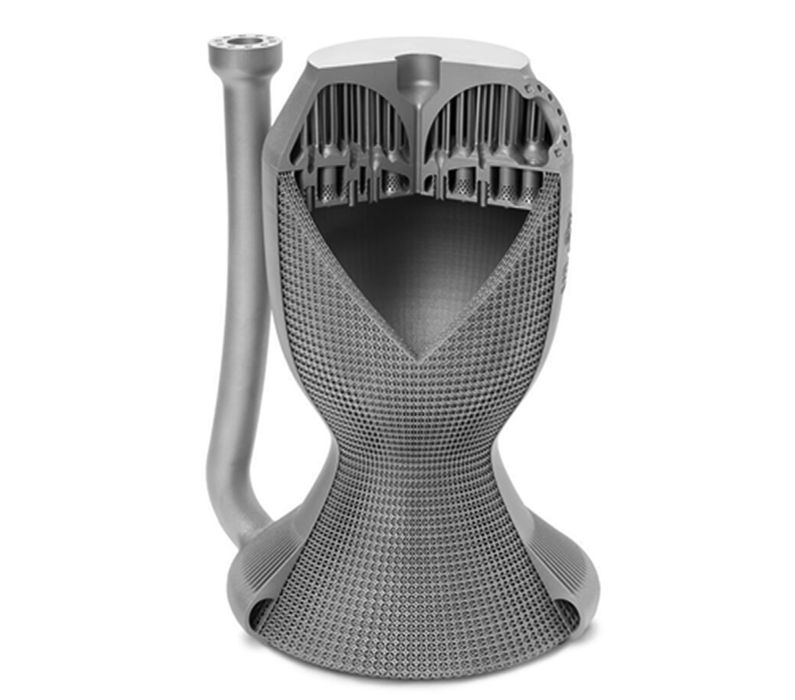
A detailed research report has been published that shows in extreme detail the usage of metal additive manufacturing techniques in the aerospace sector.
That particular sector is perhaps the first where AM has been adopted in a serious and widespread manner, and now has become a standard approach in many companies.
But the journey to get to that point was certainly not direct, nor instant. It took years of experimentation, materials development, software development, machine enhancement and much more effort by many.
The result of all that activity is a collection of knowledge and techniques that are now commonly used in the aerospace sector. This 33-page report provides a comprehensive overview of all that knowledge.
The report’s abstract explains:
“Metal additive manufacturing involves manufacturing techniques that add material to produce metallic components, typically layer by layer. The substantial growth in this technology is partly driven by its opportunity for commercial and performance benefits in the aerospace industry.”
and:
“This paper provides a comprehensive review of metal additive manufacturing in the aerospace industry (from indus- trial/popular as well as technical literature). This provides a current state of the art, while also summa- rizing the primary application scenarios and the associated commercial and technical benefits of additive manufacturing in these applications. Based on these observations, challenges and potential opportunities are highlighted for metal additive manufacturing for each application scenario.”
What does the report cover? Well, as far as I can tell, “everything”. A quick read through seems to highlight virtually every key aspect of metal AM as it pertains to the aerospace sector. That includes not only the 3D printing processes involved, but also materials, software, post processing, and examples of successful approaches and parts.
But most importantly, it covers the business cases related to using metal AM in aerospace. They include:
- Function performance
- Lead time reduction
- Lightweighting
- Cost management
- Certification
- Low volume production & sustainment
- Part complexity
There are plenty of charts to explain feasibility concepts, such as this one:
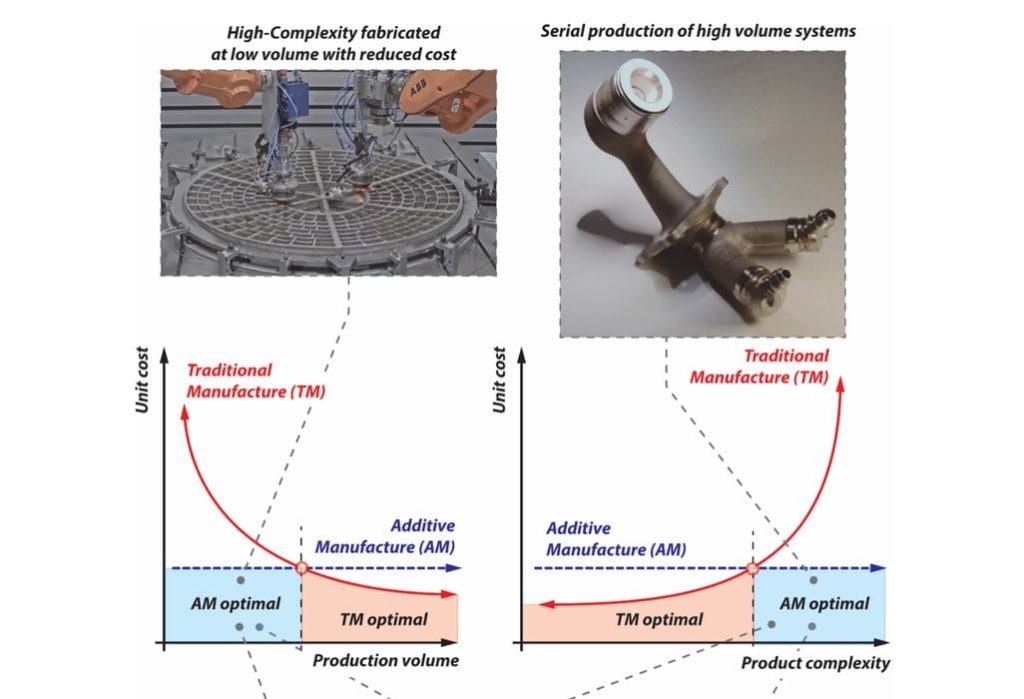
I can’t tell you the detail to which all of these concepts are explained, through both logic and example.
The report continues on to portray the key aerospace parts that have benefited from AM, beginning with components for the famous GE LEAP engine and continuing on with many others that have subsequently emerged.
To someone already using AM extensively in aerospace, the report will probably be a confirmation of existing practices and perhaps a hint at some expanded activity that could be investigated.
To someone in aerospace but not yet using AM, the report will be a revelation, exploring approaches unknown. It could also be a shock, as the reader would then understand the activities of their competitors.
Finally, to someone not in aerospace, this report is also essential. It shows, in very plain language — there is no mathematics or chemistry in the document — the way in which aerospace fully adopted AM technologies.
Knowing that, someone in another industry could then more precisely reflect on their own activities to identify paths towards use of AM, metal or otherwise. Many of the business cases and part approaches could be similar or have analogs in parallel industries.
Aerospace has largely taken the heavy lifting of figuring how to use AM in business, both practically and financially. Let’s leverage that knowledge in other areas.
Via Science Direct