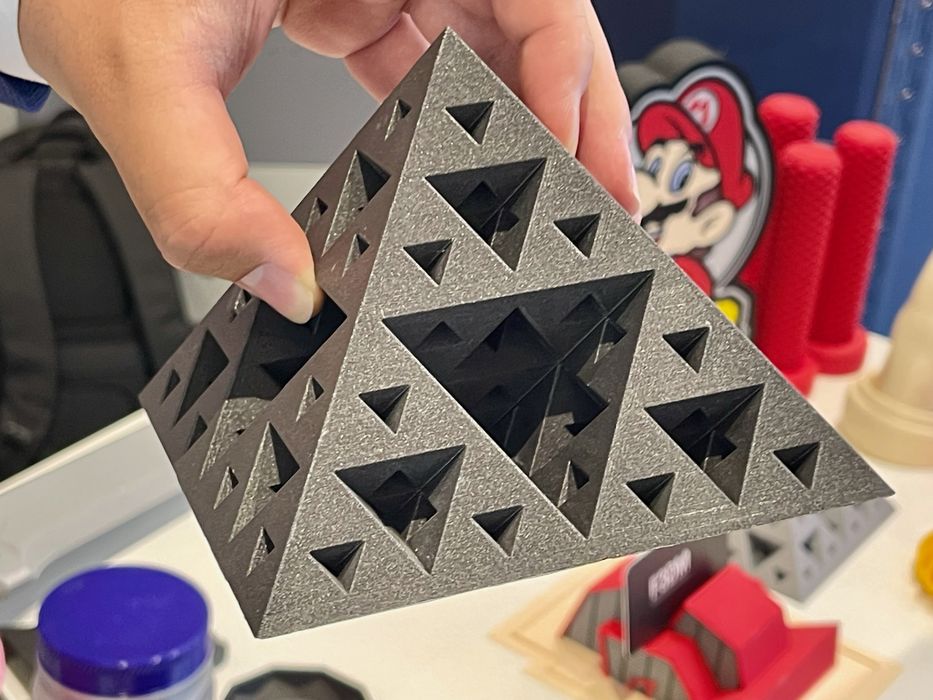
We had a look at filaments from F3DM and discovered something quite interesting.
F3DM is a London-based firm providing a wide selection of 3D printer filament products and resales of several 3D printer brands. Their current “Uzy” lineup includes around 32 different variations and colors of PLA and PETG.
During our discussion, F3DM representatives were keen to point out that their filament is among the most precise in the industry.
I asked how this is achieved, and was told their production line uses laser-based diameter sensors at an incredible rate: 7000 samples per SECOND!
The result is three levels of filament product:
- Basic, which has a maximum diameter variation of 0.050mm
- Pro, 0.025mm
- Premium, “under 0.010mm”
That’s quite incredible. For a long time it was considered that anything under 0.05mm was “good quality filament”. Later I would see promotions touting 0.04mm or even 0.03mm, but F3DM’s seems to be far better.
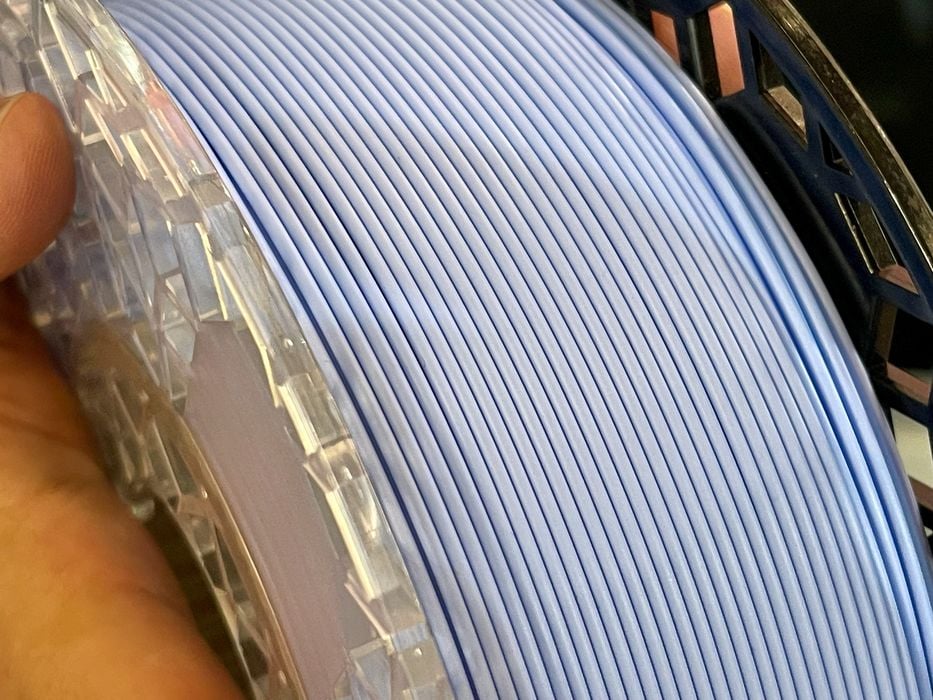
I know you can’t see such variations, but this view of a spool of their filament does look very accurate.
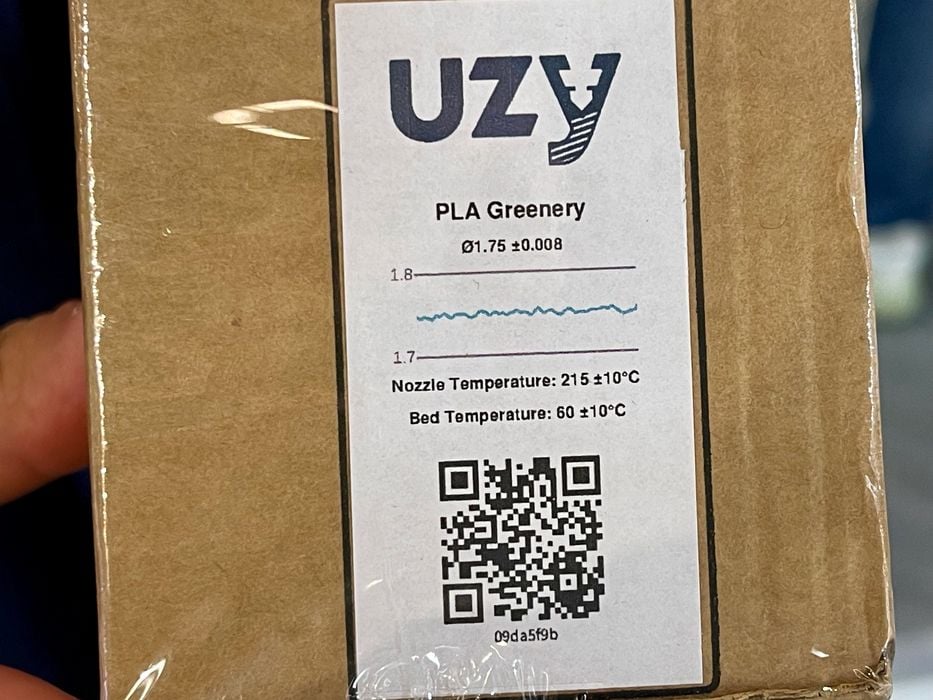
Here’s the packaging for one of their filament products, and you’ll note there is a QR code. From this code you can go to a website to view information about the production of that particular spool.
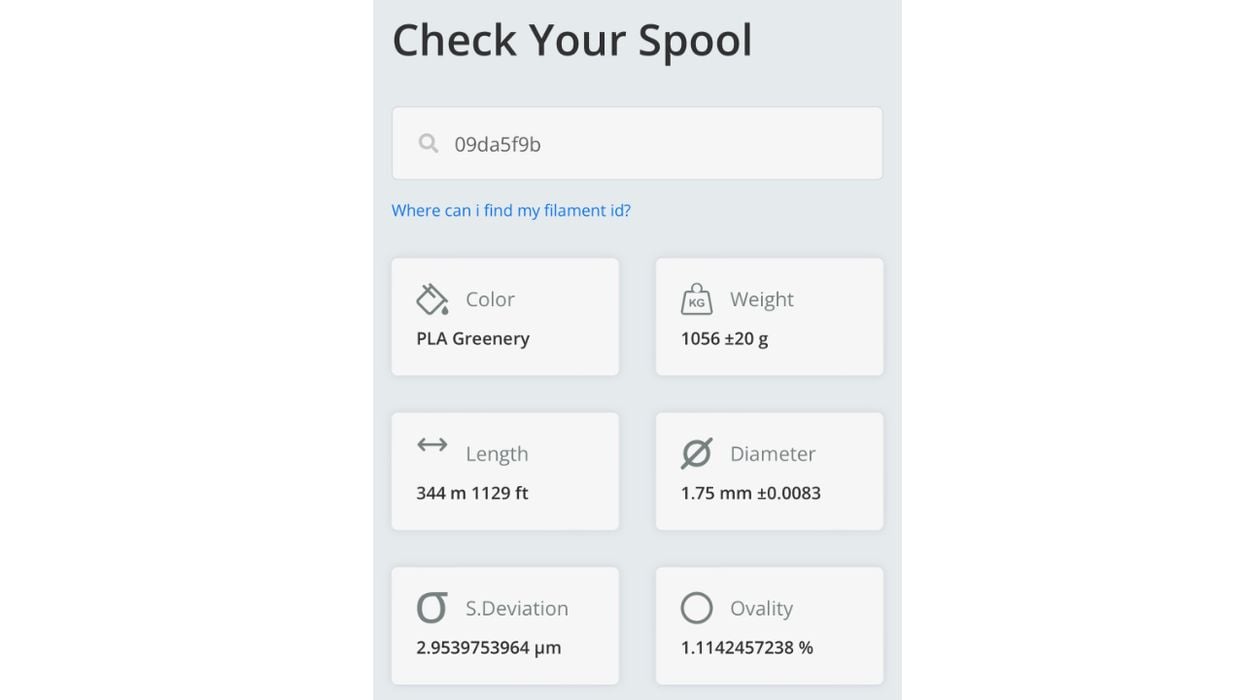
This is what you see when you visit the site.
This information is quite helpful, but using QR codes for production information isn’t new: Prusa Research introduced that several years ago.
However, in discussions with F3DM, it seems there is a bit of a difference here. F3DM apparently records the ENTIRE scan sequence of spool production. In other words, they know the exact diameter of each millimeter of every spool. That must be a lot of data!
They suggested a very intriguing application for this data: managing extrusion flow.
Their concept would be to supply the diameter data to the slicer (or printer), which would then dynamically adjust its extrusion rate to match the slightly varying diameter of the input filament.
There would be no need for flow sensors, as it would all be calculated and executed mechanically. However, I foresee challenges in synchronizing the filament with the extruder.
Another way to implement this approach is to build some type of diameter sensor right into the toolhead, so that it could perform the measurements itself without concern for synchronization. That might prove expensive, however.
While that possibility may or may not actually be implemented, it’s pretty clear that F3DM offers a set of very accurate filaments. These would be best used in high performance 3D printers that can perform precision extrusions and movements.
Good material in, good prints out.
Via F3DM