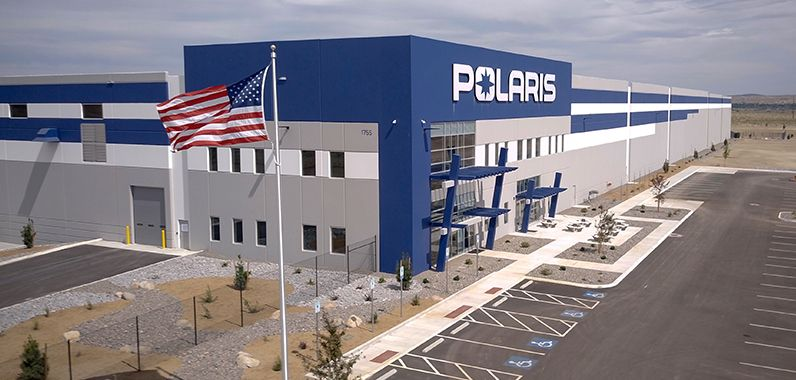
Charles R. Goulding and Ryan Donley consider the use of digital inventory in automotive manufacture as industrial 3D printing picks up steam.
Polaris Industries is one of the leading sports-vehicle makers in North America. The company leads with a 40% market share in the segment and saw a sharp increase of revenue of 25% in 2020 compared to 2019. Amidst the great performance by Polaris though, a delicate supply chain has forced the company to shift strategies and produce their products based on whatever parts they have on hand.
According to the company, changes like this can occur daily based on what parts are available in house, determines what vehicle gets produced. The production strategy has led Polaris to essentially mix and match parts and get what they can deliver to customers. An example of this is prevalent in several vehicles where some that are normally four seat models, are now being delivered as two or three seat models and customers are still ordering them regardless, putting Polaris into tight supply and re-supply levels. The ongoing company approaches are essentially the antithesis of the typical just-in-time (JIT) inventory optimization strategy that has been utilized in the industry. JIT allows flexibility in what can be produced and when without having a stockpile of huge inventories, but supply chain disruptions have forced Polaris to take what they can off the shelves and from suppliers and put together whatever products they can.
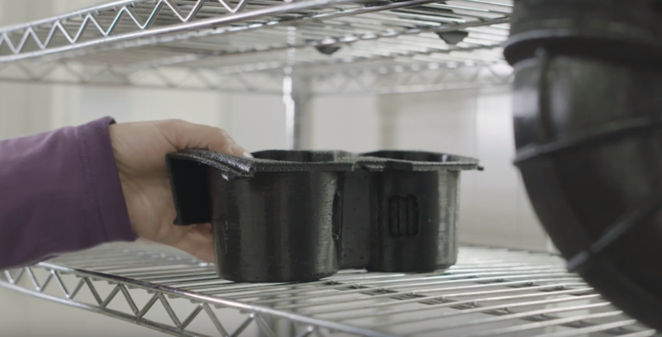
With a fragile supply chain and numerous large suppliers not being able to deliver on time, Polaris could eventually shift to more internal part and material sourcing with the increased use of 3D printing.
The company has already dedicated numerous resources to 3D printing by adding more Stratasys 3D printers, expanding their initial investment in the printers from 2014. Further experimentation into additive manufacturing would add leverage from a production standpoint as lead times for numerous parts can be reduced. This would also allow for less reliance on suppliers who are easily strained by supply chain fluctuations and cannot deliver parts when needed.
As shown in the table below, Polaris is committed to research and development (R&D) and has numerous dedicated buildings for R&D with a total staff of 1,500 employees, including additive technology designers and engineers.
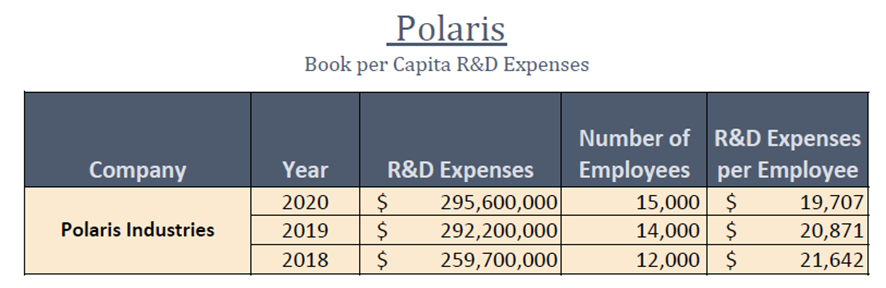
The Research & Development Tax Credit
The now permanent Research and Development (R&D) Tax Credit is available for companies developing new or improved products, processes and/or software. Eligible costs include U.S.-based employee wages, cost of supplies consumed in the R&D process, cost of pre-production testing, contract research expenses, and certain costs associated with developing a patent. As of 2016, eligible startup businesses can use the R&D Tax Credit against $250,000 per year in payroll taxes.
3D printing can help boost a company’s R&D Tax Credits. Wages for technical employees creating, testing and revising 3D printed prototypes can be included as a percentage of eligible time spent for the R&D Tax Credit. Similarly, when used as a method of improving a process, time spent integrating 3D printing hardware and software counts as an eligible activity. Lastly, when used for modeling and preproduction, the costs of filaments consumed during the development process may also be recovered.
Whether it is used for creating and testing prototypes or for final production, 3D printing is a great indicator that R&D Credit eligible activities are taking place. Companies implementing this technology at any point should consider taking advantage of R&D Tax Credits.
Conclusion
Utilizing additive manufacturing in-house to source more parts can be a significant investment of resources. Polaris currently has the capital investment in additive manufacturing to begin using the technology and rely less on suppliers to meet the growing demand from customers that has caused the company to resort to drastic production strategies.