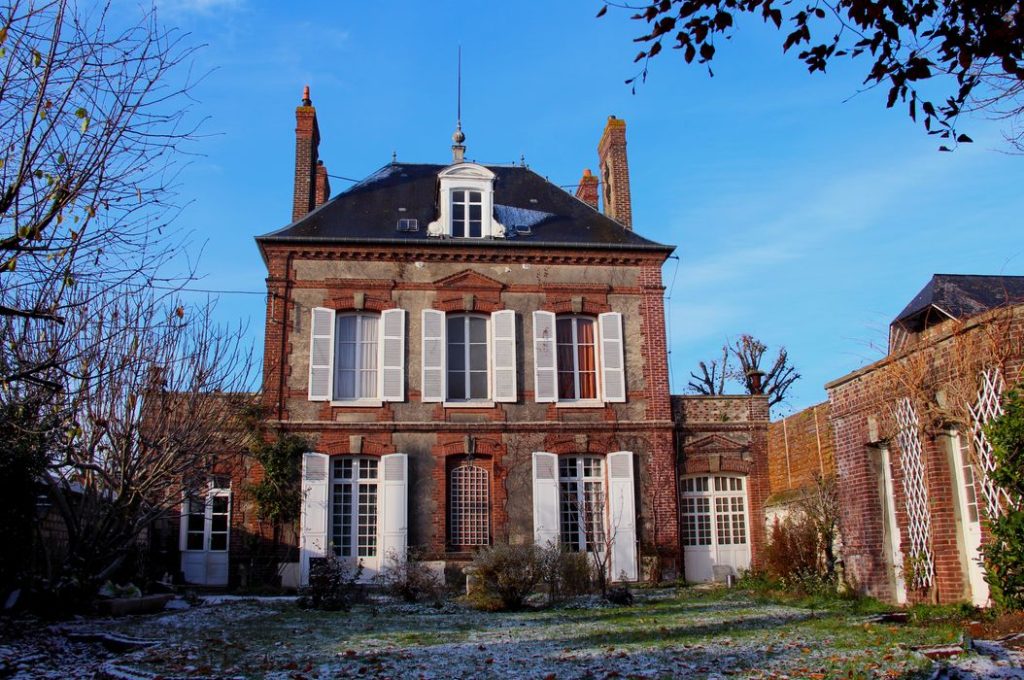
This week’s question is all about how to 3D print an enormous metal house ornament.
While Fabbaloo is a news agency, we frequently are contacted with requests to print things. Sometimes they are quite interesting to analyze, and that was the case with a query from Fabbaloo reader Benjamin from France, who asked:
“I am a private owner of an old house. On the roof there is an old zinc ornament. Would you be able to reproduce it?”
Benjamin provided images of the structure, which is quite striking on the top of the house as you can see in the images.
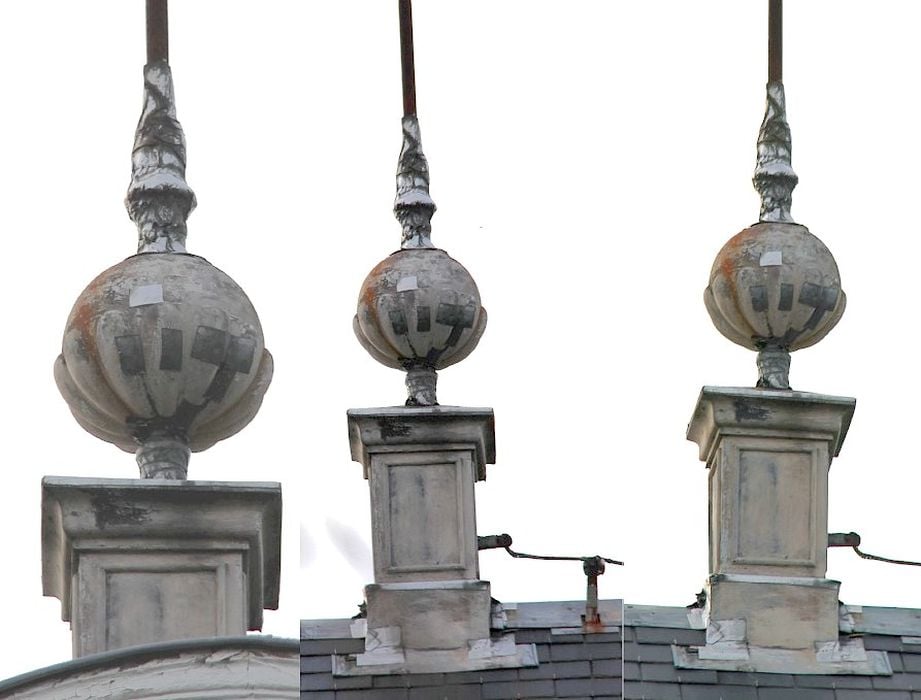
Note that in this detail image of the base you can see some repairs have been done over the years, and it’s likely this tower does indeed require replacement.
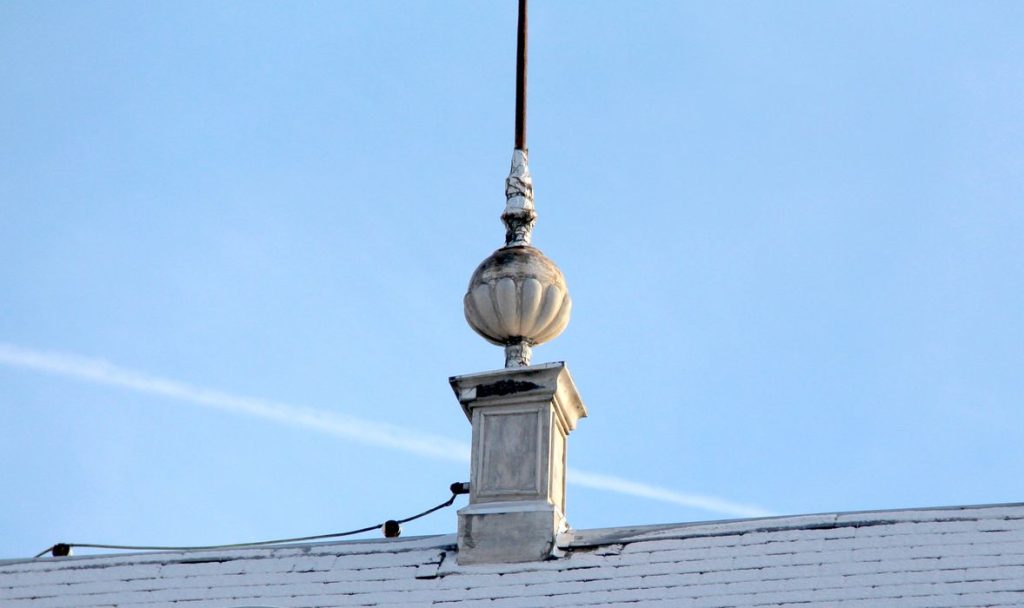
Also provided was dimensions and a proposed sectioning of the tower for production:
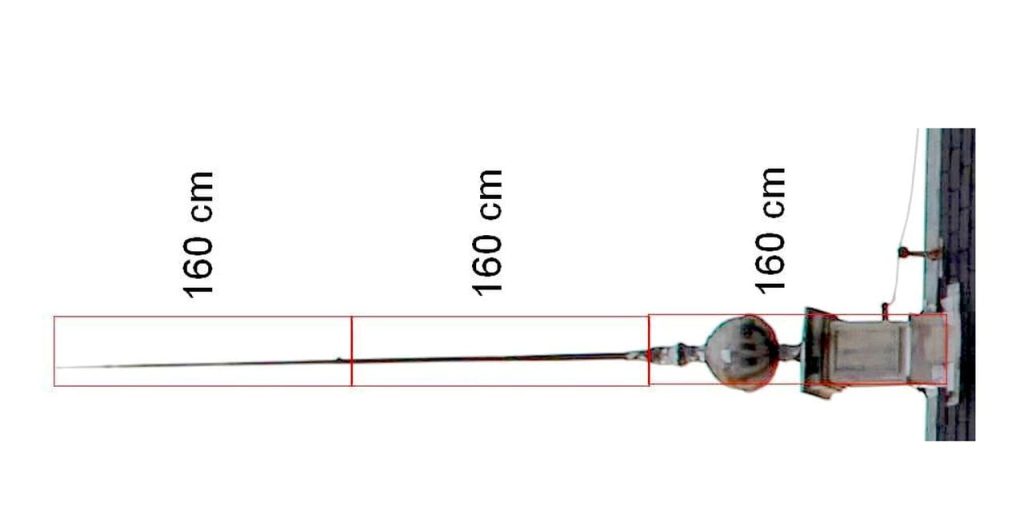
Evidently this tower is 4.8m tall, or about 16ft tall. That’s big, especially for 3D printing. Also enormous would be the project to replace this item.
The traditional approach to replacing this tower would likely involve a craftsman forging individual metal parts and welding them together to form the complete tower. This could be quite lengthy and expensive.
But could this be done with 3D printing? Let’s take a look.
How to 3D Print an Enormous Metal House Ornament
To 3D print an object, the first thing required is a proper 3D model of the object. As it is very old, there certainly is no CAD model for this tower, and it would have to be created from scratch.
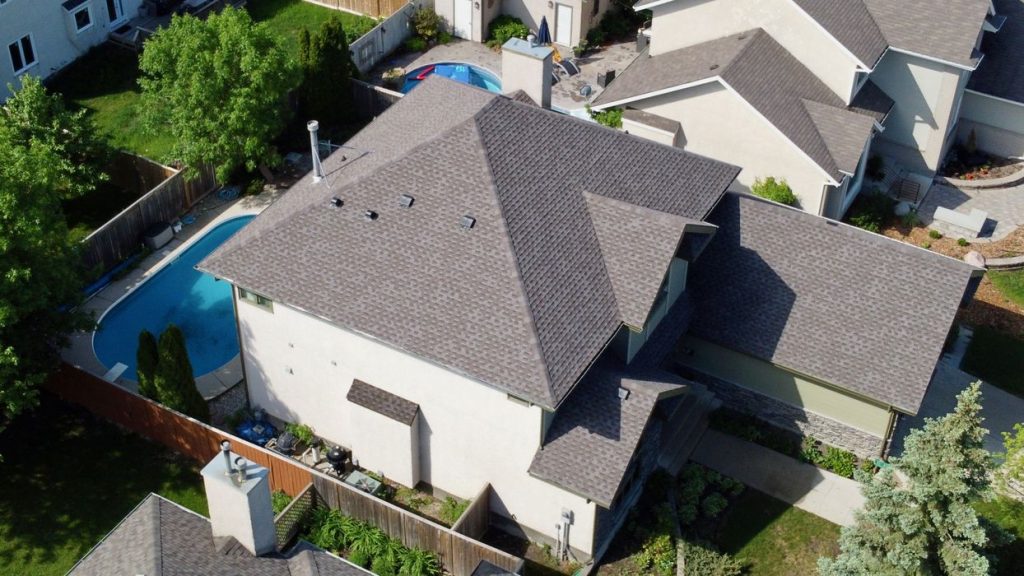
This would best be done using a 3D scan of the tower. For this the best approach would be to use a drone to slowly circle the tower, taking a series of images from each angle. Then, a photogrammetry application could transform the images into a 3D model of the structure.
But that would not necessarily be 3D printable; the scan results would have to be converted into a CAD model by a skilled CAD software engineer. But certainly that’s possible to do.
The next step would be to decide how to produce a print from the new design, and there are a couple of choices.
3D Printing a Metal Tower?
The first thought would be to simply 3D print it on a metal 3D printer. However, there are a number of concerns.
First, it’s the size. There are few 3D printers that can build a 5m object, especially with the surface quality required. The largest we’ve heard of has been commissioned by a US Army project, launched last year. The intention was to create a metal 3D printer that could print objects up to 9 x 6 x 4 m, which would do the job.
However, this technology would produce poor surface quality and thus require machining after printing (or during, if they have implemented that feature). The problem is that this printer is not available to the public — I don’t even know if it’s been built yet.
There’s also the question of cost: 3D printing such a large metal object could be quite expensive.
Another approach would be to segment the object into parts, print them separately and then assemble them. Benjamin has suggested segments of 160cm, which honestly is too large for most of the common metal 3D printers one would have access to via print service bureaus.
Most of these machines would have build volumes with a maximum dimension of 400-600mm. This would suggest the printing would require perhaps seven separate metal print jobs.
But that isn’t the issue. It would be cost: metal powder for 3D printing is extraordinarily expensive, typically at least US$100/kg — and this project would require many, many kgs. The cost of the print job (including setup by specialized engineers, printing, post processing) would be even more expensive.
Finally, there’s the material: Zinc. This is not a common metal 3D print material, and I could find only one service that offered it: PROTIQ. I’m not sure of the build volume of their equipment, but it is likely similar to the above in both size and cost.
I really don’t think this could be feasibly produced on a metal 3D printer at a reasonable cost.
Alternate Additive Manufacturing Solutions
There is another approach, however, that might be more economical.
Having developed the 3D model, it would also be possible to 3D print the tower sections in polymer. I’m thinking that some of the large format 3D printers could produce these parts in up to 1m sections, meaning only five or six would be required. The material used could be carbon-fiber reinforced nylon, which would be quite strong and durable, especially if a steel rod went up the middle.
But hold on, didn’t we want a zinc tower?
It would be possible to electroplate the polymer parts after printing with zinc. Plastic 3D prints have been electroplated for many years.
However, all the electroplating experiments I’ve seen involve small parts. These parts are large, so it would likely require an industrial electroplating service to do the job.
Executing this approach would still be pretty steep in terms of cost. Services to select, purchase — and coordinate — would include:
- 3D scanning the tower
- Developing the CAD model and segmenting it
- Printing the CAD model segments in carbon fiber material
- Electroplating the segments
- Assembling the segments
- Installing the tower
This would not be inexpensive, as I suspect each step could cost thousands. However, it may be worth investigating as it just might be financially feasible for Benjamin, as compared to the cost of conventional approaches.
The result, after assembly, would be a rather lightweight, strong and durable tower that could replace the aging zinc tower.
That’s my opinion on this unusual enquiry. Would any readers like to propose an alternate additive manufacturing solution?