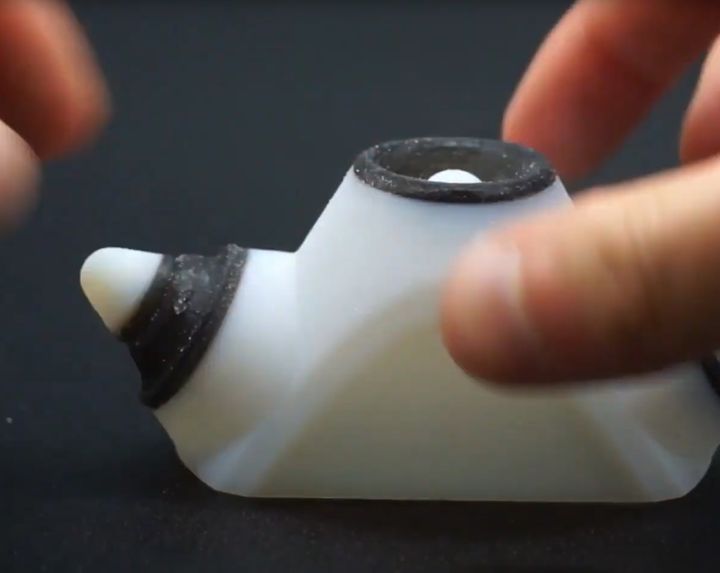
Researchers have been experimenting with techniques to 3D print objects that can be unfolded into their full size after printing.
The constraints of build volume have long been an issue in 3D printing. This has led to the development of large-format 3D printers, but the issue still persists on smaller gear. It’s always possible for a new print request to exceed the available build volume.
One approach for overcoming this problem is to 3D print objects in a smaller volume but then “unfold” them into their full, functional state.
There are several ways to achieve this, all complex. I first encountered this concept some years ago when researchers were attempting to 3D print fabric, and were severely limited by the build volume, as most 3D printed fabrics are essentially 2D: flat on the build plate.
The solution at the time was to design a way to “fold” the 3D model in such a way as to pack it into the build volume in three dimensions, while at the same time retaining all the links between the cells of the fabric.
This approach did work, but apparently is costly to generate the 3D model geometry.
Now there’s another approach being experimented with, and it’s a bit different. Instead of folding 2D objects, this method involves using “pop ups”.
Where a tall structure or protuberance exist, it is replaced by a pop-up structure. This could be a “dimple” made of continuous material, or it could be an “extension” made from concentric structures that slide over each other.
You can see how this works in this short video:
The researchers explain their approach:
“To achieve Pop-up Print, we first conducted an experiment using selected printed sample objects with several parameters, in order to determine suitable crease patterns that make both the unfolded and folded state mechanically stable. Based on this result, we developed an interactive design tool to convert 3D models — such as a Stanford Bunny or a Huffman’s cone — to the folded shape. Our design tool allows users to decide non-intuitive parameters that may affect the form’s mechanical stability, while maintaining both functional crease patterns and the object’s original form factor.”
At this point, this is simply research, but it does provoke some thought about how this approach could be integrated into future real-life 3D printing. One could imagine specialized “folding” software that would examine a geometry and apply one or several techniques to reduce the print volume. Perhaps a fold here and a pop-up there, and suddenly the object is half its original height.
While that might not save material, it could save 3D print time depending on the 3D printing process employed: some processes’ print time is directly proportional to the number of layers being printed, regardless of the amount of material on each.
As that magic software does not yet exist, we have to continue looking for larger build volumes on our equipment, and adding the cost for them, too.
Via ACM (Hat tip to Nicole)