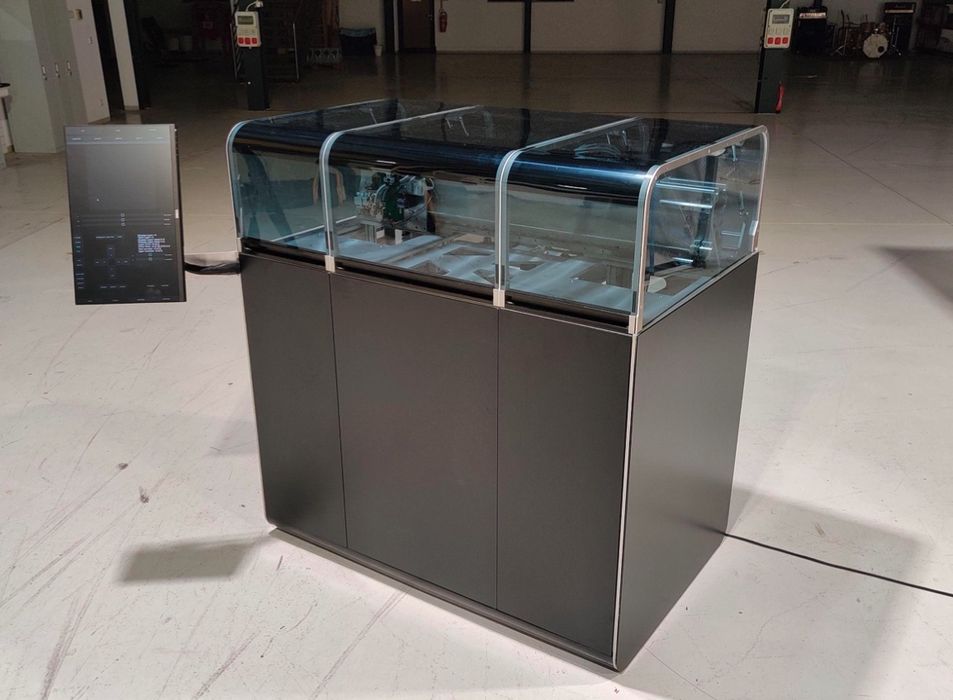
Quantica announced the T1 Pro 3D printer, which uses a new technology to enable printing of materials previously impossible to achieve.
The Berlin-based startup is not known at all because they’ve been in stealth mode for some time. Since 2017 they’ve been developing a very unique form of resin 3D printing that has so many advantages I can’t see a future without them being a big part.
Today they announced their first product, the T1 Pro 3D printer. The company described it as:
“The world’s first printhead and printing system capable of jetting and combining multiple ultra high performance resins with voxel level control, in order to print multi-colored, multi strength and multi functional 3D applications, all-in-one.”
That’s quite a statement.
To find out more about this unusual technology, I spoke with Quantica’s brand new CTO, Ramon Borrel. Borrel has previously spent many years at Xaar, a producer of advanced inkjet printheads that are used not only for 2D printing, but also in an increasing number of 3D printers.
To understand what they’re doing, you must first know of the limitations of current inkjet-based 3D printers. It’s possible to construct a jetting 3D printer using liquid inks: inkjet heads rapidly pass over an entire layer at rapid speed, and UV light can cure it thereafter. This approach has been used to build 3D printers capable of printing objects with multiple colors, textures and even flexibility.
However, there are severe limitations on the types of materials that can be used. This is because the liquid has to be pushed through the tiny inkjet nozzles, and any fluid that has a notable viscosity simply won’t flow.
That means any resin that is viscous cannot be jetted. And that means additives in the resin to make it have important engineering properties are constrained. In other words, you can’t print a broad spectrum of materials with the jetting approach, which can be extremely fast.
But that’s set to change with Quantica’s new approach. They can 3D print fluids up to 15X more viscous than conventional jetting systems. How is this done? There are two factors at play here.
First, the resin is heated. Typically their machine runs at 50-60C, but they can raise the resin temperature up to an astonishing 110C. This heat tends to make resins less viscous, and easier to 3D print.
The second secret is they have found a way to push the fluid with very high pressure. Borrel explains:
“Our principle of operation is different. We have found an extremely energetic way to push fluids with very large piezoelectrics connected to the build chamber. We can push 60-100X harder than conventional inkjets.”
This allows the system to work with high molecular weight resins. Borrel explained they have successfully worked with nanoparticles in resin up to 4 microns in size, but they’ve also found some clients are interested in jetting resins with nanoparticles 20-50 microns, which is quite large.
This capability suddenly unlocks a very broad spectrum of possible materials. For example, they can jet different types of support material that are specialized for certain model materials. They can 3D print metal objects with high particle ratios, etc.
Currently the system’s resolution is at the 600dpi level, equivalent to 40 micron voxels.
Their present technology allows for selectable control of drop volume. This means that a specific voxel could gain a mix of different resins with partial drops by different print heads. This tells me the system could eventually 3D print full color textured objects, or produce regions with varying flexibility, etc.
Borell said they are able to produce objects with excellent optical properties using a proprietary process, and that they have extremely accurate color reproduction. That’s likely due to their long experience with 2D color printing.
The company is still developing their materials roadmap, which is understandable given the near-infinite possibilities that they have available using their process. They intend to deploy their systems to the maximum number of applications, and that will require developing a large array of different materials for the equipment.
Borell explained that the company is actively looking for partners wishing to experiment with the new technology to develop new applications. These may even be well beyond additive manufacturing, for example, coatings.
As for pricing of the T1 Pro, Borell simply said it would be “well below market rates”, so it may be that the T1 Pro 3D printer could be acquired at relatively low cost.
Via Quantica