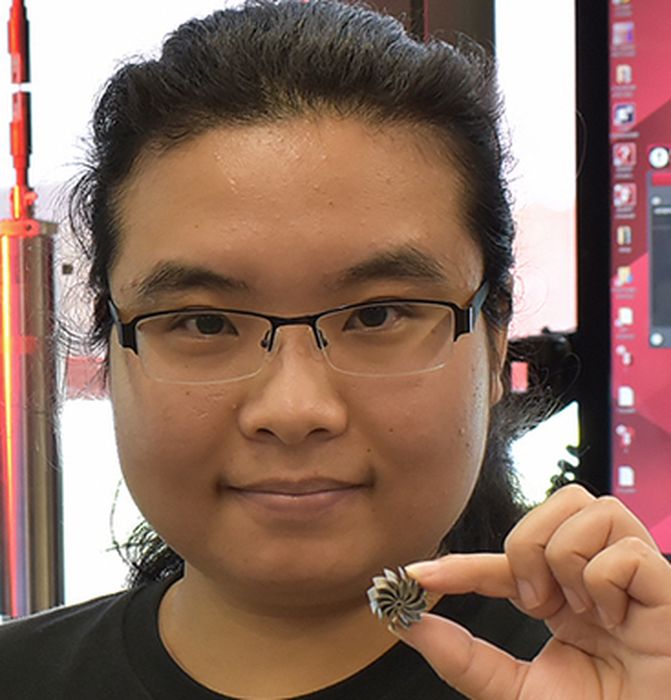
Researchers at the University of Amherst and Georgia Institute of Technology have developed a unique metal alloy that could prove highly useful in additive manufacturing.
While there is tremendous growth in the use of additive manufacturing in the production of end use parts in some industries, there are still many barriers to increased adoption of the technology. One of the most notable barriers is the rather poor selection of materials for use in AM.
When engineers design a part, they match the material for the part against the conditions the part is expected to endure. This usually means there is a small list of “ideal” materials for the part, but in practice that’s not always the case for metal 3D printing.
The powder-based systems that produce metal prints have two significant problems related to material choice: first, the manufacturers have rather short lists of “certified” materials. More importantly, the nature of the machines’ operation means they tend to be loaded with one type of material only. In some cases, a metal 3D printer will NEVER print any material other than the type that was first loaded into it.
This might seem like a strange practice, but in reality there are certification concerns. For example, a small percentage of the population is allergic to nickel metal. Therefore, any 3D printer producing medical implants cannot possibly have any nickel, and thus operators tend to have a “nickel machine” isolated from the rest.
The bottom line here is that part designers have a very hard time moving to AM because the material they need just isn’t available for 3D printing. That’s why I get excited when I see radically new materials being developed: they may eventually make their way into use for production parts, and thus expand the 3D printing ecosystem.
In this case, the researchers explored the use of high entropy alloys in AM environments. High entropy alloys, or “HEA”, are unusual alloys in that they are defined to contain more than four base elements in mostly equal proportions. Normal alloys are usually composed of a main material with some trace elements to slightly alter the properties.
HEAs offer the possibility of new materials with highly unusual properties that are combinations of their base elements. However, their use in AM has been basically nil at this point.
The researchers used one HEA in a LPBF metal 3D printer and discovered some interesting results. Researcher Wen Chen explains:
“You get a very different microstructure that is far-from-equilibrium. This unusual microstructure’s atomic rearrangement gives rise to ultrahigh strength as well as enhanced ductility, which is uncommon, because usually strong materials tend to be brittle. We got almost triple the strength and not only didn’t lose ductility, but actually increased it simultaneously. For many applications, a combination of strength and ductility is key. Our findings are original and exciting for materials science and engineering alike.
The ability to produce strong and ductile HEAs means that these 3D printed materials are more robust in resisting applied deformation, which is important for lightweight structural design for enhanced mechanical efficiency and energy saving.”
This is a profound finding, as it indicates there is a vast space of material solutions awaiting discovery: how many combinations of more than four elements are there, exactly? Quite a few, if you do the arithmetic. Hidden in that list will no doubt be new materials with astonishing properties.
Someday they will be available on your 3D printer.
Via University of Amherst and Nature