automatically seal up any cracks that appeared during printing.
Another approach would be to modify the LPBF system to somehow induce the micro-stress as each layer (or group of layers) is produced.
It might also be possible to install a device on critical metal parts to automatically seal cracks as the part is used. This could dramatically lengthen the operational lifetime of certain parts.
Or perhaps none of this will happen if the effect cannot be made to work in more natural conditions.
But that’s why we do research: to discover new effects that can be commercialized and provide benefit for everyone.
Via Sandia Labs