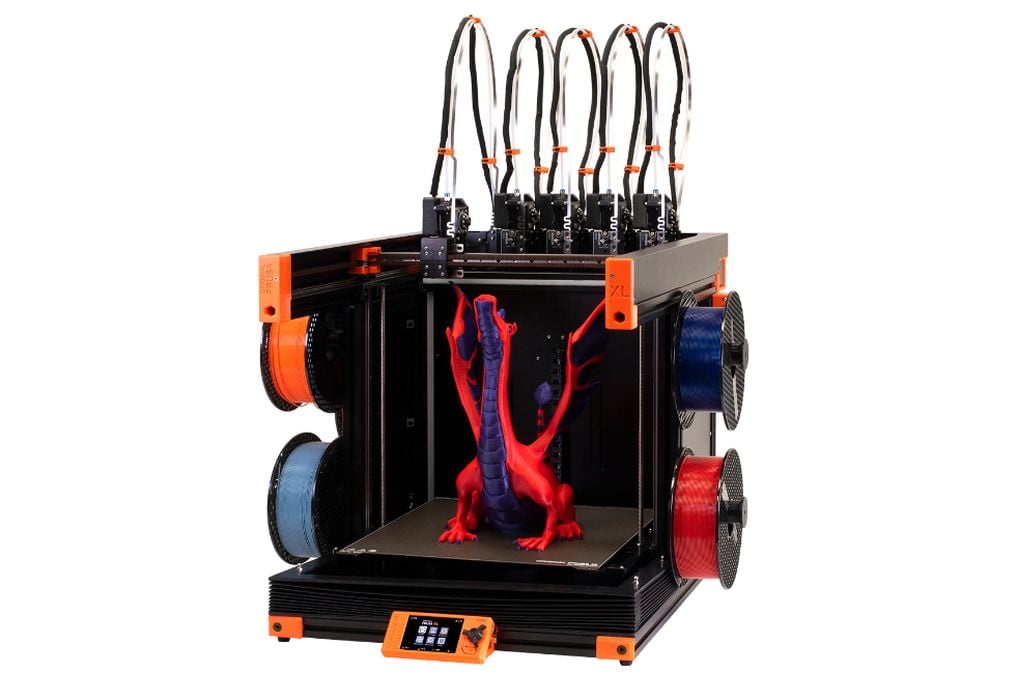
Prusa Research has been hinting about a mysterious “XL” desktop 3D printer, and suddenly released many details about the device.
While many have been awaiting a hypothetical MK4 3D printer from the Czech 3D printing giant, they’ve instead been busily developing a rather different device, the Original Prusa XL 3D printer.
We knew from hints long ago that this was intended to be a larger format device with a huge build volume. This is actually quite a normal step by many 3D printer manufacturers, who typically acquire some longer frame parts and simply make the build volume taller.
That is not what Prusa Research did, not at all.
Prusa XL Build Volume
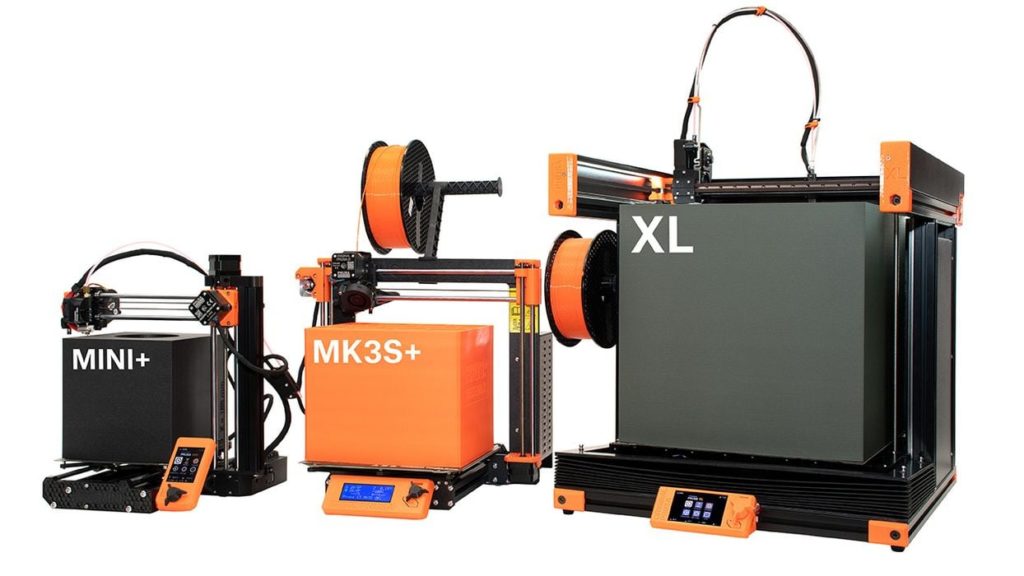
Whereas the standard MK3S 3D printer has a build volume of 250 x 210 x 210 mm, the upcoming XL will be a massive 360 x 360 x 360. That’s more than a 4X increase in build volume!
The huge build volume is one thing, but for me more noticeable were a number of other features built into the XL.
The main mechanical difference is that the XL uses a coreXY design, which, if you think about it, is really required for this larger build volume. A huge machine trying to push and pull the build plate back and forth is not optimal and would certainly introduce all kinds of vibrations and momentum problems. The coreXY design solves that, and it’s a first for Prusa Research.
Prusa Research said prints will likely take days to complete on this massive machine, and I don’t doubt that at all. But the longer print duration also implies something else: reliability had better be good, otherwise long print jobs could frustratingly fail. To overcome this, it seems that Prusa Research has included a number of quality features and others to ensure long print success.
One is huge telescopic spool mounts on the side of the device. These are apparently able to hold up to 3kg in weight, meaning a print job could take 3X longer before requiring manual intervention to swap out spools over typical 1kg spools setups.
Prusa XL Heatbed
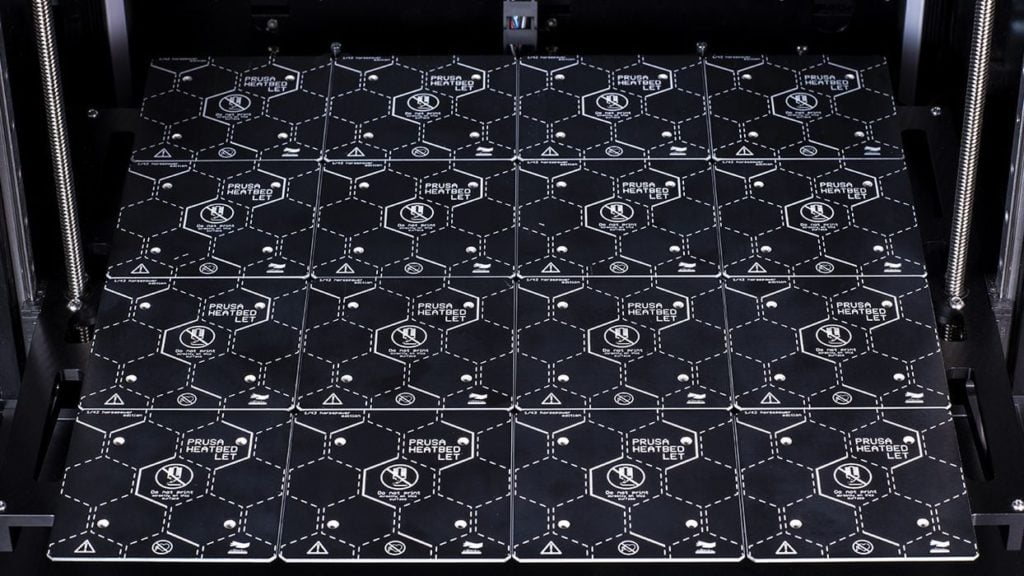
The heatbed is obviously larger due to the increased build volume, but this implies vastly increased energy use to heat it all. For jobs requiring only a smaller portion of the plate, it is divided into 16 individually selectable heat zones. Thus operators will be able to optimize energy use, and likely speed up warm-up time, too. Prusa Research explains more:
“Our new heatbed with individually controlled 9×9 cm segments is not only energy-efficient (you can turn on/off individual pads) but also effectively reduces warping thanks to its expansion gaps between each segment. To explain it a bit: regular heatbeds have a tendency to warp as the temperature increases. The problem isn’t very evident with smaller surfaces and can be partially compensated for with mesh bed leveling. However, once you have a large heatbed, the issues become more noticeable.”
Making a large-format 3D printer is absolutely not just scaling up an existing design. Here, the company has basically “started over” to solve issues inherent with larger scales.
Prusa XL Nextruder
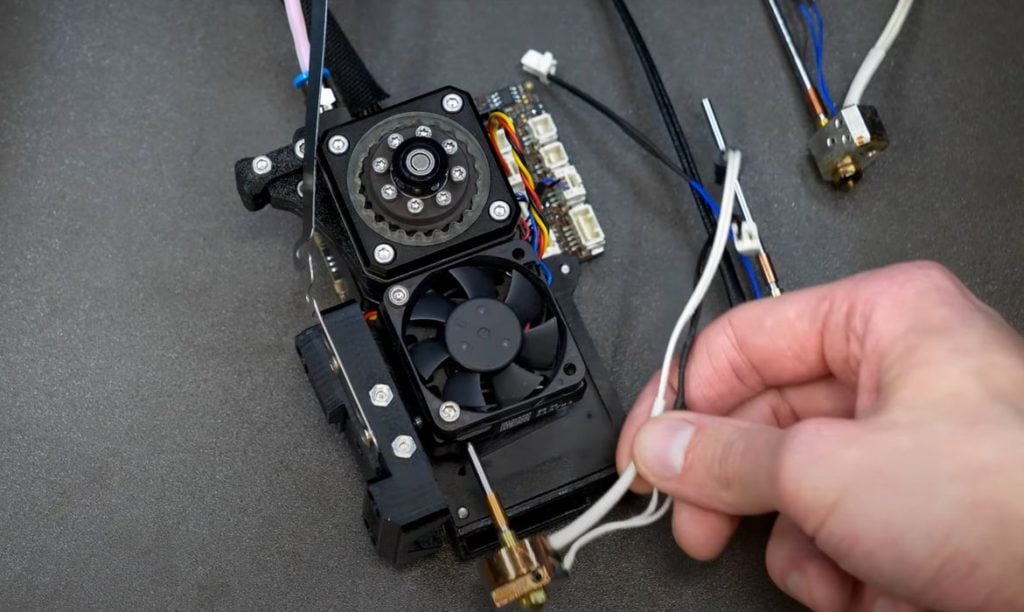
The XL also sports a completely new extruder, called the “Nextruder”. This is a much larger design that apparently took three years to develop. It has the unusual ability to use the nozzle as a sensor to probe the print surface based on a load cell sensor. This ultra-precise mechanism should allow the XL to 3D print first layers perfectly on each and every job.
This means there is no need for the traditional adjustment of the Z-gap when print jobs start, because the XL can do that all by itself. This is an unprecedented feature that, again, should be on every 3D printer. For now, it seems to be only on the upcoming XL.
This “super sensor” is also able to detect jams, even partial jams, because of its sensitivity and direct access to the action in the hot end. No doubt Prusa Research is tuning up their firmware to do all kinds of magic reliability function with this ability.
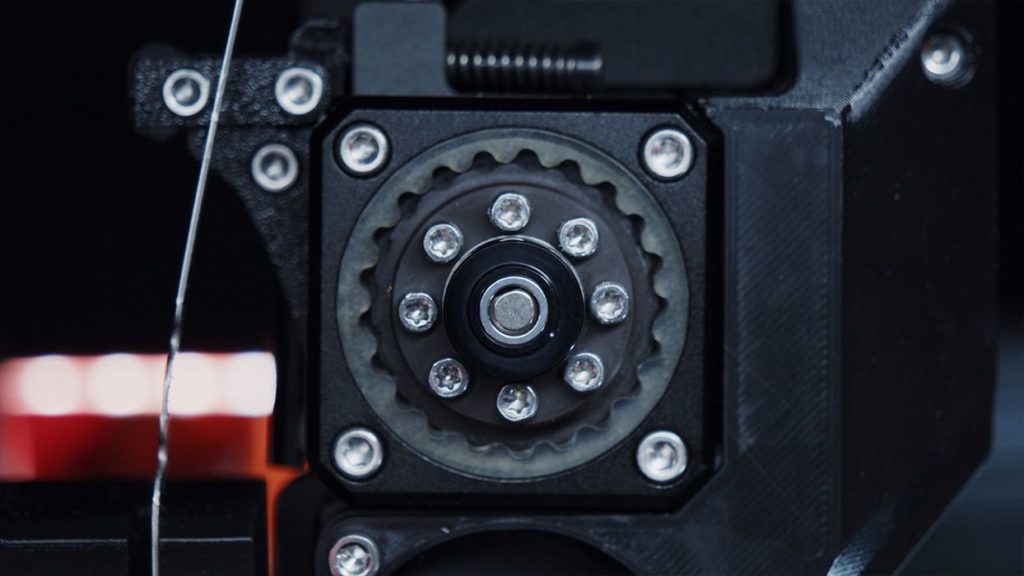
The Nextruder also has a “zero-backlash cycloidal gearbox with a large no-slip drive gear”. I’m not quite sure what this means, but they say it provides for greater flow control. Again, this leads to increased print quality and reliability.
One very interesting feature is a second thermistor positioned a bit higher on the hot end. This enables the firmware to detect heat creep that often fouls hot ends when soft thermoplastic sneaks up the pathway into the cold zone. Evidently they partnered with E3D-Online to develop this feature, so this might be available on other equipment in the future.
Prusa XL Tool Changer
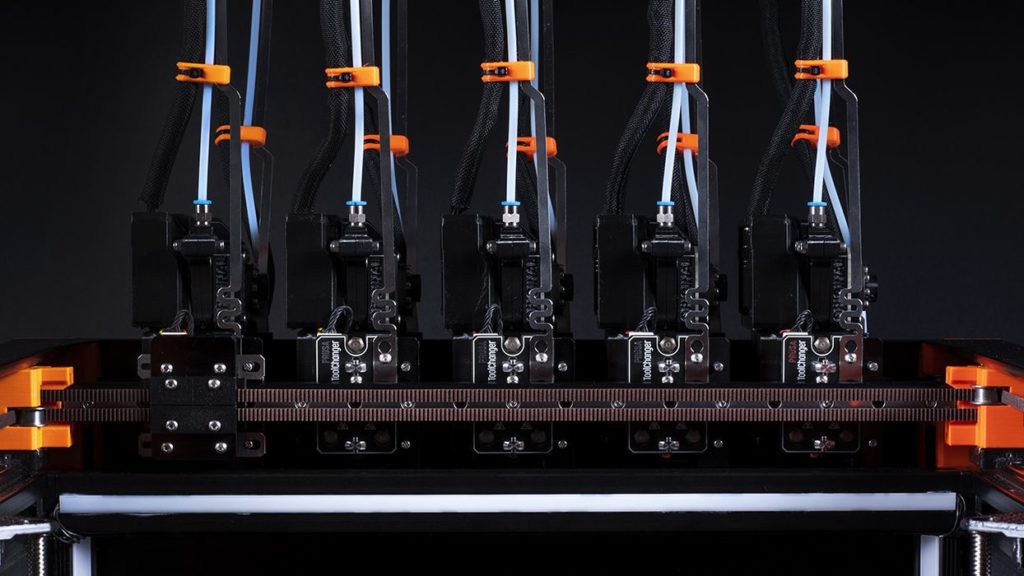
Finally, the XL will apparently be a tool changer! It will have up to five independent tool heads that are quickly swapped in and out during a print job. These can be kept warm so that they can be used instantly. This approach, although a lot more mechanical, allows for multicolor 3D printing without alignment problems, drips or other quality issues, all done at high speed. This is quite reminiscent of E3D-Online’s tool changing 3D printer.
The tool changer will also allow for the use of soluble support material, that enables operators to 3D print highly complex objects without fear of “support removal hell”.
Prusa Research also briefly mentions that the spool holder will be able to recognize filament with some type of sensor. This has a number of implications that are beyond this report.
In fact, I will write a second story on the XL’s implications for Prusa Research and its affect on other 3D printer manufacturers very soon.
Can you buy an Original Prusa XL now? Not exactly
It’s available for pre-order, with a healthy but refundable deposit of US$200. Pricing ranges from US$1999 for a single-head machine, to US$3499 for the full five-tool machine. Shipping is expected later on in 2022, but is uncertain due to the current supply chain crisis.
Via PrusaPrinters