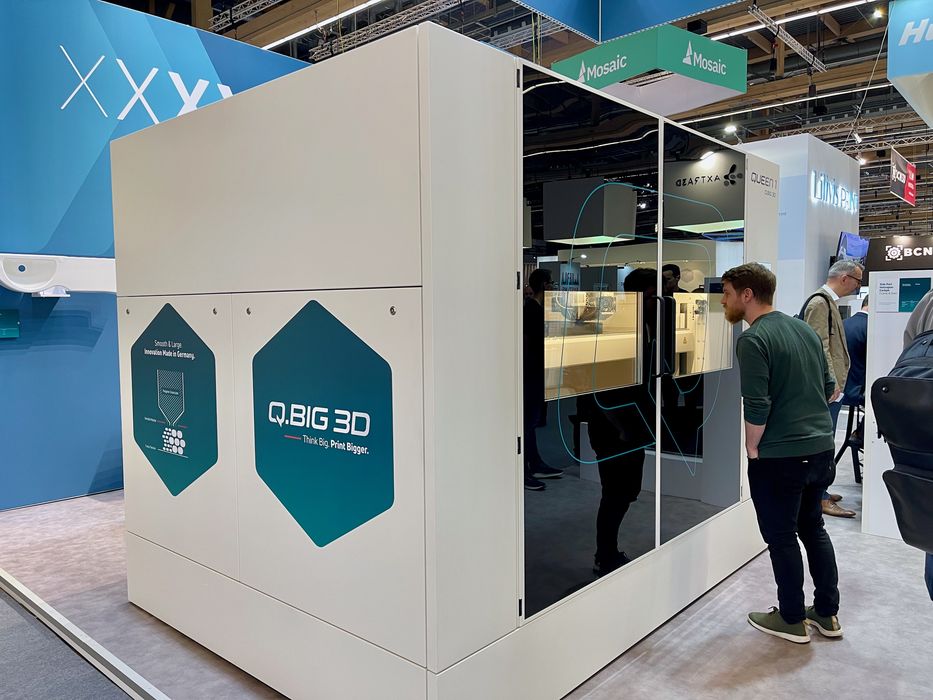
We had a quick look at Q.BIG 3D’s new QUEEN 1 3D printer.
Q.BIG 3D, based in Germany, is one of several new and intriguing 3D print startup companies emerging during the pandemic. The company was founded in 2019 based on a new style of extrusion they call “VFGF”. Their goal is to make 3D printing “economically viable”, and from what I have seen, VFGF could do so. Late this year they emerged from stealth mode and have shown their tech to the world.
The QUEEN 1, billed as an “XXXL 3D Printer”, is definitely big, with a build volume of 1700 x 1050 x 1050 mm. There are few polymer 3D printers bigger than this size.
Now let’s take a look at VFGF. It’s a variation of FGF, or “Fused Granular Fabrication”. In other words, it’s a pellet 3D printer. This is quite important for such a large build volume, as the cost of filament would be tremendous. Pellets are commonly available at far lower pricing.
The QUEEN 1 is an open materials machine, adding to its versatility and economy. Operators are able to source the least expensive pellet materials available and use them in the QUEEN 1. Currently, the company states PLA and PA6 are possible in the device.
The QUEEN 1’s build chamber is heated to 80C, with the print surface able to reach 120C. This theoretically could allow more types of engineering materials to be produced in the machine, so I expect Q.BIG 3D to make further materials announcements in the future.
The other issue with large-format 3D printers is the print durations, which can be excessive, particularly with filament devices that simply don’t deliver enough material to the nozzle. The QUEEN 1 overcomes some speed constraints by using pellets, but the company has also incorporated other features to speed up printing.
One is sheer print speed. The printhead on the QUEEN 1 is able to print at a maximum of 500mm/s, almost 10X faster than typical 3D printers.
So far, so good. But what does the “V” in VFGF stand for?
Variable.
It turns out they’ve developed a unique printhead that can near-instantly switch nozzle diameters, even in mid-print.
There are two sizes of the nozzle, and the company has also developed intelligence to do nozzle switching during printing.
The idea here is to use the coarse nozzle, which is larger than the fine nozzle, to 3D print the unseen interior portions of the print. Then the fine nozzle is used to print the perimeters, which can take on sufficient detail.
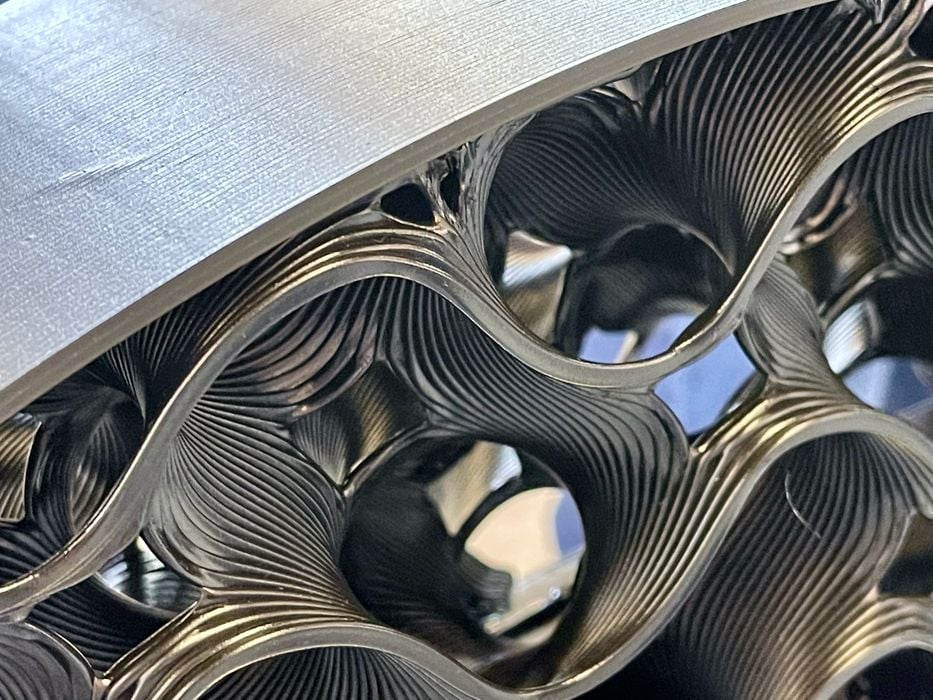
The result is that the print speed can be much higher simply because more material is being extruded each second with the use of the coarse nozzle. Q.BIG 3D indicates print speeds could increase by as much as 4X simply due to this extrusion approach. We’re told the perimeters are printed first, followed by the thicker interior portions. In all, Q.BIG 3D said parts can be 3D printed “up to 40 times faster”.
There’s more. The interior coarse sections are stronger because the extrusions are wider, and molecular bonding within the strand is stronger than between several equivalent thinner strands.
In other words, the prints produced on the QUEEN 1 are faster and are also stronger.
That’s quite a feat among the large-format polymer 3D printers, of which there are few that can match the speed of the QUEEN 1.
The QUEEN 1 can therefore be used to quickly produce large-sized polymer prototypes and production parts for a variety of industries.
The concept appears to be commercially successful, as the Q.BIG 3D website lists a number of customers, including ZEISS, Hachtel and others.
If you’re in the market for a large-format, high speed polymer 3D printer, the QUEEN 1 should definitely be on your list.
Via Q.BIG 3D