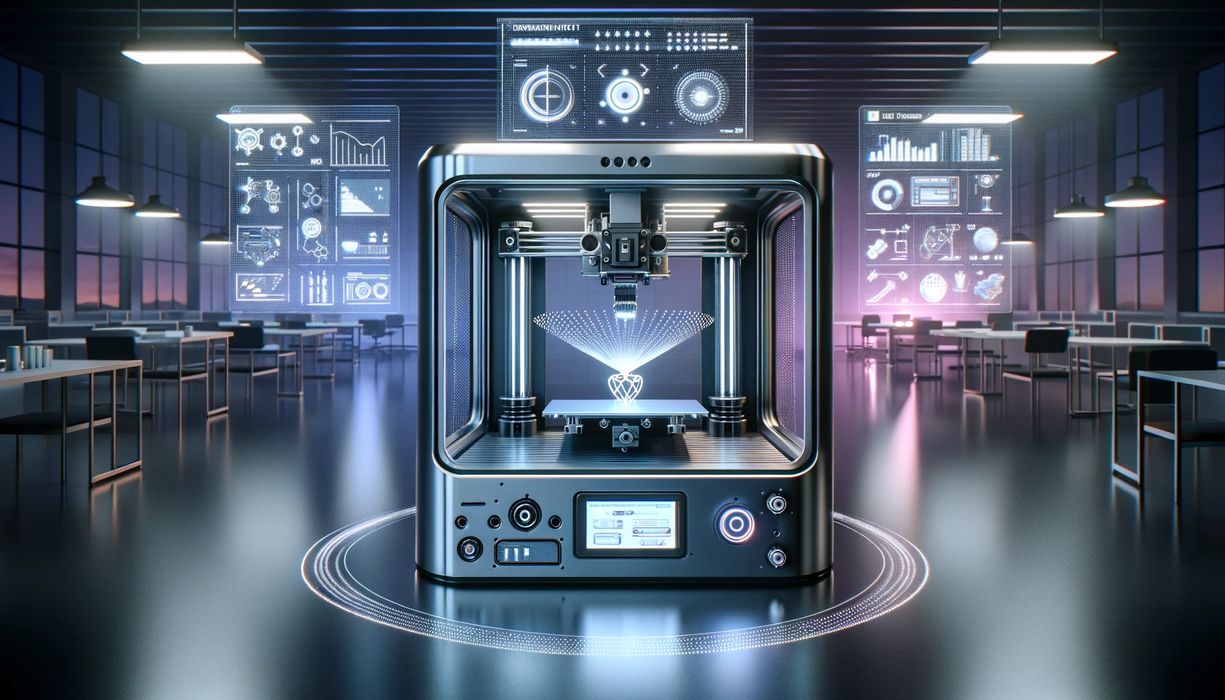
I’ve been thinking about a possible innovation for desktop 3D printers that might change print quality and material management forever.
Looking back at the first 3D printer I used, the venerable MakerBot CupCake, it’s now quite appealing how awful that machine is relative to today’s sleek, sophisticated machines. The CupCake was lucky to have end stops on its motion system, and that might have been one of the “features” at the time.
Over succeeding years there have been many developments that took the technology up a notch, year after year. Some of those innovations, which now might seem routine, include:
- Standard heater blocks
- LCD control panels
- PEI print surface
- Magnetically detachable print plates
- Dual geared extruders
- Color touchscreens
- Filament out sensors
- Power loss protection
- Linear rails
- Vibration compensation
- Dynamic flow management
And many more. As time passes, these technologies have (or will) make their way into the set of default features one would expect to find on a desktop 3D printer. That’s a good thing, as today’s devices are unimaginably more reliable and high quality than devices from years ago. That transformation happened in steps, and took many years.
But what is the next step?
I was thinking it might have something to do with temperature. Here’s the problem: every FFF 3D printer has somewhat different thermal characteristics. That’s because the hot ends, extruders and materials are different.
It means that a given filament might require a different temperature setting on a different machine. That’s because the geometry and thermal properties of hot ends differs. One machine might best use a PLA filament at 208C, while another it’s 185C.
How can you know the correct temperature? To compensate for these differences, we’ve come up with print profiles. This means that one must generate a print profile for each possible machine-material pair. That’s a lot of work, and while some companies attempt to do this, it’s not possible to “complete”. That’s because there are new machine models and materials coming out all the time.
There should be new machines coming out all the time. We need them to achieve technological progress. New hot end designs are always required, and that means even more profiles are required.
Looking forward, in, say, 2035, will we have millions of print profiles? How will we keep track of all this?
To me the root of this issue is simply that the FFF machines, as designed today, are incapable of knowing the actual temperature of the extruded material.
The temperature that they know is actually the temperature of the heater block, where the thermistor measures the temperature. That’s only a proxy for the real extruded material temperature. That’s why some hot ends might require a slightly different temperature setting for a given material.
Let’s imagine how this could be solved. What if there was a way for each FFF 3D printer to measure the actual, real time temperature of extruded material?
Perhaps this is done with some kind of laser or infrared sensor aimed at the tip of the nozzle, or a smart thermo sensor pasted on the tip, or some other means unimaginable today.
If that feature was available, then a machine, with appropriate software, might be able to dynamically determine the correct temperature for any given material.
If the print speed / flow increases during the job, this feature could help the software raise the hot end temperature to compensate, for example.
It would mean that you don’t have to use thermal data in print profiles anymore; the systems would simply figure it out when required. They’d do so continuously during each print job, and that would certainly lead to higher quality prints.
I’ve never heard of anyone working on this issue, but perhaps it’s worth exploration. If successful, such a feature could significantly change the way FFF 3D printers operate and also how filament is distributed and used.
And I’d add it to the list of major steps forward above.