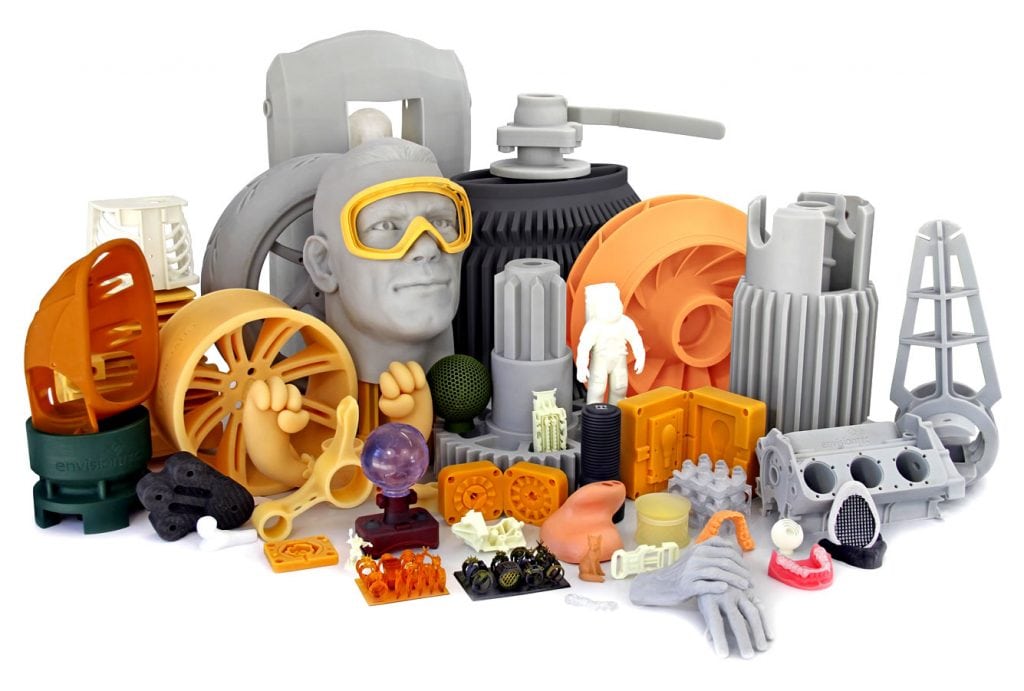
Recent 3D printing acquisition announcements have something significant in common: production focus.
As a quick rundown of some of the most high-profile M&A moves made recently in additive manufacturing:
- In September 2020, Covestro announced the intent to acquire the DSM Resins & Functional Materials line of business, including DSM Additive Manufacturing; earlier in 2020, DSM had already acquired some of Clariant’s 3D printing material business.
- More on this acquisition from DSM’s Hugo da Silva.
- In December 2020, Stratasys announced the intent to acquire Origin. This transaction closed at the end of the year, with Origin officially a Stratasys company announced at the start of 2021.
- In January 2021, Desktop Metal announced the intent to acquire EnvisionTEC. This transaction is expected to close in February.
As M&A activity ramps up to start this new year, we have to wonder: are we entering a new consolidation phase in the additive manufacturing industry?
3D Printing Industry Consolidation
Historically — meaning about half-a-decade ago — the 3D printing industry saw significant consolidation as two of its major players engaged in substantial M&A. Between 3D Systems and Stratasys, dozens of startups and smaller players were folded into the two then-leading companies in this industry. By Kerry’s count back in 2015, 3D Systems alone acquired more than 50 companies within a 15-year span.
The reasons for these acquisitions varied strategically. Some were made to grow the companies’ portfolios, others to snag and even snuff potentially competitive technologies. Some were designed to gain access to new materials, distribution networks, or software platforms. Some were people-centric to bring innovative minds to a larger company.
Of course the strategic reasons for M&A activity often vary — but sometimes a singular trend arises. And that’s what we see happening now.
Production 3D Printing
Of the three recent/pending acquisitions taking the 3D printing limelight, there’s one area of focus to highlight: production. Specifically, polymer production.
High-throughput 3D printing technology with high-quality 3D printing materials, especially combined with high-profile 3D printing marketing and distribution channels, represent a major strategic approach to the market today.
3D printing for production has been a concept bandied about for some time now. “Break-even points” have long been a highlight of new technology presentations, representing the point at which it made sense to 3D print versus injection mold in terms of production volumes. Those break-even points have been moving, though, as more materials and more additive manufacturing processes have become increasingly able to actually produce relatively large volumes of products.
Additive manufacturing in early 2021 is not what it was a decade, or even half a decade, or half that time again, was. Today’s technologies are often squarely industrial. A production line without a 3D printer of some kind will become a thing of the past, as many posit with growing credibility.
While a lot of production focus for 3D printing has been placed on metal technologies, the real growth opportunity right now is on the polymer side. With years more development behind them, polymer 3D printing processes are currently better understood, and in many cases a wider portfolio of engineering-grade polymer materials are available than their metal counterparts. Automation on many a DLP/SLA production line is likewise enhancing the ability to place, remove, clean, and cure parts with minimal human intervention.
With both Stratasys and Desktop Metal stepping out from their flagship 3D printing processes through their new acquisitions, their moves are especially poignant. The companies’ FDM and SPJ processes, respectively, represent major technological achievements. But the desire to expand process portfolios with, respectively, P3 and DLP processes highlights something that ought to be highlighted across all manufacturing industries:
There is no one best tool; there is only the best tool for the job.
That is: when someone asks “What’s the best 3D printer available today?” there’s never a clear-cut simple answer. There’s only a necessary follow-up: “What do you need it to do?”
One 3D printer, one material, cannot do everything. Many are incredibly versatile; if you can 3D print ULTEM or Nylon 12, for example, there’s quite a lot you can do. But you can’t do everything. Some jobs need flexibility, others absolute rigidity; some need ESD properties in delicate performance environments, others must stand up to UV light without degradation. And for each of these material needs, there’s the need for the appropriate hardware able to handle it (and software able to account for material profile and print parameters).
Expanding a product portfolio to include more options, more capabilities, all available from a single parent source operating through a single distribution network will enable a lot more customer requests to be met.
Doing so on a large scale, with the repeatability and reliability necessary for true production quality and scale, is a major step forward for 3D printing.
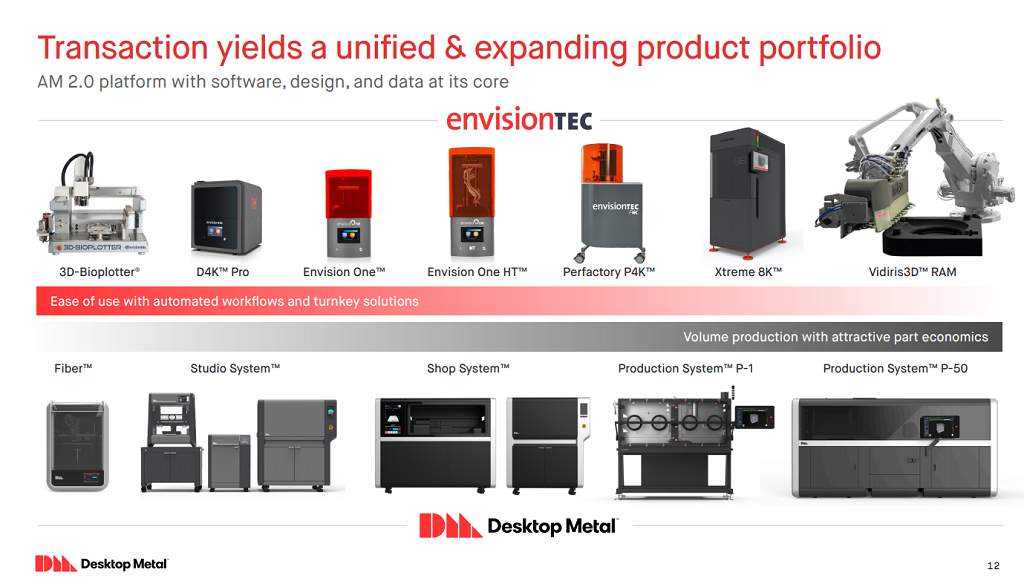
And seeing significant players like Stratasys and Desktop Metal on the hardware side and Covestro/DSM on the materials side offers a major statement to the industry.
There is no one right tool for the job — but there may be a right tool shed housing all the best tools.