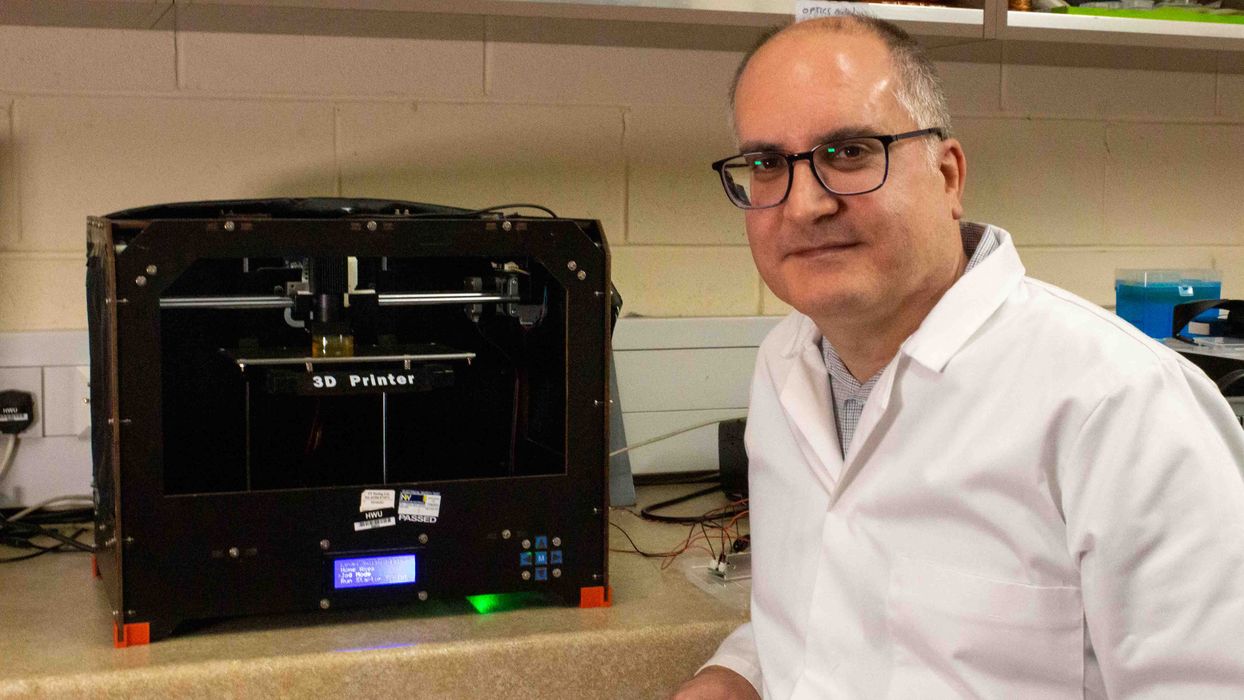
Researchers have developed an unusual approach for enabling multi-material resin 3D printing.
Resin 3D printing is the oldest 3D printing process, and since developed it has not significantly changed: a single resin in a vat is selectively polymerized, layer by layer. The methods of polymerization and mechanical structures have changed, but that’s how all of these resin 3D printers still operate.
Now, researchers at Heriot-Watt have developed a new form of resin 3D printing that involves use of near-infrared light (980nm). This is vastly different from current 385nm or 405nm systems.
Why use a different wavelength? There are a couple of advantages, but the most important one is that NIR is able to penetrate the resin much more deeply than UV light. UV systems typically penetrate to about 0.1mm, the thickness of one layer. That’s why SLA and MSLA systems print layer by layer: they can’t reach any further.
The new system is able to penetrate resins up to an astonishing 58mm. This opens up a number of intriguing possibilities for alternate forms of 3D printing because you don’t necessarily have to print layer by layer.
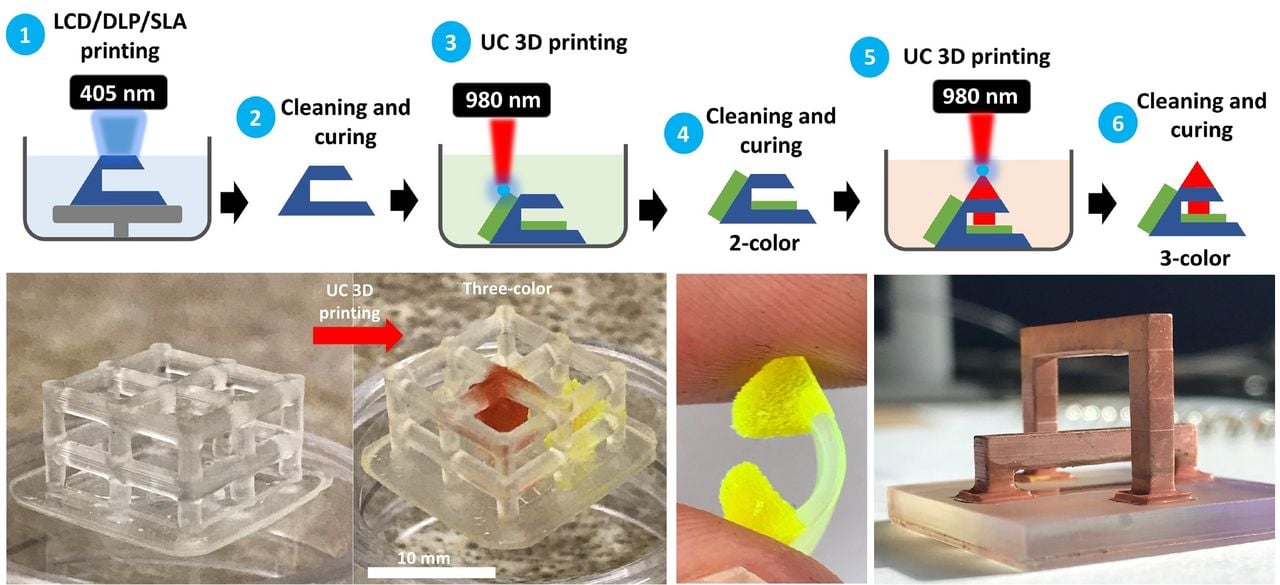
Note that this approach is very different from volumetric 3D printing, which uses projections into a rotating resin tank to build objects all at once. That approach is quite complex, whereas the NIR approach could yield 3D printers that cost only about US$500, according to the paper’s authors.
One concept proposed by the authors is to 3D print objects inside of previously 3D printed objects. This would entail placing the first object in a second resin vat and printing from there.
Another concept would be to print part of the object in an initial resin, then washing off loose resin, and printing the remainder of the object in a second resin material. This could be repeated in several steps, leading to a multi-material resin 3D print.
The team has also developed a resin that can be used for selective copper plating. The method involves printing a multi-material object with one material being a specific electroplating resin. Later, when the object is immersed in an electroplating system the copper molecules are attracted only to the portions made from the special resin.
This approach could, for example, be used to create electrical circuits in a 3D printed object through electroplating. However, it’s likely that the conductive elements must be on the surface, otherwise the electroplating solution could not reach them if deeply embedded.
Another key advantage of the NIR technique is that it doesn’t require an expensive laser system as might some other 3D printing processes. This allows the NIR 3D printer designs to be manufactured at lower cost.
Clearly the NIR approach is unique and offers some intriguing advantages. However, there are several questions to be answered.
One of the big issues with current resin systems is that parts are typically quite brittle and cannot often be used in production applications where mechanical stress occurs. Does the NIR resin produce useful parts? If not, then the NIR approach might not be as successful.
Another question revolves around the method of performing multiple material prints. How difficult is it to wash partial prints and reuse them in subsequent material print jobs? How do you keep the print aligned between steps? Do secondary materials adhere to prior materials?
These questions certainly don’t disqualify the NIR 3D printing approach, but they do suggest there is a lot more work required on this concept before commercialization could proceed.
Via Science Direct