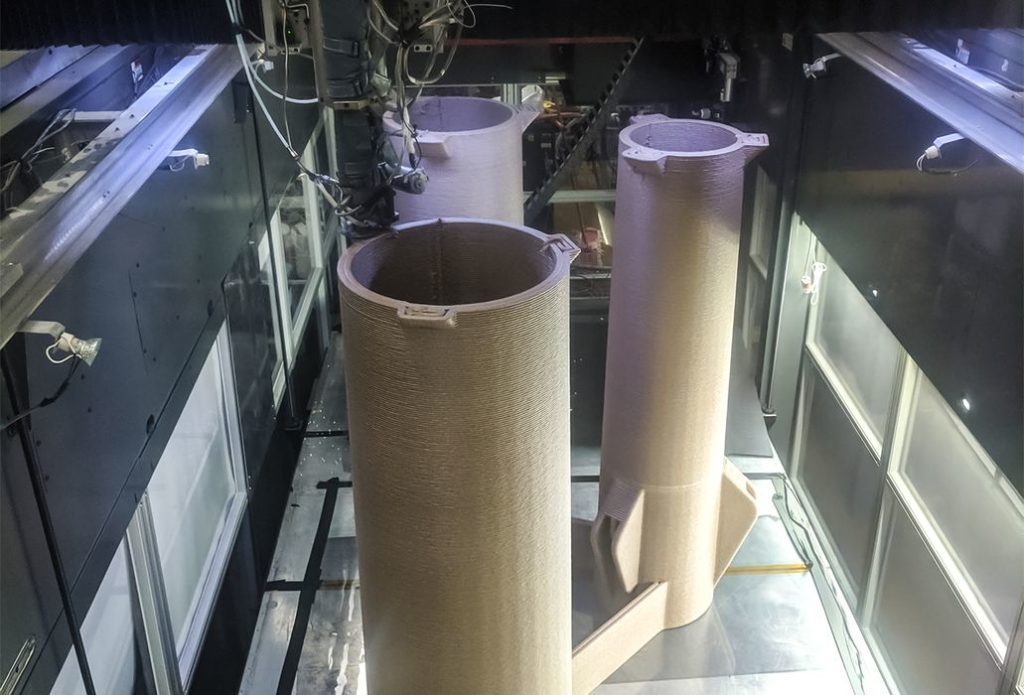
Researchers have developed a method of successfully 3D printing power poles for practical use in the field.
Power poles are typically made with natural wooden poles, but they must be of sufficient size and strength to be used. With an increasing emphasis on retaining forest, the notion of chopping down trees for this purpose might need an alternative approach.
That was the goal of researchers at the Oak Ridge National Laboratory, where they worked with a number of hybrid natural materials for producing functional power poles.
The project experimented with several composite materials, including cellulose ester, recycled polycarbonate and bamboo fiber-reinforced polystyrene. All were strengthened further with the addition of glass fibers.
For 3D printing, the project made use of the BAAM system from Cincinnati Inc., which is able to 3D print large objects in relatively coarse layers. Previously this equipment was used to 3D print an automobile body.
But, you ask, “the BAAM 3D printer is way smaller than a power pole, how could this work?”
The approach was to segment the power pole design into modular segments, which provided several interesting advantages over natural wood poles.
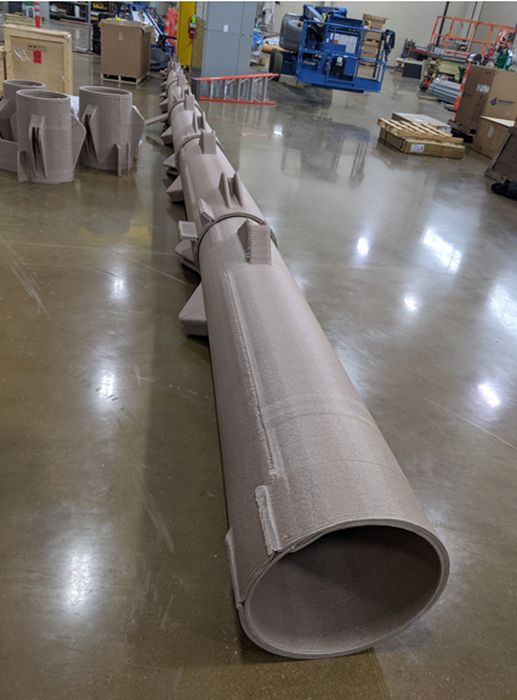
Rather than requiring an entire tree to make a pole, discarded wood material can be used in the composite 3D print material. This is a more effective use of wood material in a world where we have fewer large trees to harvest.
Segmenting the print meant that transport of a pole to the installation site became simpler, as an extra-long transport vehicle would not be required. The segments could fit into a much smaller truck, and then assembled on site.
The weight of the composite 3D printed pole is less than the equivalent wooden pole, so lifting the segments into place is easier and can be done with lesser crane equipment.
Since the pole is 3D printed, it’s possible to include functional features into the design. For example, footpads for power workers to climb are included. It is also possible to include guides for cabling or other features.
Most importantly, the modular nature of the 3D printed power pole means you can mix and match segment types to fit a given scenario. This makes the pole more effective and greatly simplifies field installation work, as it’s instead accomplished through the design.
Is the 3D printed power pole ready for prime time? Not quite yet, it seems, as ORNL explains:
“The ability to 3D print power poles with locally harvested materials such as wood debris and trees makes production and installation more efficient. Future research efforts will focus on increasing production efficiency and improving material performance.”
Via ORNL