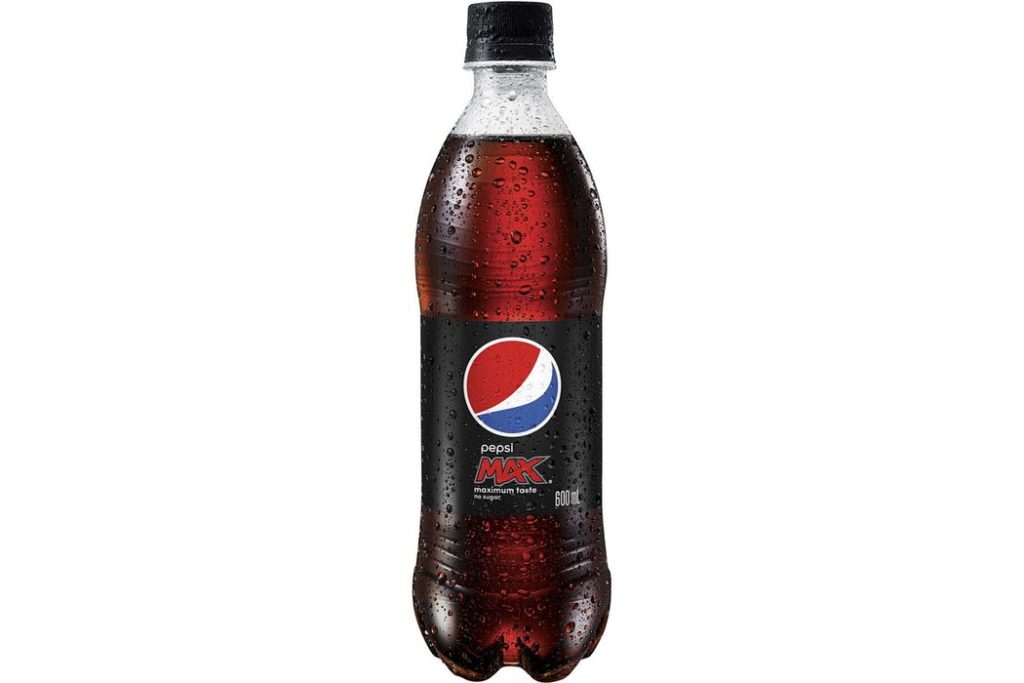
Drink giant Pepsi is getting into the 3D printing business.
The company announced today a large and comprehensive “green” initiative. The initiative includes a number of projects, including changing the power source at all of their bottling plants to green energy.
But deep down in the details there was something of interest to the 3D printing community: Pepsi intends on producing 3D printer filament of its own.
Let’s back up a bit to understand what’s actually going on here.
For many years the majority of the company’s drinks have been delivered in two forms: aluminum cans and plastic bottles. The aluminum is an easily recycled metal that is reasonably expensive, and that has led to widespread recycling programs. This has saved countless tons of CO2 through the re-use of the aluminum.
But Pepsi’s internal research indicated the same was not happening for their plastic bottles. They felt that a recycling program could solve the problem.
That’s good news, because our environment is increasingly polluted with plastics of all kinds. Even large items like bottles eventually break down into fine plastic bits that find their way everywhere: into our soil, rivers and oceans, and eventually even into our own bodies. At some point in the future this is will become a major issue to be dealt with.
Meanwhile, Pepsi’s forward thinking leadership is going to take one of those steps immediately with the production of 3D printer filament.
Recycled plastic being made into 3D printer filament is not a new concept, but it has never really taken off. The biggest issue is that a typical pile of plastic scraps contains a wide diversity of plastic materials. You can’t just melt it all down and re-use it: the plastics will have different melting points, let alone other engineering characteristics.
Some recycled 3D printer filament programs have solved that problem by accepting only specific materials for recycling, thus ensuring only one type of material is collected. Drink bottles from a specific manufacturer, for example, would all be made from the same material.
That is the case with Pepsi’s plastic bottles. They are all made from a specific blend of PET.
Pepsi’s new concept is to launch a worldwide recycling program in which drinkers can freely return their empty PET Pepsi bottles. These would be collected and then prepared for recycling: cleaning, crushing, chopping and eventually melting and extruding into highly usable 3D printer filament.
Pepsi intends on marketing the new 3D printer filament under their new “Pepsiment” filament brand, similar to how Prusa Research named their materials “Prusament”.
Given Pepsi’s massive production of bottles — said to be over 600,000 bottles PER DAY in the United States, they should be able to produce a great deal of filament very easily and at low cost.
Each Pepsi bottle contains approximately 28g of PET, so a 1kg spool of Pepsiment would be achievable with the collection of only 36 bottles. It’s possible the company could produce as many as 17,000 spools of PET every day, all year long.
With that volume it’s very likely Pepsi will be able to offer Pepsiment at rock-bottom prices. So far they have not revealed the Pepsiment price structure, but we’ll be watching closely.
Pepsiment: the choice for a new generation!