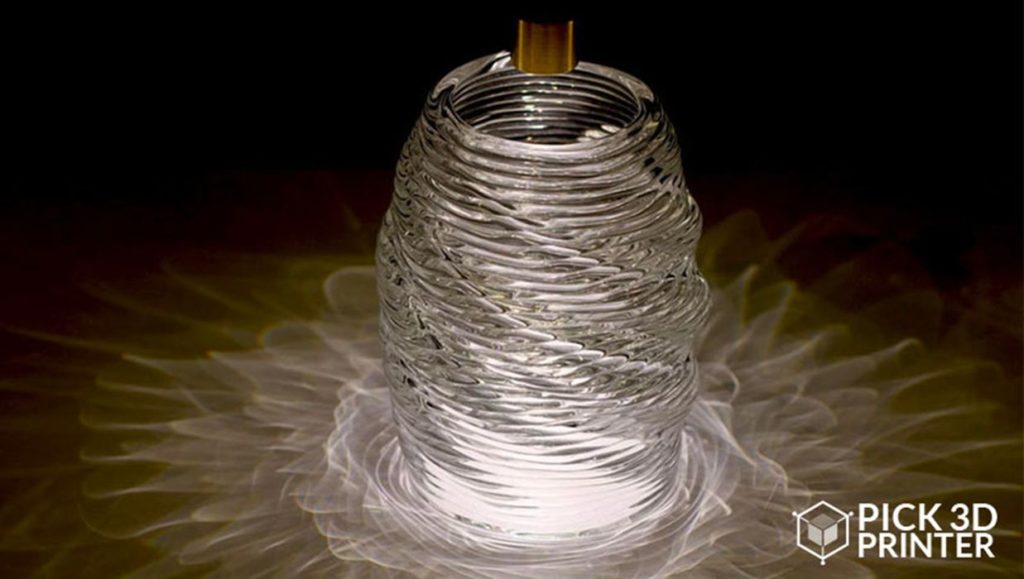
Charles R. Goulding and Mindy Zhu look at various projects attempting to create 3D printed glass objects.
Glass has been one of the oldest and most versatile materials used for creation but has always been difficult to 3D print. This is due to the chemical and physical properties of glass; the material is very hard to utilize with additive manufacturing, and the high temperatures usually required prevent easy solutions. Back in 2019, researchers at MIT developed an additive manufacturing platform for architectural-scale 3D printed glass, the G3DP2. Since this development the 3D glass manufacturing industry has continued to grow and advance.
3D Printed Glass [Source: Pick 3D Printer]
Univerre and ETH Zurich
Univerre is a Swiss family-run international glass bottle creator and distributor. They partnered with ETH Zurich (Swiss public research university) to reinvent the idea of 3D printed glass. As the glass industry grows, more consumers are asking for very intricate pieces that can be near impossible to create with handmade glassmakers. Due to the demand for higher levels of details and faster output, the team turned to the possibility of 3D printed glass.
ETH Zurich has research specializing in complex materials, glass being one of the materials they work with. By combining the use of a special resin and digital light processing (DLP) technology, the team hopes to be able to create the complex intricate details sought after by the glass industry. The idea of DLP technology is to have resin cure and solidify under a light source. By combining glass with the special resin, the team hopes to be able to design a glass product layer by layer. Each layer would be cured under a UV light to solidify. By separating the layers and curing them individually, the team hopes to be able to create very intricate designs.
The special resin used is one developed by the university. The resin contains a type of plastic along with organic molecules. By adding glass precursors bonds to the organic molecules, the formulation creates a 3D printed glass structure. By using DLP, not only are they able to cure each layer individually, the UV light intensity can also be adjusted to weaken or strengthen the pores to create different designs.
Glassomer
In 2018, a German company, Glassomer, started to design their own special resin called Glassomer Resin. They’ve now developed multiple glass resins for UV curing, 3D printing, and specific liquids for embedding thin polymeric templates. The company’s goal is to make the product 100% transparent and clear like real glass. Although the resin will be 60% glass and 40% other compounds, the other compounds cause the glass to have a honey-like tinted color. The company continues to develop its product to get closer to real glass. The special resin allows for high levels of intricacy allowing for 3D printed glass to be used to manufacture microfluidic chemical reactors, compact optics, medical technologies, automotive and jewelry.
Luxexcel
Luxexcel is an international company formed in 2009 to develop and distribute 3D printed prescription lenses. COVID-19 has fast-tracked the trend of online eyewear. Luxexcel’s technology builds the lenses droplet by droplet from a liquid material The small droplets combine to build the lens shape with a 3D printer. The 3D printer jets the small droplets to exact locations to create smooth and clear glass-like lenses. The droplets are then cured and solidified with UV lights. On September 8th, 2021, Optiswiss and Luxexcel announced a partnership to design 3D printed lenses for regular eyewear and smart glasses.
The Research & Development Tax Credit
The now permanent Research and Development (R&D) Tax Credit is available for companies developing new or improved products, processes and/or software.
3D printing can help boost a company’s R&D Tax Credits. Wages for technical employees creating, testing and revising 3D printed prototypes can be included as a percentage of eligible time spent for the R&D Tax Credit. Similarly, when used as a method of improving a process, time spent integrating 3D printing hardware and software counts as an eligible activity. Lastly, when used for modeling and preproduction, the costs of filaments consumed during the development process may also be recovered.
Whether it is used for creating and testing prototypes or for final production, 3D printing is a great indicator that R&D Credit eligible activities are taking place. Companies implementing this technology at any point should consider taking advantage of R&D Tax Credits.
Conclusion
Although 3D printed glass has been challenging in the past due to the chemical and physical properties of glass, it is a capability that innovation is slowly achieving. As the industry continues to grow, 3D printed glass is expected to become more transparent and glass-like.