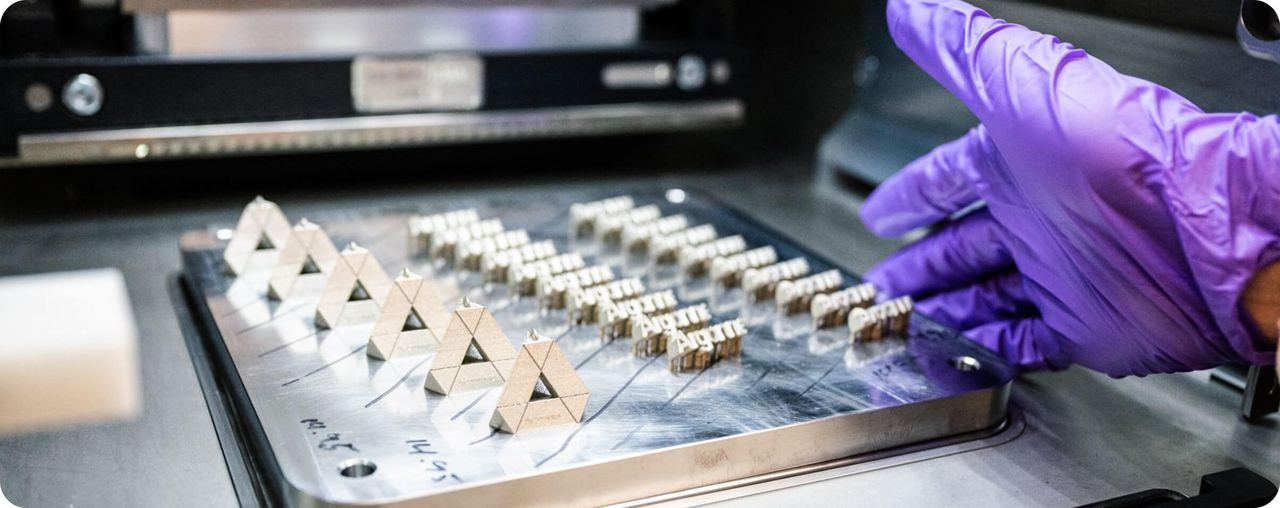
Phase3D has developed a sophisticated real-time quality control system for powder-based 3D printers they call “Fringe”.
The Chicago-based startup, which started only in 2020, is focusing on quality issues often found in production 3D printers. Typically production devices are large and intended to be operated 24/7 to produce as much output as possible. This is driven by financial matters: get as much return as possible from the large investment required for the device.
This means that it hurts badly if the device is down, or when prints fail. Most print failures are detected only after the job completes, and that wastes both costly materials and machine time. The time used to produce the failed print didn’t generate any revenue!
Phase3D’s approach is to attach an add-on to powder-based systems that can provide a measure of real time quality control. They call this “real time inspection”.
Their approach is to perform continual 3D scans of the print surface as the job proceeds. They use a structured light approach to determine height maps of the scene inside the build chamber, layer by layer.
These are compared to what should be occurring based on the 3D model’s geometry and the machine’s typical behavior. If deviations are detected, then alerts can trigger the operator to pause the job.
This short-circuits the failure cycle and prevents loss of additional pricey materials, and more importantly, can get the part produced properly in a shorter time period.
Engineers can investigate the cause of the deviation and make appropriate adjustments, which could be part orientation, temperatures, support structures, laser power or print speeds. The Phase3D system enables “informed decision making”.
The system provides 3D visualizations of print progress so that the operator can “see” what’s going wrong in real time. (Or see that it’s “right”). They also provide specific measurable results in microns that can be used for detailed analysis and comparison from job to job.
What’s interesting is that this system works on almost any powder-based system, be they metal or polymer. That’s because the PBF process is mostly the same, aside from materials and temperatures.
Currently Phase3D has certified their equipment for use on EOS, GE M2, ExOne, Desktop Metal and DMG MORI powder-based equipment. They are “in progress” for other systems, and I’m certain they’d be very interested to hear from customers interested in other machine implementations.
Recently Phase3D announced a deal with Materialise to integrate Fringe capabilities directly into that company’s Process Control software. This means that the many companies using Materialise solutions could very easily gain access to Phase3D’s real time inspection services. This arrangement could be a big deal for Phase3D, bringing in customers they may otherwise have had connection challenges.
Finally, Phase3D just announced a new contract with the US Air Force Research Lab to develop a similar real time inspection system for cold spray additive manufacturing systems. This is somewhat different than the flat PBF systems they’ve been using, but scanning technology should be able to succeed in this environment as well. Phase3D explains:
“Our flagship Fringe in-situ inspection system will be adapted to monitor CSAM deposits to ensure uniform material deposition. For advanced manufacturing to increase adoption and use cases, more repeatable, quantifiable, and objective data needs to be gathered for every step of the workflow. This contract will demonstrate a full solution of in-situ monitoring for CSAM which will help a technology with a lot of potential grow.”
Via Phase3D (Now Additive Monitoring)