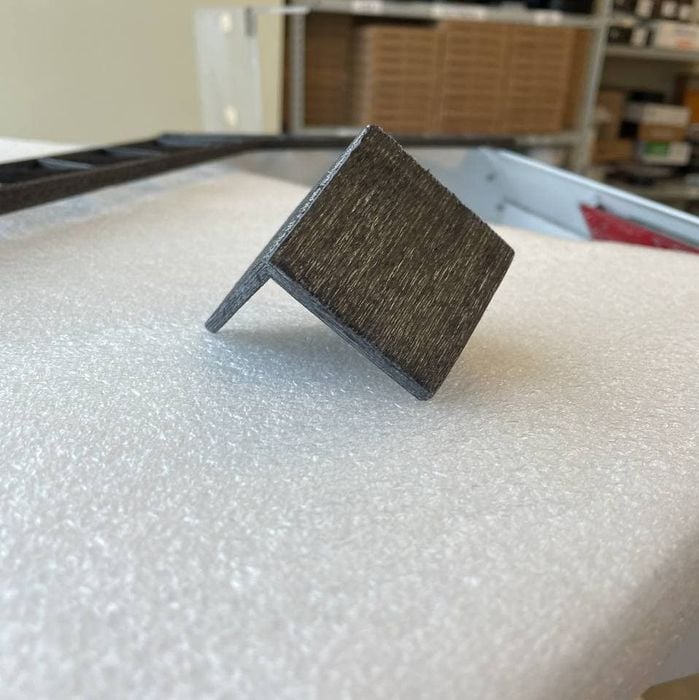
Anisoprint is developing a very powerful approach for 3D printing continuous carbon fiber.
The company has been one of the very few 3D printer manufacturers producing equipment capable of laying down continuous carbon fiber within 3D prints.
Continuous Carbon Fiber 3D Printing
This is quite unlike the “carbon fiber” 3D prints you typically see. Those are simply a polymer mixed with very fine chopped carbon fiber. That approach does increase the strength of the parts, but is nowhere close to that of true, non-chopped continuous carbon fiber. Imagine a long piece of polymer with strands of carbon fiber from end to end; such a part might be as strong as or stronger than metal.
Carbon fiber parts are also quite a bit lighter weight than equivalent metal parts, making them ideal for use in specific industries. There’s quite a bit of interest in “CCF” because of this.
The process of 3D printing CCF is a bit tricky as you have to “lay down” a continuous fiber instead of extruding it as is done with polymer. CCF 3D printers typically have a standard nozzle for the polymer extrusion, and a separate toolhead that can string out CCF and cut it when necessary. Software does the rest to coordinate the two toolheads.
That approach to CCF also follows the standard layer-by-layer method that’s used in practically all 3D printers. Thus you might see a layer of nylon with some CCF on it, then another layer on top of that, and so on. The parts are built layer by layer.
Now there’s one problem with this layer-by-layer approach: while the CCF part might be very strong along the CCF fiber axes, the part is weak between the layers. In fact, the layer strength is going to be the bonding capability of the polymer, which is vastly smaller than CCF.
This poses a bit of a problem: how can you make CCF parts isotropically strong?
3D Continuous Carbon Fiber 3D Printing
One company has been working on an answer, and it’s quite dramatic. Anisoprint has developed a system in which the toolhead itself moves in 3D, very different from the typical 2D layer moves on normal 3D printers.
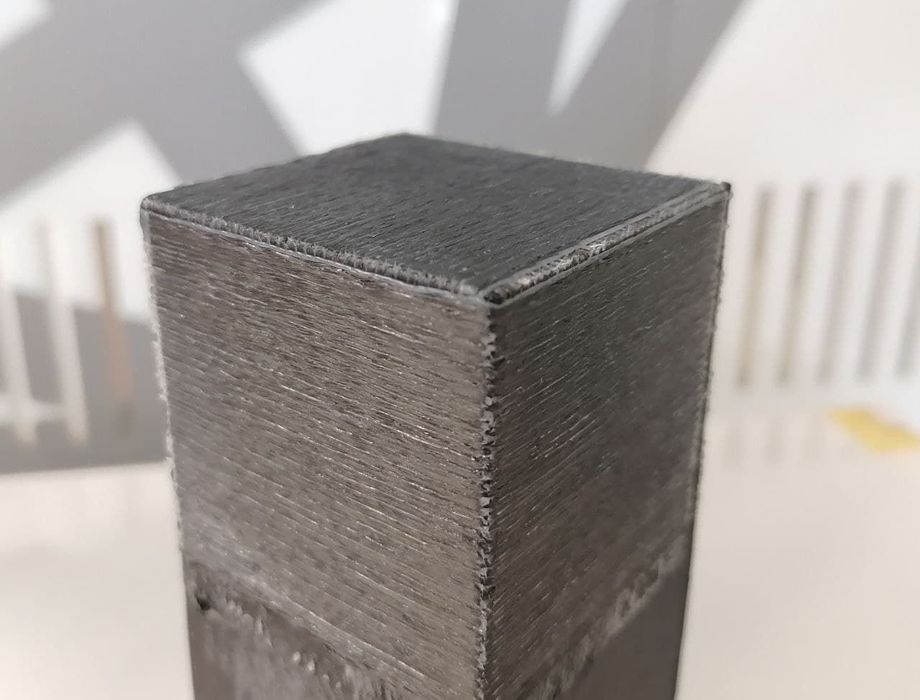
This allows Anisoprint to print “in 3D”, and lay down CCF in orientations that can optimize strength in any required direction.
Not quite sure how this works? We obtained a video of the prototype system in operation:
I don’t think you’ve seen a 3D printer quite like this before, but it seems to have the required capabilities.
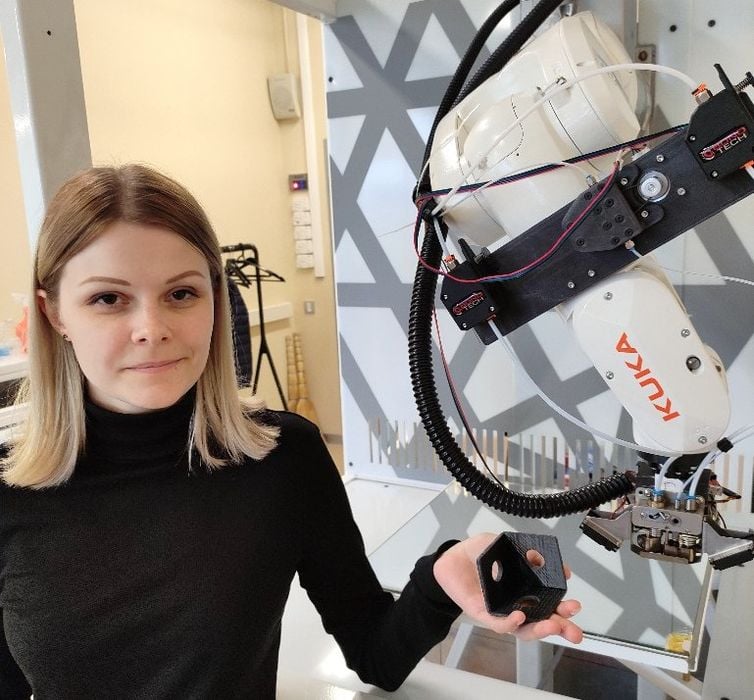
I wondered how the polymer would mix in with this movement and asked Anisoprint CEO Fedor Antonov. He explained:
“The part itself is printed with CFC (co-extrusion – means that there are both fiber and plastic extruded through the same nozzle) only in this case. The support structure is printed with FFF nozzle.
With co-extrusion we can vary fiber volume fraction hence layer thickness and print variable layer thickness (like a bent tube or so) or make layer thickness drops. This makes it more flexible for complex geometries.”
They seem to have produced a nozzle that can extrude both CCF and polymer at the same time. This is perhaps the only way to achieve these 3D movements.
The most intriguing aspect of this development to me is the complexity of software required to drive this system. Imagine a system that could somehow organize the toolpath for arbitrary geometries and at the same time take direction from the operator on which axes, surfaces and segments to provide extra strength, in three dimensions, not just two?
Antonov explained that the complex slicer deals with surfaces rather than with layers, which is a paradigm shift for slicing technology.
This capability is still under development by Anisoprint, and we will have to wait until it is released.
Via Anisoprint