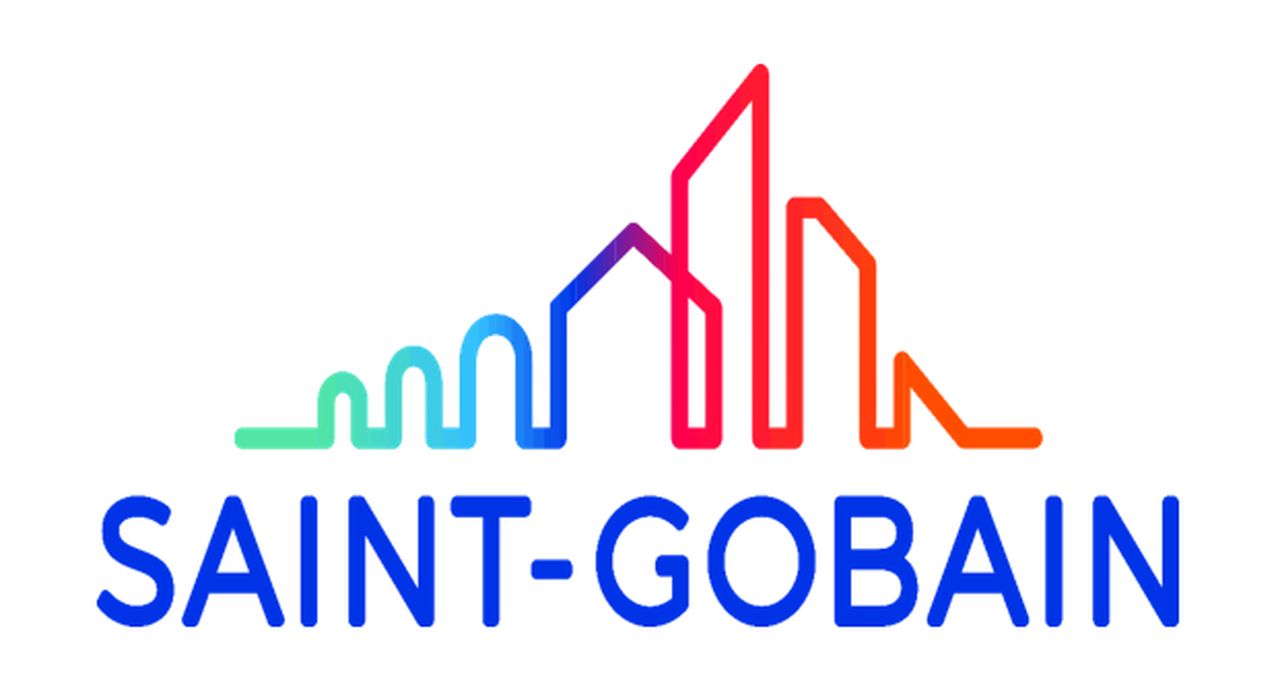
Charles R. Goulding and Preeti Sulibhavi discuss Saint-Gobain’s proactive approach to 3D printing integration.
French manufacturing giant Saint-Gobain has been at the forefront of exploring applications for 3D printing across its diverse operations. From printing bridges and houses to custom tooling for factories, the 350-year-old innovator sees great promise in 3D printing and additive manufacturing to enable more sustainable and efficient production processes.
Saint-Gobain Weber (Weber), which produces construction materials like concrete and mortar, opened Europe’s first concrete 3D printing factory in 2019. Located in Eindhoven, Netherlands, the state-of-the-art facility houses an industrial-scale 3D concrete printer capable of fabricating full-scale construction components. The company has already printed multiple bridges, houses for the Milestone project, and even a 12-meter-tall structure that earned them a Guinness World Record.
Weber also runs an annual Concrete Design Masterclass where architecture students get hands-on experience with concrete 3D printing and other novel construction methods. They collaborate with textile companies to have the students make molds and cast their own concrete models in addition to operating the 3D printer. Weber’s concrete printing expertise even attracted landscape furniture maker, “Urbastyle,” to jointly develop 3D printed concrete benches. With infinite customizability and lightweight yet durable constructions, they exemplify the technology’s potential.
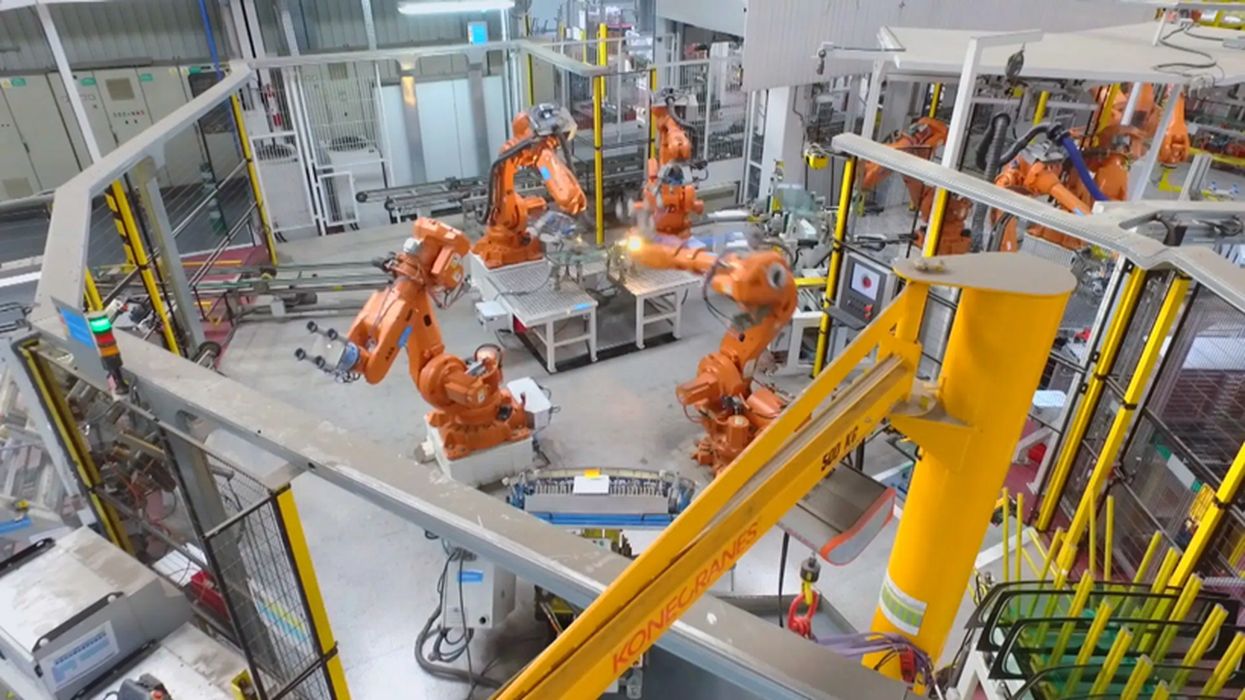
The plant (shown above) reports saving €170,000 on tooling expenses since 2019 in addition to reducing lead times by 93%. Such a drastic boost in efficiency and cost savings highlights the power of 3D printing for production applications. Other auto manufacturers like Nissan and BMW have also turned to BCN3D’s printers recently as the transportation industry recognizes the benefits of additive manufacturing.
On the automotive production side, Saint-Gobain’s glazing plant in L’Arboç, Spain has leveraged 3D printing to enhance their manufacturing efficiency. By adopting BCN3D printers in 2019, the factory has printed numerous custom tools, jigs and fixtures used in their automated glazing lines. This has allowed them to bring the production of these support tools in-house instead of relying on more expensive external machine shops.
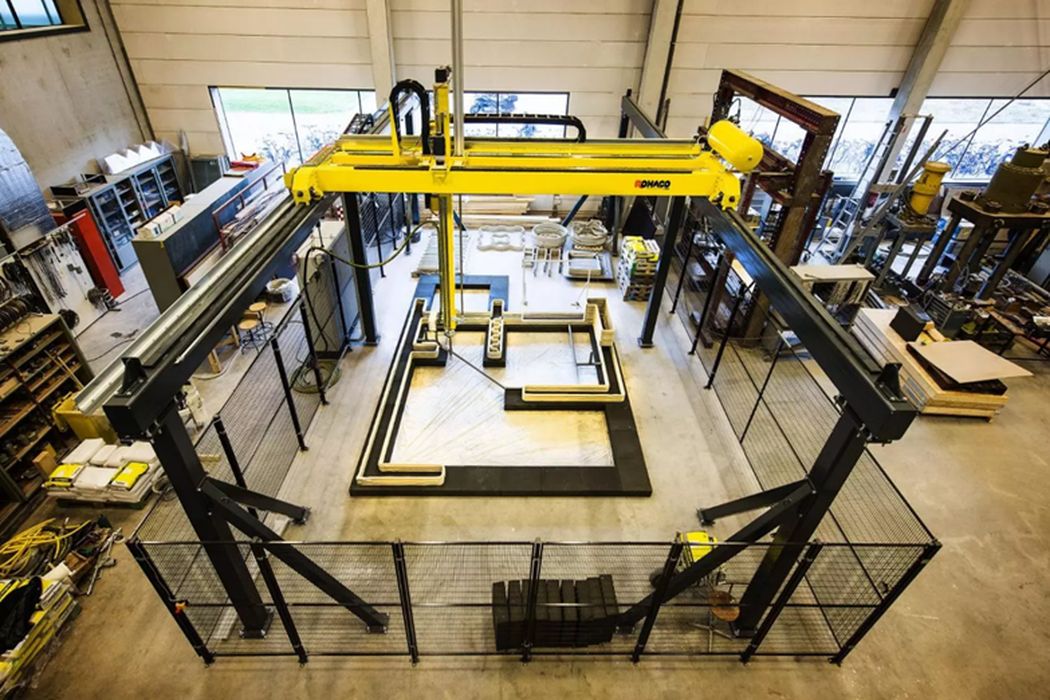
The Research & Development Tax Credit
The now permanent Research & Development Tax Credit (R&D) Tax Credit is available for companies developing new or improved products, processes and/ or software.
3D printing can help boost a company’s R&D Tax Credits. Wages for technical employees creating, testing and revising 3D printed prototypes can be included as a percentage of eligible time spent for the R&D Tax Credit. Similarly, when used as a method of improving a process, time spent integrating 3D printing hardware and software counts as an eligible activity. Lastly, when used for modeling and preproduction, the costs of filaments consumed during the development process may also be recovered.
Whether it is used for creating and testing prototypes or for final production, 3D printing is a great indicator that R&D Credit eligible activities are taking place. Companies implementing this technology at any point should consider taking advantage of R&D Tax Credits
Conclusion
Across applications ranging from concrete construction structures to custom automotive tooling, Saint-Gobain continues to explore innovative uses of 3D printing. The venerable company has clearly embraced this technology as an integral part of its next-generation, digitally enhanced manufacturing capabilities.
As one of the first adopters and foremost pioneers in the field, Saint-Gobain provides an inspiring model for bringing 3D printing solutions to long-established industries. Their forward-thinking investments reflect the business advantages possible with 3D printing and additive techniques.