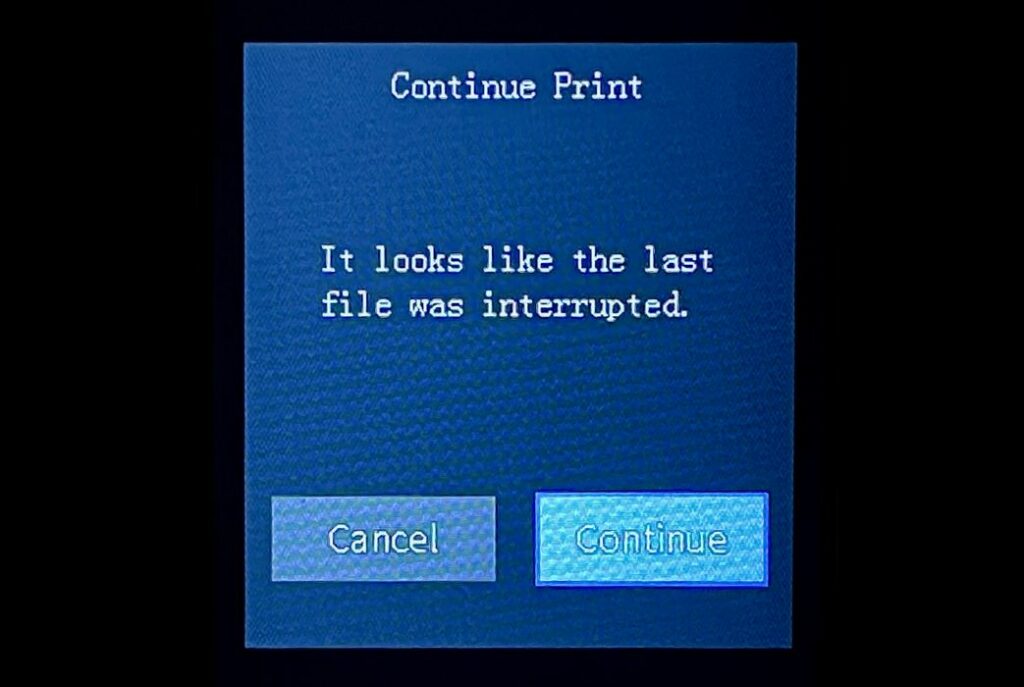
I’m beginning to have my doubts about the benefit of “power fail recovery” for FFF 3D printers.
This is an increasingly common feature, now found on even the most inexpensive 3D printers. The feature attempts to eliminate the frustration of having a huge print job fail towards the end of the work due to a power failure. That entire job must be tossed out because the 3D printer can’t resume after power is restored.
The power fail feature will instead cause the 3D printer to “remember” where it was when the power failed, and then resume the print when power is restored. Theoretically you get your print completed and no frustration occurs.
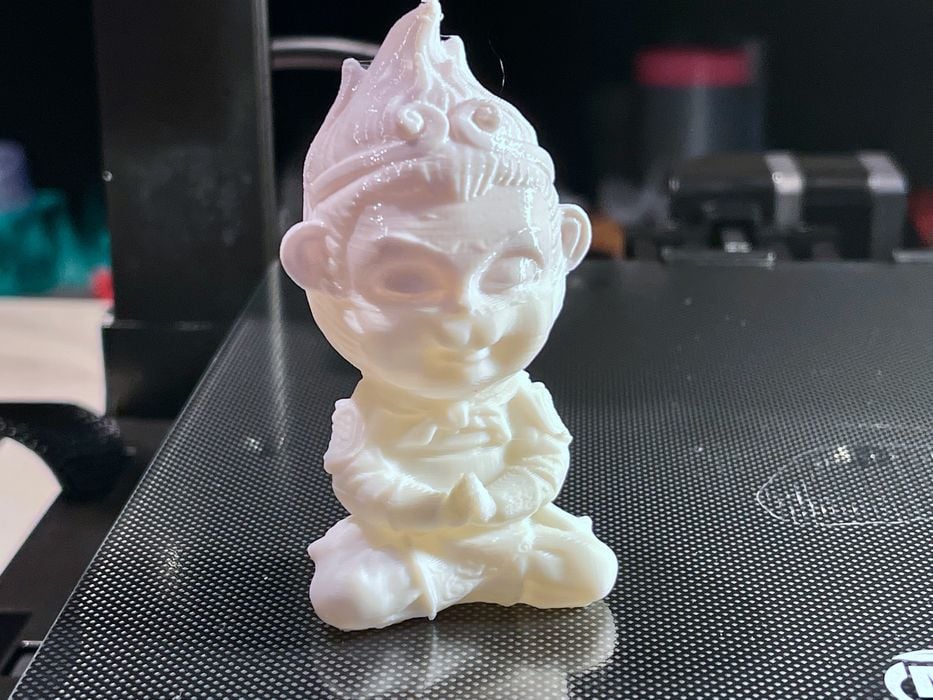
But there are several problems with the approach, most of which are not observed until the power fail scenario actually happens.
3D Printer Power Failure Extra Melting
The most obvious and visible problem is that when power fails, the machine stops moving. The toolhead and nozzle remain where they were. Unfortunately, the nozzle is still at high extrusion temperature, and its proximity to extruded structures will often melt them for a short while until cooled.
Basically, the power fail can cause a “blister” to be placed in the print where this melting occurred. If you’re lucky the melted spot is inside the print, corrupting the infill only. But sometimes it’s on the surface. For some prints this might not matter, but for others it does, and matters very much.
The only solution to this dilemma I can see is to somehow store enough power in the machine itself to slightly raise the Z-axis when the power drops. This could put enough distance between the nozzle and the print to avoid melting.
3D Printer Power Fail Priming Problem
The second problem deals with priming, and let me explain.
The print is to resume after power is restored. However, we know that as a result of the leftover heat, it’s likely that a quantity of material has dripped out of the nozzle — probably onto the print making a slight mess. This leaves the nozzle “empty” and it should be refilled before printing resumes. This is why most 3D printers have a “prime line” to ensure the nozzle is full of material before printing.
Some power fail resume processes involve moving the toolhead to the side and priming a length of filament. Because there is a print in place on the bed, the printer cannot lower itself and put that prime line on the bed. It has to “air print” the prime line. In other words, the nozzle now has a long stringy thread hanging from it.
Guess where that material goes? That’s right, it’s dropped on the print, spoiling the surface quality again.
To overcome this problem, some power fail recovery processes don’t move to the side at all, and just resume printing in the exact position they stopped. That avoids the above problem, but introduces another: there is a gap where the leaked material would have been.
One possible solution would be to always move the toolhead to the side and prime it, but then move it to a high-mounted brush to knock off the priming extrusion. There are very few FFF 3D printers with brushes.
3D Printer Power Fail: Where Did It Fail?
Another issue is determining exactly where the print should be resumed.
One approach is to simply re-print the entire layer that was underway when power failed. You’ll be sure to get all of it, but then there will be over extrusions in parts that had already been done.
Another approach is to resume after the last successful GCODE instruction. That would provide a “finer resolution” of the failure point, but some GCODE instructions produce very long extrusions: “start extruder and move across the bed”. In such cases there is no way to know where on that instruction the power failed. Again, you would get some over extrusions. However, this approach could be better than the other options.
I believe the best approach should be something like this:
- Power fail is detected
- Printer continues to complete the current layer based on battery power
- Printer moves the toolhead far away from the print to avoid melting
- Printer shuts down
- When power is restored, the extruder heats up
- Extruder primes some material
- Material is brushed away
- Print resumes on the layer after the last successful layer.
To implement such a solution would require not only a brush and some new software, but also a battery system capable of powering the machine for multiple seconds through that final layer. That would add notable cost to the 3D printer, which users would have to pay for. Essentially it would be similar to a standard UPS system used with PCs.
Would such a system be worth it? I’m not sure, as the cost of reprinting is relatively inexpensive — just material and time. On the other hand, if a site is experiencing frequent power outages, it may be a desirable feature.
I suspect that 3D printer manufacturers aren’t going to re-work their power failure processes any time soon because few solutions are good and most buyers don’t want to spend any more money on them.