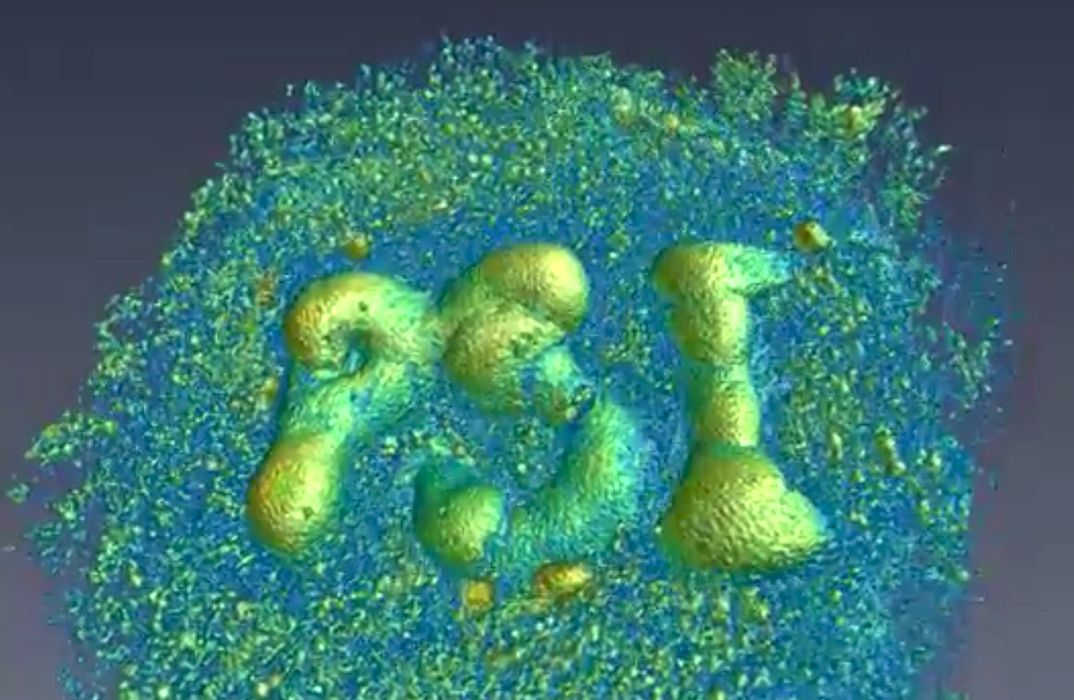
A fascinating new research paper explores the complexities of 3D printing ceramic materials using the LPBF process.
LPBF, or Laser Powder Bed Fusion, is a popular process used by many companies to produce metal, polymer and ceramic objects. Because of the nature of the materials, the prints are often end-use parts rather than just prototypes. This usually means that they must be of the highest quality possible.
Quality isn’t just surface quality. More important is the inner strength of the printed material, because the parts are typically used in mechanical situations. This strength is derived from how the powder is fused together when exposed to the laser.
Over many years it’s been realized that the microstructure of parts produced with the LPBF process can vary considerably depending on the laser power, speed, chamber temperature, temperature gradients, humidity, oxygen levels and many more factors.
This confusing set of parameters makes much work for operators that have to devise print plans that achieve the intended part results. It also makes LPBF one of the more expensive 3D printing processes on the market today.
Because of this there has been much study of the “meltpool”, which is a temporary region where the laser is currently operating on the powder bed surface. This is where the material softens and flows together, and that’s how the microstructures of the finished part are generated.
The researchers were concerned with 3D printing ceramics with LPBF, as there are often issues with the resulting parts. They explain:
“Laser-based Powder Bed Fusion (LPBF) of oxide ceramics enables fabrication of objects with complex three-dimensional shapes. However, mechanical properties of dense LPBF-manufactured ceramics are poor due to large amount of structural defects.”
To investigate the source of the defects, they designed a method to observe the meltpool in action using “operando tomographic microscopy”. As you probably don’t know what that means, let me explain.
Tomographic microscopy differs from normal X-ray views because it is in 3D. Typical X-rays pass through, so meltpool movements are only visible if they cross the plane of the beam, and cracks can be invisible if they aren’t at the correct angle. Tomography views from multiple angles and can create a true 3D view of a subject.
“Operando” simply means “working”. In other words, the tomography is done while the subject (in this case the meltpool) is active. They are literally observing the meltpool activities in real time in three dimensions.
This allowed the researchers to perform a series of experiments where print parameters were varied, and they could observe how flaws were generated. They used a standard LPBF set up to print magnetite-modified alumina.
What did they find? From the paper’s abstract, they found:
“Increasing laser power results in significant increase of the melt pool width, but not its depth and no melt pool depression is observed. Forces due to the recoil pressure are not seen to significantly influence the melt pool dynamics. Increasing power allows to avoid fusion porosity but enhances formation of spherical porosity that is formed by either reaching boiling point of liquid alumina, or by introducing gas bubbles by injection of hollow powder particles into the liquid.”
LPBF is an incredibly complex process that takes place at a microscopic level. I believe more investigations of this type could greatly assist those trying to squeeze out the most performance from their LPBF equipment.